The PdM team of Palo Verde Nuclear Power Generation Station has a recipe for oil analysis success. Over the past several years they have documented several “saves” that could have potentially costed over $200,000.
Much of the success can be attributed to a consolidation of maintenance technologies. Early on, maintenance related technologies such as oil analysis, vibration analysis and thermography programs were isolated, each concentrating on maintaining and improving their individual programs.
A company-wide re-engineering effort brought the three together into one predictive maintenance program, under one leader. The move resulted in better communication, synergy, and support between disciplines. Strong support from management helped the effort.
This integration has led to improved fault detection, each technology picking up where the others leave off, with some overlapping.
Prior to introduction of a Palo Verde lubricant test lab, the lubrication program used off-site services for all of its oil testing. The off site services testing effectiveness was limited by the nature of the very basic test package used and the limited understanding of the meaning of the data provided.
The lubrication program was not able to function as effectively as the vibration program. That began to change with the decision to implement an on-site lubrication testing strategy.
A comprehensive testing strategy was developed and instrumentation was purchased that allowed equipment condition monitoring well beyond the level previously supplied by the outside service. Microscopic evaluation techniques became routinely performed tests.
Oil chemical condition monitoring was dramatically improved with test methods appropriately targeted to additive effects and depletion. With the enhanced technical capability and the use of a highly skilled and dedicated lab staff, the lubrication and vibration program obtained equal footing.
With two independently strong programs available, true integration began.
An important monitored condition is in bearing failure forecasting. The vibration technology is seen as a better forecaster of late stage bearing failure while the lubrication program is better at identifying early stage bearing conditions.
Wear begins at the micron size level and deposits itself in the lubricant. The defects are too small to cause a flaw that can be monitored with vibration techniques. Together, the programs are able to monitor a failure in excess of a year to failure. The long term planning has advantages in pre-planning and scheduling maintenance.
Watching a failure progress over time has the added advantage of allowing ‘root cause’ evaluations in this power generation station. Wear debris in oil can be evaluated microscopically to establish probable failure mechanism such as fatigue, abrasion or lube failure. This information can often be correlated to a cause such as misalignment, unbalance or mechanical looseness. Data points from both technologies can help narrow the root cause of the condition.
The final step in completing the root cause is an examination of the parts after they have been removed. Severely degraded and worn parts are difficult to evaluate. Advanced wear often removes the evidence of the initial failure mechanism. If root cause evaluation is treated as an important part of a program, attempts should be made to remove machinery from service prior to advanced failure stages.
The on-site oil analysis program was expanded. The PdM team uses Rotrode Filter Spectroscopy to detect wear metals in the oil. If high ferrous content is detected, a ferrogram is made to help determine the source of the problem. If high non-ferrous content is detected, a filtergram is made using an eight micron membrane.
A proactive strategy was initiated for all aspects of lubricants. Whenever an order of oil is delivered it is isolated and then tested before acceptance. Each oil is tested for additive level, viscosity and then a 100-ml sample of the oil is filtered through a 3-micron filter paper for less viscous oils and an 8-micron filter paper for more viscous oils to check for contaminants.
Education is a big part of the success at Palo Verde Power Generation. All mechanics have gone through continuing lubrication, vibration and thermography training.
In one year, the predictive maintenance department documented approximately $3.7 million in savings. Johnson points out that for every $1 dollar spent, at least $6.50 in maintenance costs has been saved over the last 3 years.
Ref: Johnson, Bryan, Maxwell, Howard, “Integration of Lubrication and Vibration Analysis Technologies”
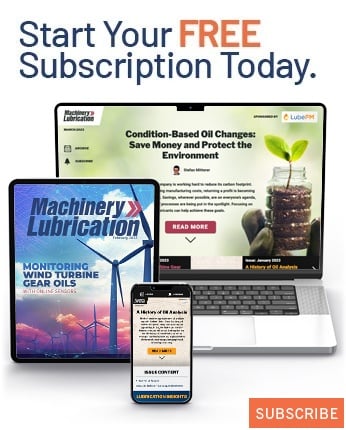