Whether you currently have an oil analysis program in place, or are putting one together, it is imperative to ensure that equipment is properly sampled to meet the goals of a specific maintenance program.
To provide the program with the proper foundation, six basic questions must be asked:
-
What do you want to get from your oil analysis program?
-
What units need to be sampled?
-
Where does the sample need to be taken on the equipment?
-
How are the samples going to be procured?
-
How often do samples need to be taken?
-
What tests are needed?
Some of these steps can be performed simultaneously, while others must be done in sequence.
Step 1: The Functions of an Oil Analysis Program
This first step is critical. It provides the direction for nearly all future decisions regarding the oil analysis program. Can failures be caught early? Are there lube-mixing problems that need to be prevented or caught before resulting issues occur? Or does the lubricant health simply need to be monitored to provide accurate lube change intervals? The reasons for performing lubricant analysis can vary, but overall, the choice can have the most effect on what can be accomplished with an oil analysis program.
Step 2: Sampled Units
The next problem to tackle is deciding which units to sample. Individual units do not need to be determined immediately, but for other steps later in the process, it will be necessary to decide what unit types to sample. Gearboxes only? Super-critical units? Everything? This step can be one of the most challenging, but when all of the fundamentals are combined, it is relatively simple due to the limiting factors some steps provide.
The most likely solution is to make a list of everything the user might want to sample and then prioritize them into groups (definitely want to sample, would like to sample, must be sampled). Therefore, if the cost is too prohibitive, the units can be pared down to sampling either less often or not at all.
Step 3: Sampling Location
While this step can be performed in any order, it is useful in helping place limits on the scope of the sampling project. Sample location is sometimes cut-and-dried regarding where the sample can be pulled from on the equipment.
The pros and cons of each sampling option must be weighed against many variables including questions such as "What does the budget allow with the number of units that need to be sampled?" and "Which sampling method will allow me to monitor what I need to reach the goal of this project?" In some instances, drop tube sampling is appropriate. Other instances require a sample point to be installed to obtain accurate and useful data.
Selecting the proper location on equipment may not be as easy as it seems. If the wrong type of sampling is performed or the sample port is placed in an inactive zone, a unit may end up failing while the data analysis continues to show positive results.
Safety can also be an issue. Is the unit a high-pressure hydraulic? Be sure to check that if a sample port is being installed, the pressure rating is within the proper range.
Step 4: Procuring the Sample
If the drop tube sampling method is chosen and only diesel engines are used, this choice is an easy one. Buy a vacuum gun and get to work. If, however, there are challenges with ensuring the proper location has been chosen for taking samples, this can be a significant problem. There are many reasons why particular units cannot be sampled at any point in time.
There is always going to be a unit that just doesn't have a feasible solution, but there are typically solutions for problems if one is willing to dig in and search. Make sure that when the equipment and sampling method have been selected, the ability to pull the sample exists as well.
If you encounter a problem while searching for a way to retrieve samples from a piece of equipment, the equipment vendor may be able to provide a solution. If there is no equipment vendor available, look up a sampling equipment vendor on the Internet (or just continue looking through this magazine - there are usually several). If the first vendor cannot find a solution to the problem, try another one.
Step 5: How Often is a Sample Needed?
Sampling frequency can be dictated by two factors: what the user is trying to find and how fast it needs to be found. Cost can also be factored in because monthly sampling is not always an option. However, if cost for having the analysis completed becomes a major issue, the scope of the sampling project may have to be changed to effectively limit sampling to a financially manageable situation that doesn't involve randomly removing units from the sampling plan.
When determining the frequency of sampling, issues such as the likelihood of failure and equipment history should be addressed while deciding which interval to set up the equipment.
The more frequently sampling takes place, the more effective one will be at discovering problems before a failure occurs. Most oil analysis users have heard stories involving a failure that went from inception to disaster in a matter of days. While this is the exception rather than the rule, keep in mind that failures can happen quickly, and it is necessary to limit exposure to that magnitude of failure on units that will cripple operations if they go down.
A functional equipment history may be the difference between a good call and a complete miss with the analysis. A unit sampled yearly to monitor oil will not provide the analyst with much equipment history. Quarterly sampling may be the beginning of a stable and trendable equipment history, and with monthly sampling, there is a 90 percent range of problem detection before failure.
Step 6: Tests
Which tests are needed is strictly determined by what one wants to find with the testing. Viscosity and acid number tests may be useful if it is just to monitor lubricant health. To monitor equipment health, metals and ferrous density testing may be the route to take. Most oil analysis users look for a combination of equipment health, lubricant health and lubricant cleanliness.
Many oil analysis providers offer discounted packages for oil analysis geared toward general equipment types, so be sure to ask for any packaged tests that receive a discount to meet specific needs.
In conclusion, if all of these fundamental questions are brought to the table when traveling down the path of lubrication excellence, and the answers have proved appropriate, then an effective program which has a solid foundation and a rewarding outcome should be in place.
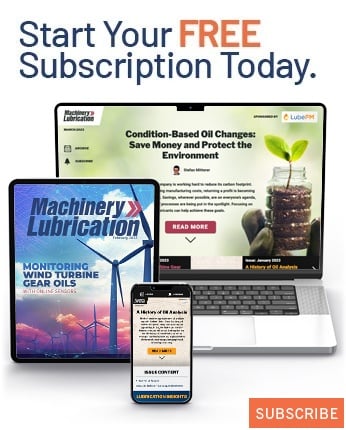