It's often said that an oil analysis program is a metric of the overall health of a lubrication management program. If this is true, then why is oil analysis seldom used as such? Sure, it gets used, and sometimes well-used, to manage machine health and detect incipient problems on an individual machine-by-machine basis.
Unfortunately, however, it is rarely used to actually measure the health of a lubrication management program as a whole. Although oil analysis statistics are not the only measurements of the health of an oil analysis program, they are the focus of this article.
Useful Data
A more thorough analysis of the plant's oil analysis results is needed, as well as some statistics and metrics that can be generated on a monthly basis. It is important to be able to perform this analysis. If a lubrication excellence program has been initiated at a plant, then capital funds have likely been provided, and if so, sooner or later a cost benefit analysis of the investment must be provided. The useful information generated is going to be a function of the data the laboratory or oil analysis software provides.
Many labs are able to produce a monthly report of samples analyzed. This analysis tends to be rather general, but may still be useful. If this is not already being provided, request one. Also, most labs are able to provide the sample data in an electronic format that is easily importable into a spreadsheet or database. Such data can provide more than a standard monthly report, but will likely take some extra manipulation to convert the data into meaningful information.
The Common Statistic
The statistic that is most commonly tracked is the ratio of normal to abnormal samples. This is an important statistic, but is rather basic. It does nothing to indicate if abnormal problems are the result of contamination, fluid properties, or if they are wear-related.
This type of dimension is comparable to the acid test that financial analysts use as a basic measurement of a company's health. It is readily obtainable, indicative, but certainly does not encompass the whole picture.
A more advanced approach is to categorize the normal to abnormal ratios according to fluid condition, fluid contamination and wear. Abnormal machine wear is directly more damaging to the bottom line than fluid properties or fluid contamination, and should carry more weight in the decision-making progress.
Grouping by oil analysis category may be performed automatically by the lab, but most likely it will be left to the individual. Although I have never tried tracking these parameters personally, I suspect that an improvement on the contamination ratio will be followed shortly by an improvement in the fluid condition and machine wear ratios.
The analysis of normal to abnormal ratios can be broken down into even more granular categories: machine wear into particulate and nonparticulate wear; contamination into water contamination, dirt contamination and possibly soot contamination in the case of engines; and fluid properties into mature and premature degradation. Once again, these categories, if tracked, need to be provided by the laboratory or oil analysis software.
Conducting an Analysis
The most useful method of analyzing results is actually quite simple, providing laboratory results can be accessed in an electronic format. The basic process is to generate monthly averages of key oil analysis results. However, how the tests are interpreted requires additional consideration.
Here are some concepts that need to be considered when conducting a statistical analysis of individual oil analysis tests:
-
The first step involves grouping machines according to type. From a purely operational viewpoint, it is reasonable to expect that the oils in process pumps are more susceptible to liquid contamination than adhesive wear generation. It is just as reasonable to expect the oils in heavily loaded gearboxes to be more likely to suffer from excessive adhesive wear metal generation than liquid contamination. Averaging machine wear or water contamination out on a plant-wide basis rather than a machine-type basis may show acceptable results for both pumps and gearboxes, but will not highlight the critical differences between the two machine groups. Results must be compared on a machine type-by-type basis, rather than a plant-wide basis.
-
The second step is to break machine types into different oil types. This may not be necessary in all plant situations. But just to illustrate its importance, consider a plant using invert emulsions in some fire-resistant hydraulic applications. An invert emulsion is typically about 40 percent water by volume. If monthly water contamination is measured on a hydraulics-wide basis rather than separating oil and invert emulsion categories, the results would obviously be biased.
-
The third step is to treat the oil analysis tests that are use- and nonuse-dependent differently. This is a more advanced technique, and will be the subject of a future article.
The third step is advanced, yet it may not need to be applied to obtain quality metrics to measure the health and performance of a lubrication management program. Assuming the results can be imported into some type of data analysis software (like a spreadsheet or database), the following steps must take place:
-
Group the oil analysis results by month.
-
Group the monthly results by machine type.
-
If fluids in the same machine group have varying properties, group them separately.
Now that the samples are correctly grouped, for each group you must perform the following:
-
Average out the particle counts. This can be achieved by averaging each size category, only the four-, six-, and 14-counts, or simply by averaging the ISO 4406:99 range digits.
-
Average the water contamination numbers.
-
Average known contaminant indicating elements (silicon and aluminum for dirt, calcium in a limestone or cement environment, etc.).
-
Average wear data, such as elemental iron or ferrous density. While useful in themselves (unless use-dependence is considered), these parameters can make a well-performing program look mediocre.
Graph the analyses and prominently display the plots. There is nothing like a steep line on a chart to grab people's attention!
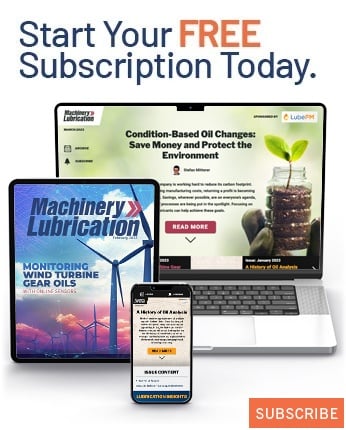