Proper lubrication facilitates uninterrupted machine operation and is one of the most important aspects of machine health and efficiency. The most common industrial lubricants primarily consist of a base oil and are either mineral-based, synthetic, or vegetable-based. Additives are also added to the base oil to optimize the properties of the lubricant. Another form of lubricant, grease, is made by combining a base oil with a thickening agent.
Why is Lubrication Important?
It serves many purposes, but the ultimate goal of a lubricant is to reduce unwanted friction (the resistance encountered when solid surfaces slide against each other). This friction reduction is accomplished by separating two solid surfaces with a thin layer of lubricant.
Friction, unabated, can cause many problems for machinery. Every metal surface within a machine, no matter how finely finished, will have some degree of roughness, with high points called asperities. As the surfaces move past each other, these asperities come into contact and catch on one another.
As the asperities catch and move, they rip each other apart, causing abrasions and adhesion, and in some scenarios, they can even weld and seize together. The pieces of metal torn from the component surfaces become free-moving particulates and are introduced to the machine’s lubrication system, causing further problems. Additionally, friction produces heat which, if unchecked, can quickly degrade the lubricant and cause catastrophic machine failure.
Beyond friction reduction, lubricants can also provide:
- Heat control — The heat created by friction is absorbed and transferred by the flowing lubricant. Additionally, heat generation is reduced by the lubricant’s reduction of friction.
- Contamination control — Grease and other lubricants can be used to create a seal between a machine’s internal components and the external environment, which prevents the ingress of contamination. In addition, lubrication circulating within a machine can carry contaminants to a tank, sump or filter, where they can then be removed.
- Protection against chemical attack — Lubricants and their additives can coat the surfaces of machine components, protecting them from corrosion, such as rust.
- Transfer of energy — Hydraulic oil, because of its incompressible nature, is used to transfer energy within a hydraulic system.
What is Lubrication?
As stated above, there are three types of base oils used in a lubricant: mineral, vegetable, and synthetic. Vegetable oils, because of their lower oxidative stability and limited flow properties at cold temperatures, are seldom used for industrial purposes; instead, mineral and synthetic base oils are often used in industrial applications.
- Mineral — Derived from crude oil, the quality of mineral oil depends on the refining process. Mineral oils are generally made up of four different types of molecules — straight paraffin, which have a long, straight, chained structure; branched paraffin, which have the same structure as paraffin molecules, with a branch to the side; naphthene, which have a saturated ring structure and are most commonly used in moderate temperature applications; and aromatic, which have a non-saturated ring structure and are primarily used in the manufacturing of seal compounds and adhesives.
- Synthetic — Making up a smaller fraction of lubrication oils used for industrial purposes (primarily because of cost), synthetic oils consist of man-made or highly modified molecules. There are several types of synthetic oils with various properties. Despite their higher cost compared to mineral oils, synthetic oils are sometimes a preferred choice in certain applications — this may be due to various reasons, but is often tied to the unique benefits of each type of synthetic, such as increased oxidation stability, thermal resistance and higher viscosity index.
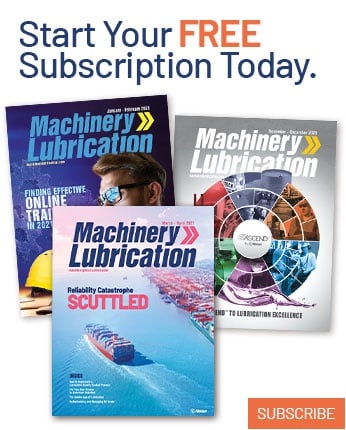