Grease for rolling bearing lubrication provides a separating film between a bearing’s rolling elements, raceways and cages to prevent metal-to-metal contact and associated friction. Grease additionally helps to inhibit wear, resist corrosion and impart enhanced sealing protection against solid or moisture contaminants.
For all of these reasons, and because grease is easy to apply and remains retained within a bearing’s housing, most bearings in rotating machinery (an estimated 80 percent) are lubricated with grease.
Regardless of the application, the condition of grease and the changes in grease properties over time can tell many stories when analysis of the lubricant is performed as part of a predictive maintenance strategy.
But, traditionally, grease analysis has occurred infrequently, usually only when there is suspected contamination, when the wrong grease may have been used or when a failed component is studied to determine root causes. The primary stumbling block has been that a practical, user-friendly methodology to assess grease condition in the field on a regular basis has eluded industry.
Figure 1. Grease analysis can provide important information about lubricant condition and properties.
The development of an innovative portable grease analysis kit offers a solution for users to perform grease condition assessments directly in the field (and as frequently as necessary). Such grease analysis can deliver a wide range of benefits:
- Grease relubrication intervals can be adjusted according to real conditions
- Grease quality can be evaluated to detect possible unacceptable deviations from batch to batch
- Grease performance can be assessed to allow verification of the grease’s suitability for the particular application
- Under-performing greases can be identified to help prevent related damage
The kit’s appeal broadens since no special training is required to perform the tests, no harmful chemicals are involved, sample sizes are purposely small (just 0.5 grams of grease are needed to perform all of the tests) and quick assessments in the field based on immediate results enable timely decision-making.
The kit also contains instructions for use, a report template and guidelines for proper interpretation of test results.
The grease test kit lets users analyze three all-important grease properties: consistency, oil bleeding and contamination. Universal tools supplied for all three grease condition assessments include a sampling syringe, a sampling tube, a permanent marker, sampling containers, disposable spatulas and gloves. Tools specific to a particular test also are provided.
Figure 2. Greases are classified by their consistency, or stiffness.
Consistency
Greases are classified by their consistency, or stiffness, according to the National Lubricating Grease Institute (NLGI) and are graded from NLGI Class 000 (very soft) to 6 (very stiff). Classifications are based on the degree of penetration achieved when a standard cone is allowed to sink into the grease at a temperature of 25 degrees Celsius for a period of five seconds.
For normal use in bearings, grease consistency usually ranges between NLGI Class 1 and 3. Lower-consistency greases will be recommended for low-temperature applications or for improved ability to pump; greases with higher consistency will suit bearing arrangements with a vertical shaft.
The kit’s test for consistency involves a fixed grease volume spread between two glass plates by means of a calibrated weight. By comparing the stain to the calibrated measuring scale, you can directly determine the NLGI lubricant class.
This is significant, considering that bearing failures attributed to poor lubrication often can be caused by mixing incompatible greases with different properties, leading to inconsistent lubricant.
Therefore, it is imperative for optimized bearing performance that the correct grease type first be selected to deliver the necessary base oil viscosity in the proper amount at the prevailing operating temperature and that its consistency be maintained over time.
Tools in the kit specifically for the consistency test include a housing, a calibrated weight, a mask and glass plates.
Figure 3. Special paper helps to determine bleeding properties.
Oil Bleeding
Grease must release some of its oil during operation to properly lubricate a bearing. The rate of release is called the bleed rate (or the oil separation rate). Typical oil bleed rates of greases for bearing lubrication are 1 to 5 percent. The base oil viscosity and operating temperature influence the bleed rate, which should be high enough for adequate bearing lubrication.
The kit’s test for oil bleeding properties begins with a fixed amount of grease placed on a piece of special paper. When this paper is heated, base oil is released from the grease, which creates an oil stain on the paper. By measuring the diameter of the ellipse that is formed and comparing it with a fresh sample, the bleeding properties can be evaluated.
Components for use in the oil bleeding test include a USB heater, a USB/220/110V adapter, a special paper pack and a ruler.
Figure 4. The portable kit contains everything that’s needed to perform grease condition assessments.
Contamination
Cleanliness of grease is as important as the proper amount. If contaminated grease is placed into a system, it can cause more damage than a lack of lubrication.
The kit’s test for evaluating contamination uses a supplied pocket microscope to view a fixed grease amount spread between two glass plates. Any contamination becomes apparent.
The Right Grease for the Application
Effective grease monitoring and testing as an integral part of an overall lube management program can tell much about machinery conditions and potential problems. But the entire process can be undercut when the correct grease for an application is not specified and used at the outset.
Although it may be tempting to standardize on a single grease plant-wide to increase purchasing power, all machines operate as highly specialized rotating assemblies, and every asset will exhibit requirements specific to the application.
Mixing greases will prove fatal long-term for machinery and often will have the same effect as contamination. It can be helpful to establish color codes or other visual aids at machinery locations to guide maintenance staff in identifying the proper grease to be used and avoid mix-ups and the damage they can cause.
Over time, the grease in a bearing arrangement will naturally lose its lubricating properties. This underscores the need for careful attention to original lubricant selection and then conducting regular tests of the grease for a better understanding of its condition.
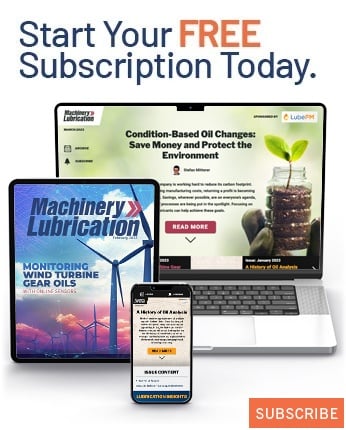