The rolling element bearings used in electric motors potentially have many modes of failure if an incorrect strategy is implemented. These modes include incorrect lubricant selection, contamination, loss of lubricant and overgreasing. This article will discuss several effective strategies to minimize the likelihood that one of these failure modes will happen.
Most electric motors are designed with grease-lubricated, anti-friction, rolling element bearings. Grease is the lifeblood of these bearings, providing an oil film that prevents the harsh metal-to-metal contact between the rotating element and races. Bearing troubles account for 50 to 65 percent of all electric motor failures, and poor lubrication practices account for most of these bearing troubles. Good maintenance procedures, planning and the use of the correct lubricant can significantly increase productivity by reducing bearing troubles and, likewise, the motor failures.
Failures
Get to know the failures. By knowing what the failure modes are, you can focus on reducing or even eliminating them.
Wrong lubricant – It is important to use the correct grease for the application. Regreasing with the wrong grease can lead to premature bearing failure. Most oil suppliers have grease that is specifically designed for electric motors.
Grease incompatibility – Greases are made with different thickeners, such as lithium, calcium or polyurea. Not all greases are compatible with one another, even those with the same thickener type; therefore, it is important to use the same grease or compatible substitute throughout the life of the bearing.
Motor casing full of grease – If the grease cavity is overfilled and high pressure from the grease gun is applied, the excess grease can find its way between the shaft and the inner bearing cap and press its way into the inside of the motor. This allows the grease to cover the end windings of the insulation system and can cause both winding insulation and bearing failures.
Lubricant starvation – This has several possible causes. The first is insufficient grease being added during installation. The second is inappropriate, elongated relube intervals. The third possibility is that the oil has been removed from the thickener base by excessive heat.
Overpressurization of the bearing housing – Anytime there is an overpressurization of the bearing housing, stresses are placed on parts that weren’t designed to handle the pressure. Keep in mind that the standard manual grease gun can produce pressures up to 15,000 pounds per square inch.
Overheating due to excess grease – Too much volume will cause the bearing elements to churn the grease, trying to push it out of the way, resulting in parasitic energy losses and high operating temperatures, which in turn increase the risk of bearing failure.
Getting Started
The first thing you need is a plan to execute. The following would be the bare minimum that would need to be discussed and implemented to get the program started.
- Make an equipment list that includes all of the assets you want to include in the program.
- Verify the type of bearings installed in both the inboard and outboard ends of motors. This will determine if the bearings are regreasable. You also should determine a policy for the regreasing of shielded bearings, commonly found in motors. (Some experts recommend not greasing double-shielded bearings.)
- Choose a grease type that will be adequate for the program. Remember that once a grease type and manufacturer are chosen, it is best not to deviate from this choice.
- Make all necessary modifications to the electric motors. This includes adding fittings and making them accessible.
- Establish a set of procedures for maintaining the motors.
Developing a PM System
There are many choices to make when deciding on a preventive maintenance (PM) system. In some plants, it may be beneficial to only use a spreadsheet, while others have the need for complete, dedicated systems. The end goal is the same: You want to be able to track each motor as an asset and keep track of the attention that each motor receives. Some good things to include in the PM system are: date of installation, horsepower, frame size, rpm, bearing type and environmental conditions. It will take a while to set a system like this up, but once completed, it will be one of the greatest tools you possess.
Determining Lube Type
When searching for a lube type and manufacturer or supplier, there are several things to consider. The following is a list of qualities associated with a good electric motor grease.
- Good channeling characteristics
- NLGI Grades 2-3, ISO VG 100-150
- High dropping point, 400 degrees Fahrenheit at a minimum
- Low oil bleed characteristics, per D1742 or D6184
- Excellent resistance to high-temperature oxidation
- Good low-temperature torque characteristics
- Good anti-wear performance, but not extreme pressure
Polyurea grease is popular with many bearing and motor manufacturers. A good percentage of equipment manufacturers also specify some type of polyurea grease in their electric-powered machinery. A polyurea-based grease is an excellent grease for electric motors, but be warned: This thickener is incompatible with most other thickeners. Some manufacturers don’t recommend mixing one brand of polyurea with another. Instruct your motor rebuild shop on what grease to use, and make sure your grease type is specified on new motor purchase orders.
Determining Regrease Time Cycle
There are several methods for determining a regrease time cycle. There are multiple calculators, tables and charts that can give you a very good starting point. I like to use them all to get a good feel for how I want to set the cycles. The real “fine tuning”, however, must be done by trial and error. The factors that most calculators have in common are: load, operation time, bearing type, temperature, environment and speed. This is where the database you built will be beneficial.
Alternatively, a better solution is to forgo a time-based cycle altogether and grease bearings based on the condition of your bearing, rather than time.
Grease Volume Control
Grease volume control has been a longstanding problem for industry, and simply following OEM recommendations may not be enough to solve this problem. Unless you've installed an automated regreasing system that calculates grease volume and dispenses grease for you, there exists an equation that has yet to fail me. It is a simple equation that takes a very logical approach to determining the volume of grease to be added. The formula is:
G = [(.114) x D x B]
Where G = the amount of grease in ounces; D = the bearing outside diameter in inches; and B = the bearing width in inches.
Once the volume is found, you need to convert it into shots, or pumps of the grease gun. There is only one way that I know of to get the value used to convert the number. You will need the grease gun that is going to be used and a postal scale. After finding the output per full stroke of the handle, label the gun so that it is now “calibrated”. The average value I’ve found is approximately 18 shots per ounce for most manual guns.
The Procedures
The intent of a good maintenance program is to extend the service life of your motor. In most cases, improper lubrication procedures or the failure to follow them can have a negative impact on your program. A good base set of procedures should include some variation of the following:
- Ensure the grease gun contains the appropriate lubricant.
- Clean the areas around the relief and fill fittings.
- Remove the grease relief valve or plug.
- Grease the bearing with the proper, calculated amount of grease. Add grease slowly to minimize excessive pressure buildup in the grease cavity.
- Watch for grease coming out of the relief port. If you pump excessive amounts of grease into the motor and the old, used grease is not being purged, stop and check for hardened grease blocking the relief passage.
- If regreasing is performed with the motor out of service, operate the motor until bearing temperature raises to operating temperature to allow for thermal expansion of the grease. Ensure that the relief valve or drain plug is left out during this process.
- Allow the motor to run at this temperature for a short time to expel any excess grease before installing the bottom grease relief valves.
- After excessive grease has been purged, reinstall the drain plug and clean excessive grease from the relief port area.
This article was written as a very broad and general document to inform you of some of the thought processes that go into the creation of a lube program. It may seem like an easy task to take on, but in reality, it is very difficult. Remember to take your time, do it right the first time and you will find the rewards are very much worth the trouble.
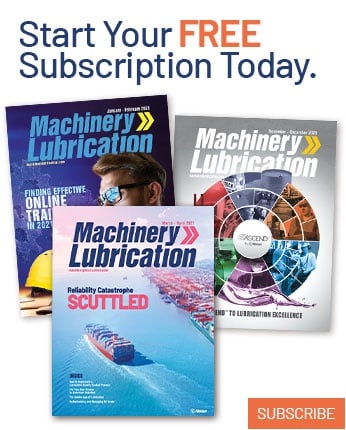