Oil analysis and vibration analysis are natural partners for machine condition monitoring. This, unfortunately, hasn’t always been the perception. In the early days of the modern condition monitoring era, these two powerful technologies were viewed to be in competition with one another – vying for the same condition monitoring resources. Time has allowed most people and organizations to see the value of integrating vibe and oil. For root cause management, they team up to provide control over the “big five” root causes of machine failure. Vibration analysis enables the control of balance, alignment and looseness. Oil analysis enables control over lubricant quality and contamination. They are also a great pairing on the predictive side of condition monitoring.
The strengths of vibration analysis counteract the limitations of oil analysis and vice versa in managing the health of specific machine types. In this issue, I’m going to share some philosophies for pairing oil analysis and vibration analysis for managing the reliability of common mechanical equipment in your plant. These short vignettes are by no means comprehensive, but rather are intended to make you think so you can start to formulate your integrated condition monitoring solution for mechanical plant equipment. I’m covering enough types to ensure that you get the idea and can think through your specific applications.
Gearboxes
Just about every plant in the world employs gearboxes. A gearing application is a rough application for most lubricants because of the high heat, aeration and the presence of chemically active particles, such as brass and steel. Also, contaminants are always present that weaken the lubricating film strengths and interfere with critical lubricant film clearances. Likewise, misalignment, unbalance and looseness are a risk to a greater or lesser degree depending upon the configuration of the machine train and what the gearbox is coupled to and the coupling mechanism. As with most machines, vibration analysis and oil analysis are required for proactive control over the root causes of mechanical wear and failure. As previously mentioned, the proactive aspects of integrated condition monitoring apply to most of the machine types discussed herein – gearboxes are our example and are certainly no exception to the rule.
Occasionally, gears go bad. The most common failure modes are gear tooth wear and gear tooth fracture. Detecting wear-related gear faults with vibration analysis can be challenging because there are so many competing vibration signals – particularly at slow speed, where the amplitude of the vibration signal may not be strong enough to overcome the noise factor. However, oil analysis provides excellent resolution in detecting contact fatigue, abrasion and adhesive wear, making it a great choice for the early detection of these failure modes.
If a gear tooth breaks away from the shaft, it is unlikely that the failure will produce a detectable concentration of wear particles – particularly if the failure is caused by a sudden impact or defective material. However, monitoring the gear mesh frequency with vibration analysis will nail a broken tooth each time. Together, vibe and oil analysis make a powerful combination for managing the health of gearboxes.
Paper Machines
Having cut my teeth in oil analysis, I have always struggled with paper machines. We like to collect return line samples where we get a high concentration of information about the bearings before the oil goes to the tank. The problem is that a paper machine has hundreds of these bearings. If you collect a sample from the common return line header, the information generated from any single bearing gets lost. And, it’s impractical to set up 200 bearings for routine individual return line sampling.
Paper machines employ rolling element bearings – a real strength for vibration analysis. My approach - I like to sample the oil going to the bearings to make sure the oil is clean, dry and healthy. Then, I rely on vibration analysis to monitor the condition of the individual bearings themselves. The advanced player installs sampling valves on the individual return lines from each bearing, but only samples them on-condition – when vibration analysis or some other condition monitoring technology points to a problem. We typically analyze these samples qualitatively using particle microscopy to evaluate the nature and severity of the event. This helps with planning and scheduling, prioritization and cause analysis.
Oil Lubricated Centrifugal Pumps
Like paper machines, pumps have rolling element bearings – making them a natural for vibration analysis. However, because they are small-sump systems, they get a great concentration of wear debris. For sump lubricated systems, sampling often constitutes an oil drain, which can be tricky when the pump is operating. For these systems, I prefer to employ a statistical sampling approach to time oil drains and manage contamination and rely on vibration analysis for primary machine condition monitoring. Much like paper machines, we can install valves on pumps to sample on-condition to aid in troubleshooting.
Grease Lubricated Electric Motor
Again, these are usually rolling element bearing applications – a strength for vibration analysis. Traditionally, I would rely solely on vibration analysis to monitor a motor’s mechanical condition. However, with the advent of “Grease Thief” sampling devices, we can now extract a reasonably representative sample of grease to detect mixing, grease degradation and wear particles.
Reciprocating Combustion Engines
Vibration analysis is the primary condition monitoring tool for grease lubricated electric motors, but oil analysis owns condition monitoring for reciprocating combustion engines, irrespective of fuel type. Engines simply create too many different vibrations for traditional vibration analysis to be effective. Oil analysis, on the other hand, is ideal for the application for several reasons. First, the combustion process itself must be monitored to detect excessive soot generation and fuel dilution of the lubricant. Also, we must always be watching for coolant contamination, which severely compromises lubrication. Because engines are enclosed, wet-sump lubrication systems oil analysis effectively identifies ring, liner, bearing and other sources of wear with a high degree of effectiveness. For mobile plants, oil analysis is the primary condition monitoring tool for the entire drive train. For fixed equipment, vibration is useful for monitoring the health of other parts of the machine train (e.g., generators and pumps).
Hydraulic Systems
Hydraulics systems are the most difficult to typify because they can take so many different forms. Some have gear pumps, others employ vane pumps and still others are equipped with axial piston pumps. Speeds and load vary as a function of the application and the machine’s duty cycle. Some are equipped with cylinders, while others utilize motors. It’s really all over the board. Oil analysis is generally the lead technology for hydraulic systems, assuming we can obtain a return-line sample before the filter. However, vibration analysis is useful for vane pumps, gear pumps, drive motors and hydraulic motors, assuming we can fix speed and load during the sampling process over time. Vibration analysis is not useful for monitoring cylinder health or axial piston pumps. A note on piston pumps, a case-drain sample is often preferred for monitoring the health of the pump because debris shelled out by the pump tends to concentrate there.
Slow-Speed, Grease-Lubricated Pillow Block Bearings
Pillow block bearings are a challenge all the way around. While they are typically rolling element bearings, the low speed makes it difficult to detect problems with vibration analysis until very late in the failure process. Likewise, because they’re grease-lubricated, the challenge in gathering a representative sample creates a challenge for oil analysis. The new Grease-Thief sampling method helps to overcome some of these challenges.
Once considered enemies in the battle for scarce condition monitoring resources, we now view oil analysis and vibration analysis as essential complementary condition monitoring methods for managing the reliability of the entire plant. Both are required to manage the “big five” root causes of machine failure. And on the predictive side of condition monitoring, the strengths of oil analysis help to overcome the limitations of vibration analysis and vice versa. It’s truly a match made in engineering heaven!
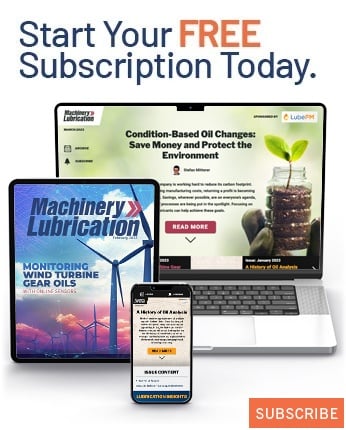