The increasing complexity of today’s hydraulic systems means there is a lot to know about proactive and predictive maintenance in order for optimum reliability outcomes to be achieved. It’s my observation though, that this increasingly specialized knowledge is grossly undervalued in the marketplace. And despite my loud and regular protests to the contrary, it seems the Holy Grail of all hydraulics-related skills is and always has been: fault-finding.
Yes, whether you and I like it or not, the crack trouble-shooter, the man who can cast his eye over the most complex of hydraulic systems and quickly zero-in on the fault without breaking sweat, is ‘top-gun’ in the hydraulics world. He’s a soldier of fortune. Admired by some; envied by the rest of us.
But there’s no need to be awestruck. Hydraulic troubleshooting can be challenging at times, but in the majority of cases it’s usually straightforward. Consider the fundamental structure of any hydraulic system for a moment: A positive displacement pump (or pumps) producing flow which is directed to an actuator (cylinder or motor) to move a load.
When pump flow meets actuator load, the resistance of the load and the positive displacement nature of the pump means pressure is developed. Once pressure is developed there are two possible outcomes—both of which usually occur simultaneously to some degree:
1. The load moves (work is done); and
2. Flow escapes from the pressurized circuit to either the tank or the atmosphere (power is lost).
But if the amount of power lost becomes noticeable, i.e. the movement of the load becomes unacceptably slow—when compared to its ‘normal’ speed, or pressure is noticeably lower (due to the volume of flow being lost from the circuit) then by definition, we have a problem. So when you think about it, in the majority of troubleshooting situations, the task is to find the missing flow, or more correctly, the component which is allowing an abnormal amount of flow to escape from the circuit—without doing any work. In other words: it’s a flow-chasing exercise.
And here’s a list of the tools—and some of the cunning techniques, available to a savvy flow-chaser:
Stop Watch
The speed of an actuator (or actuators) is determined by flow. And so accurately timing how long it takes for an actuator to complete its cycle—combined with a logical process of elimination, can be used to isolate flow loss.
As an example, consider a hydraulic excavator with four main-pumps. The operator complains that the machine is slow. While it’s not certain to be one of the pumps, it’s usually not a bad place to start. The pumps can be ‘tested’ individually (and relatively quickly) by recording the cycle time for each, and comparing the results. To do it, the attachment (stick and bucket) is fully extended and the bucket is placed on the ground. The displacement controls of three of the four pumps are isolated (electrically or hydraulically) - so only the pump being clocked produces flow.
With the engine at high idle and starting with the bucket on the ground, the operator fully summons the boom up on the joy stick and the time it takes to fully extend the boom cylinders is recorded. This process is repeated for the other three pumps and their times recorded. Let’s say the results look like this:
Pump 1: 29 seconds
Pump 2: 36 seconds
Pump 3: 29 seconds
Pump 4: 30 seconds
As you can see, pump 2 is 20 percent slower than the other three. However, before condemning this pump, other components that are unique to pump #2’s circuit and which could explain the loss of flow (a relief valve, for example) need to be eliminated. This could involve confirming the correct setting of all relevant valves and taking another cycle time. And it could involve reaching for another diagnostic tool in the cunning flow-chaser’s armory ...
Infrared Thermometer, a.k.a. Heat Gun
When a liquid moves from an area of high pressure to an area of low pressure (pressure drop) without doing useful work, heat is generated. This law of physics can be extremely useful to the savvy flow-chaser when armed with an infrared thermometer or heat gun. Put simply, it means if a component in a hydraulic circuit is several degrees hotter than the rest of the system, chances are it’s a source of abnormal internal leakage.
Going back to the multi-pump excavator example above, using a heat gun to measure the relative temperature of pump #2’s case drain, relief valve, etc. can greatly assist the savvy flow-chaser’s logical process of elimination.
Photocell Tachometer
Flow is speed and the speed of a rotary actuator (motor) is measured in RPM. So like the stop watch, a photocell tachometer is another handy tool when tracking down missing flow.
For a simple example, consider troubleshooting a hydraulically driven, air-blast heat exchanger circuit—see figure 1. One of the variables which determine the cooling circuit’s effectiveness is fan speed. If fan speed drops off, so does air flow through the exchanger core and therefore, heat transfer is diminished.
Figure 1. Simple cooling fan circuit
A photocell tachometer can be used to measure fan RPM and confirm this one way or the other. If fan speed is slower than it should be, the component responsible for the escaping flow (fan pump, fan motor, bypass valve or relief valve) then has to be determined through a logical process of elimination. This requires some intervention in the circuit—see figure 2. The bypass valve can be eliminated as a suspect by installing a ball valve as shown and then checking fan motor RPM again with this ball valve closed. Next, the fan pump can, in effect, be flow tested—and the setting of the relief valve confirmed, by installing a pressure gauge and needle valve as shown in figure 2.
Figure 2. Cooling fan circuit with additional components installed for troubleshooting
The needle valve is used to load the fan pump, while pressure is monitored and the photo cell tachometer is used to measure flow downstream (by counting fan motor revs). If fan speed drops off markedly as the needle valve is closed—but before the relief valve cracks open, then this indicates the pump has excessive internal leak. On the other hand, if fan RPM remains fairly constant as the needle valve is closed—and we’re certain the relief valve is not passing, then by process of elimination, the fan motor must be leaking excessively. Note that the combination of the pressure gauge, needle valve and photocell tachometer counting motor RPM is a crude but effective flow-meter. And a flow-meter is the ultimate flow-chaser’s tool ...
Flow-meter/tester
The reason it’s last on this list is because it’s the most expensive. And because they’re expensive (a good hydraulic flow-tester can run to several thousand dollars or more) it means, even though it’s usually the best tool for the job, it’s also the one least likely to be available to you. But if a flow-tester is available it increases the flow-chaser’s options considerably. The downside is a flow-tester must be installed in the circuit being tested. This takes time, requires suitable adaptors, and carries the risks inherent in opening the system – such as oil spill and the ingression of air and other contaminants.
For these reasons, a flow-tester is not always the first tool a savvy flow-chaser will reach for. A good example of this is the multiple-pump excavator discussed above; individual pump cycle times can usually be taken much faster (and more safely) than performing a flow test on each of the pumps. So the next time your hydraulic machine develops a fault, don’t be overwhelmed. It’s quite possible it’s just a flow-chasing exercise. And now you have four tools which can be used in different ways to achieve the same result. The good news is, the first three are not expensive and when used correctly, they can be just as effective as the fourth!
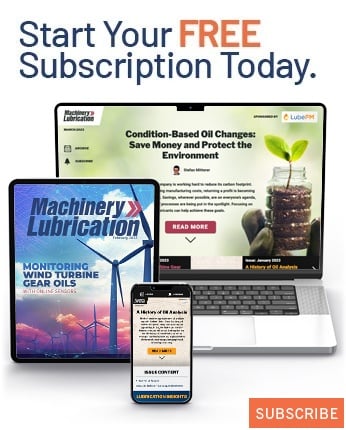