Joining my sister at the emergency room for an issue with her son was an enlightening moment. The ER doctor walked in, reviewed some historical records on my nephew and began asking questions.
As any mother would do, my sister gave the doctor a wealth of information, both relevant and not so relevant, to the current situation. It was the doctor’s job to filter the information and determine what was truly important and helpful. He kept pressing for more information and grilling my sister for clarification on even the smallest comment, which to her may have seemed inconsequential, but to him was significant.
I couldn’t help but realize that this scenario is repeated quite often in our world of oil analysis, with a few changes in characters. In oil analysis, the patient is a machine. More specifically, it is a component of something larger. The end user has the vested interest in the health of the component, and the person evaluating the oil sample data is the doctor.
Example of an Oil Analysis Program Strategy
A survey of 3,000 rotating assets showed that there were 1,500 oil-filled components (including pumps, gearboxes, hydraulic and lube oil reservoirs). In theory, there could be 1,500 oil samples collected at some interval. Studies showed that this was not financially feasible, and therefore the following criticality-based strategy was implemented:
In the case of evaluating oil sample data, it is important to realize that few problems can be resolved based on a single data set or a single test. Like the doctor in the ER, an oil analyst needs to have some historical data on the component being checked.
This means the analyst must know the right questions to ask and have the ability to hear what is being said, not just listening to the words.
One of the first questions to ask when reviewing oil analysis data is, “What is the objective of the plant for this specific component?” It is fully possible and often quite warranted to have a different oil analysis strategy for different components assigned to the oil analysis program.
The appropriate oil analysis strategy should be assigned based on component criticality. During the development of component criticality, a whole new set of issues arises, including:
• Health, safety and environmental effects if failure occurs
• Production loss impact due to failure
• Potential costs of repair due to failure
• Historical mean time between failures (MTBF)
• Effectiveness of early warning systems
Understanding component criticality is absolutely vital in establishing an appropriate oil analysis strategy. I was recently in a mill where components were added to the oil analysis program on an ad-hoc basis. In short, if a component failed, it was then added to oil analysis.
At another mill, the maintenance manager wanted all oil-filled components to go through oil analysis. Obviously, neither of these strategies will end with the desired result, which should be early identification of potential failure using a proven method to cost effectively monitor equipment condition.
Test Slate and Test Interval
The next question to be asked should be, “Is the current test slate and test interval capable of supplying the information we need to meet the plant objectives for this component?” Read How to Create an Effective Oil Analysis Test Slate for more detail on this.
When developing an oil analysis strategy, we must consider two primary components: test slate and test interval. Both of these components may change depending on the strategy taken.
Some of the best oil analysis programs utilize a hybrid approach of on-site and off-site testing. In summary, there is no blanket strategy for oil analysis. The goal is to exercise a method by which a well-developed oil analysis program can be implemented and maintained.
In doing so, the right questions need to be asked with relevant information being supplied to the analyst of the data, whether that analyst is on-site or remote. Once this takes place, we can ensure the program will be in a better position to achieve the desired results at an affordable cost.
By the way, my nephew ended up doing well after his ER visit. If we get it right, our machines can survive simply through the routine visits.
Read more on developing an oil analysis strategy:
Keeping Your Oil Analysis Program Up to Date
How to Select the Right Oil Analysis Lab
How to Justify an Oil Analysis Program
Is Oil Analysis a Waste of Time?
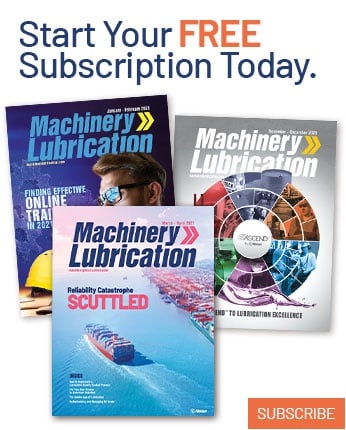