During the last decade, demand for biobased hydraulic fluids has increased, especially for applications in mobile equipment and in close-to-water stationary installations like movable bridges. Motivation for the change comes both from users being more conscious about environmental risks and from government policies to create new markets for agricultural products.
One of the major obstacles in this market conversion is the sensitivity of biobased ester fluids or biodegradable fluids (bio-oils) to contamination with traditional mineral hydraulic oils. Typical situations involve either incomplete flushing during conversion from mineral oil to bio-oil or lack of attention during maintenance and refilling. This has been motivation to analyze the contamination effects in more detail.
Effects of Contamination
With mineral oil contamination levels reaching several percent, problems like excess foam generation, poor air release or filter clogging have been reported during conversions. As a consequence, malfunction or even severe damage to the equipment may occur. For example, in a movable bridge that had been converted, frequent filter changes were necessary during several months following the conversion, returning to normal intervals after that period.
There have been numerous reports about unsuccessful conversions of hydraulic equipment to bio-oil, yet these reports were mostly undocumented and imprecise. There is hardly any literature available about this problem. The experience of hydraulic equipment manufacturers and their fear of expensive warranty claims have resulted in a very cautious and restrictive attitude toward the use of bio-oil.
Biodegradable hydraulic fluids were first standardized by recommendations from the German Machine Manufacturers Association (VDMA), which eventually led to the issue of the international standard ISO 15380. The ISO 15380 standard requires contamination of bio-oil not to exceed 2 percent in the case of the contaminant being common hydraulic fluid and 1 percent in the case of HLPD or engine oils.
Discussions with fluid manufacturers have suggested that the main deteriorating effects may not even be caused by the mineral oil itself, but by metal containing additives that attack the fatty acids in the ester molecules and eventually lead to the formation of soap-like reaction products.
Market Situation and Conversion Practices
Biodegradable and biobased hydraulic fluids have been increasing their market share during the last decade. Despite some progress in the market, the majority of existing mobile equipment still have mineral oil in their hydraulic systems. Companies that decide to order new machines with bio-oil also want to convert their existing machines, reducing the number of different lubricants in their stock. Therefore, conversion of used machines from mineral oil to bio-oil has a larger volume presently than the acquisition of new equipment factory-filled with bio-oil.
Figure 1. Market shares of biodegradable mobile hydraulic fluid
Mobile hydraulic systems only have little more than half of their fluid volume in the reservoir. A very large part of the fluid is distributed in piping, cylinders and other hydraulic components. It is difficult to drain 80 or 90 percent of the fluid without opening connections. As a consequence, reaching a 98-percent drain result of the old fluid in order to obtain a less than 2-percent contamination level for the new fluid is impossible, unless a major maintenance job requiring complete disassembly is scheduled.
To convert to bio-oil and avoid mixing old and new fluids, hydraulic systems need to be flushed, often several times. An example of a volume balance requiring several flush cycles to obtain the desired 2-percent result is given in Figure 2. In this example, it is assumed that after draining, 27 percent of the old fluid still remains in the system. Better draining will reduce the number of cycles.
Figure 2. Volume balance for multiple flushing cycles
It should be clear that this is an expensive, time-consuming procedure. Furthermore, several disadvantages are associated with the 2-percent rule:
- Every bio-oil product is different. Some are more tolerant than others.
- Every mineral oil product is different. Some are more aggressive than others.
- Every hydraulic system is different. Some by design have more tolerance to contamination than others.
- It is difficult to measure the mineral oil content in bio-oil after finishing the flushing procedure.
In addition to these problems, even after successful flushing, contamination risks are also present at later stages, including refilling leakage losses, wrong maintenance instructions, attachment of external equipment and many more.
Experimental Setup
Experiments at the Institute for Fluid Power Drives and Controls (IFAS) investigated relevant properties of biobased oils contaminated with mineral oils. The goal was to obtain an insight of how severe the problem is and to gather information about which effects occur at various concentrations and combinations.
For this purpose, 10 different bio hydraulic products of the HETG and HEES types from different manufacturers were selected. These bio-oils were combined with seven mineral oil products, including a common HLP46 as well as HLPD, HVLP, zinc-free HLP, engine oil SAE 15W-40 and one fossil-based synthetic ester. Engine oil was added to the choice of mineral contaminants because it is sometimes used as a hydraulic fluid. It is also mentioned in the conversion guidelines in ISO 15380 (Appendix A) with an even lower limit of 1-percent contamination. These contaminant fluids were applied in a concentration range between 0.1 and 20 percent, depending on the degree of effects observed during the experiments.
While properties like viscosity, density and the effects on elastic materials used in seals and hoses did not show unexpected changes, it was found that foam generation and filter clogging were the most critical aspects requiring closer investigation. There was also some effect on air-release properties.
It was clear from a previous test sequence that the reactions would take several hours or days to develop, depending on the temperature. At a storage temperature of 60 degrees C, most of the reactions were complete within eight hours. Therefore, all test samples for the following experiments were first submitted to a 20-hour heat treatment at 60 degrees C.
Figure 3. Foam generation after heat treatment
The foam experiments were carried out according to the ASTM D 892 standard, where foam is generated by blowing air into the fluid. The volume of foam was measured twice, immediately after shutting off the foam generation and again 10 minutes later. Having the previous heat treatment performed on all samples, only one foam sequence at 24 degrees C was found to be necessary instead of the three sequences at different temperatures as recommended in the standard test procedure.
Filtration experiments were conducted at 25 degrees C with a paper filter having a 1.2-micron pore size and a 47-millimeter diameter. The pore size was chosen because a growing number of mobile hydraulic systems are equipped with bypass filtering systems with very fine filters.
Flow was forced by a constant vacuum on the downstream side of the filter. For the experiment, three samples of 60 milliliters each were poured through the same filter, recording the time required for each step. Obstructions developing in the filter during the process became apparent by increasing throughput times.
Air release was tested according to DIN 51381, which is almost equivalent to ISO 9120. Air was blown into the fluid under determined conditions. The test requires the measurement of the time until the air content of the fluid is reduced back to a value of 0.2 percent.
From all bio-oils that were tested, two (numbers 1 and 7) were found to be more sensitive to contamination with mineral oil and were investigated in more detail. Both were synthetic esters from different manufacturers with 50 percent or more biobased content and good acceptance in the market.
The mineral oils used for contamination experiments will be referenced in the results with letters as shown in Table 1.
Table 1. Mineral oils used for contamination experiments
Visual Inspection
In most cases, visual inspection could provide an early indication of how severe the changes of the properties would be. Results of the chemical reactions typically appeared as cloudiness, often at the bottom of the container if left still, or as larger particles floating in or on top of the fluid.
Figure 4. Cloudy reaction products (right)
Figure 5. Floating particles
Foam Generation
Foam test results with bio-oil 1 and different contaminants in varying concentrations are shown in Figure 6. The foam volume is indicated twice per sample, immediately after the foaming (upper value) and then after a 10-minute settling time (lower value). In the ISO 15380 standard for bio-oils, the tolerated levels for both are 150 ml and 0 ml, respectively.
Figure 6. Foam test with bio-oil 1 and contaminations
The column at the far left is the pure bio-oil, which demonstrates a good value well below the allowed maximum. Contaminations with hydraulic oils A, B and D show higher but still acceptable results at 2 percent, yet are beyond the allowed maximum at concentrations of 5 percent or higher. The higher the contaminant concentration, the more foam is present even after 10 minutes. In the case of engine oil C, even a 0.5-percent contamination (half of that permitted in the ISO standard) results in unacceptable performance. Interestingly, the last column (zinc-free mineral fluid F) shows that even a contamination as high as 10 percent does not cause any problems in this test.
While bio-oil 1 had good values for foaming in pure condition and was seriously affected by contaminants, bio-oil 7 is average when not contaminated but shows almost unchanged behavior with all contaminants except engine oil C. In the case of engine oil, a content of only 0.5 percent causes problems.
Figure 7. Foam test with bio-oil 7 and contaminations
Figure 8. Foam test result depending on metal content (bio-oil 1)
Since zinc-free mineral oil F seemed not to cause any problems, it was interesting to check the influence of zinc and other metals. For an overview, both values of each foam test were combined and the sum plotted over the total metal content of the mixtures. For bio-oil 1, there was an almost linear functional relationship between metal content and foaming problems. At and beyond 20 micrograms/gram (20 ppm), foaming reached unacceptable levels. In Figure 9, the picture was totally different, where bio-oil 7 showed problems only with engine oil but not with the other oils. Engine oil has a high calcium content, while many hydraulic oil additives are zinc-based substances.
Figure 9. Foam test result depending on metal content (bio-oil 7)
Filtration
As described previously, filter experiments resulted in three consecutive throughput times through the same filter. The bio-oils were first tested in pure condition and then with various contaminants. Pure bio-oil is easy to filter, and all three passes took the same amount of time. For bio-oil 1, contaminations with mineral oils A and B showed a light increase and filter clogging tendency at 5 percent, as well as complete clogging at 10 percent. A clear clogging tendency could be seen with engine oil C at all concentrations from 0.5 percent upward. Adding zinc-free mineral oil F did not cause any changes with respect to the pure bio-oil even at a 10-percent level.
Figure 10. Filter test results for bio-oil 1 with contaminations
Figure 11. Filter test results for bio-oil 7 with contaminations
Bio-oil 7, which was more stable than bio-oil 1 in the foam test, was much more sensitive to mineral oil in the filter test. A 2-percent contamination with common hydraulic fluid A resulted in progressive filter clogging. In this case, even the zinc-free mineral oil F caused minor problems at 5 percent (half of the concentration used for bio-oil 1). Filtering became easier again after passing the 10-percent concentration of oil B, which was a detergent HLPD, where at 20 percent there was less filter clogging than with 5 or 10 percent.
Air Release
Air-release time in the ISO 15380 standard is limited to 10 minutes, a value that is maintained by both bio-oils in pure condition. Adding mineral oils increases the time measured but only in concentrations beyond 2 percent (beyond 1 percent for engine oil C), which is acceptable. Like in the foam test, bio-oil 1 initially was better than bio-oil 2 in pure condition but was more sensitive to contamination.
Figure 12. Air-release test results for bio-oil 1 with contaminations
Figure 13. Air-release test results for bio-oil 7 with contaminations
Conclusion
Some biobased hydraulic fluids sold in the market are sensitive to contamination with common hydraulic fluids. Problems that occur at higher contamination levels reaching several percent include the formation of reaction products that lead to poor filtering, foaming and air-release properties of the mixture.
It is obvious that the degree of deterioration does not correlate to the amount of mineral oil added but to the amount of metals introduced through the additives present in some of the mineral oil products. Therefore, the mineral fluids were analyzed for their content of metals: zinc, calcium and magnesium.
The observed effects were specific for different bio-oil products and for different mineral oils. The effects took several hours or days to develop. This has several practical consequences:
- The reactions between bio-oils and mineral oils vary in a wide range, depending on the combination of products used. A 2-percent tolerance level for contamination is a very coarse measure.
- Metal-free or zinc-free mineral oil seems not to cause major problems.
- The observed delay effect increases the breakdown risk for users, as qualified maintenance personnel may no longer be available when problems appear several hours or days after the conversion of equipment from mineral oil to bio-oil.
- As a quality check after conversion, the remaining metal content in the mixture would be much easier to analyze in standard lab procedures than the amount of mineral oil.
A specific metal tolerance index likely could be defined for each bio-oil product, also as a performance indicator for product development, eventually replacing the inflexible 2-percent rule in the ISO 15380 standard.
References
1. Internet site of the German Market Introduction Program for Biobased Lubricants: www.bioschmierstoffe.info
2. VDMA (German Machine Manufacturers Association) recommended practices: VDMA 24 568 – "Biologisch schnell abbaubare Druckflüssigkeiten – Technische Mindestanforderungen"; VDMA 24 569 – "Richtlinie für die Umstellung von Druckflüssigkeiten auf Mineralölbasis nach DIN 51 524 auf biologisch schnell abbaubare Druckflüssigkeiten und erforderliche Maßnahmen für den Betrieb" – (Guideline has been replaced by ISO 15380)
3. ISO 15380:2002 – Lubricants, industrial oils and related products (class L) – Family H (Hydraulic systems) – Specifications for categories HETG, HEPG, HEES, and HEPR
4. Theissen, H.: "Die Marktsituation biologisch abbaubarer und biogener Schmierstoffe in Deutschland 2006", Aachen 2006 (available for download at www.bioschmierstoffe.info)
5. Murrenhoff, H.; Rüschkamp, H.: "Untersuchung des Verhaltens von Bioölen mit Restanteilen von Mineralöl in hydraulischen Anlagen", Final Report FNR FKZ 22 014 803, IFAS Aachen 2006 (available for download at www.fnr.de)
6. Geller, A.: "Untersuchung der Mischungsprobleme von Biohydrauliköl mit Mineralöl", Diploma Thesis, Aachen 2006 (internal document)
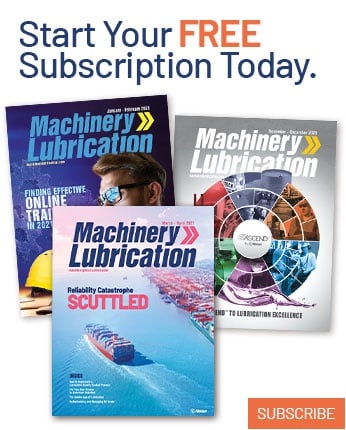