"Many of the available side-stream (portable) filter systems have low flow rates, and I am concerned that it might not be circulating enough oil to get ahead of the contaminant level. What is considered to be a good target flow rate for side-stream filtration?"
There is no single answer for this question. Filter system selection must follow a thorough analysis of the system constraints and a clear definition of the task objectives. There are a handful of questions to ask about the targeted systems before selecting elements and hardware, including the following:
1. What is the relative cleanliness of the fluid in its initial state?
2. What is the new cleanliness target level?
3. How long can the portable filtration system run once it is put into operation?
4. What will the fluid viscosity be during filtration?
5. What is the sump volume?
The selection of filter elements and hardware can be a sliding scale based on the answers that exist to these questions. A couple of key principles to consider are:
1. If the flow is constant, as the operating viscosity increases, the element size should also increase.
2. As the flow increases, element effectiveness may decrease.
What does this mean in practical terms? Higher flow does not necessarily lead to improved filtration effectiveness.
Assume the following conditions: Your facility is going to purchase a unit with a 5-gallons-per-minute throughput and will choose between a 5-inch spin-on, an 8.2-inch coreless element or a 16.9-inch coreless element. All the elements have the same Beta rating (B10=100), and the facility has two 1,000-gallon sumps to filter. The first sump (circulating oil) has an operating viscosity of 180 centistokes (cSt), while the second sump (hydraulic) has an operating viscosity of 55 cSt.
In this situation, any of the element options for the second sump (hydraulic) may work, but the facility would be better off to select the 16.9-inch media for the first sump. The larger filter element will help maintain the 5-gallons-per-minute rate (even positive-displacement pumps don't have 100-percent volumetric efficiency) regardless of fluid temperature, which correlates to the amount of time the technician will have to leave the filter in place to reach the cleanliness target. Additionally, large filters translate to lower element flow density, which typically translates to better filter economy (cost to take out a gram of dirt) and more stable capture efficiency throughout the filter's life.
The point of this exercise is to show that there are many factors that should be considered prior to making this decision. It is not a complicated decision if the objectives and the constraints are clearly defined. Start by evaluating the constraints and setting the cleanliness objectives. From there, it is a simple engineering exercise that can be rooted in known criteria.
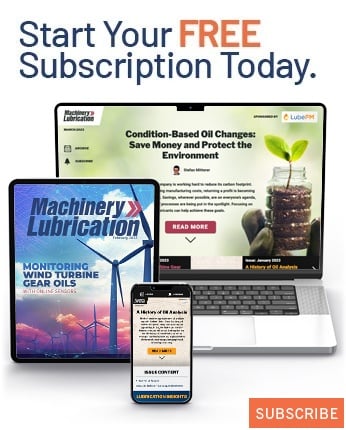