"We are experiencing pump bearing housings that are contaminated with either water, sludge or wear metals. I've been reading about some in-depth flushing procedures on your Web site. Is there a simpler standard procedure that could be used (recognizing that all contaminants will not be removed) to remove some, if not a good portion of the contaminants?"
The chosen path will depend on the nature of the contaminants. If your primary problem is an adherent contaminant (varnish), then forceful action or chemical action is likely required. You may remove some portion through normal oil changes, but this is a long-term proposition. High-velocity flush with a detergent or petroleum solvents may be useful, but as I understand, you are not in a position to go this route. There is always some risk to introducing solvents and detergents into lubricant compartments.
If your contaminant is in the bulk fluid (particulate or chemical contaminant), then a drain and fill, repeated a handful of times with short run periods between, may be sufficient. With some systems I would be comfortable conducting a running drain and literally flushing out the old material with a large quantity of new lubricant metered in while the system is running (also known as bleed and feed). You must pay special attention to oil levels if you choose this route.
It is not difficult to install fluid quick-connect couplings on most existing sumps, even with the machines running. Again, attention to the oil level is important. I would prefer to install fluid quick-connect fittings and use a filter cart well above the other alternatives.
When using a filter cart, the oil is taken from a dirty sump, filtered and returned to the dirty sump. The cleanliness of the filtered oil is diluted, so to speak, by the dirty oil residing in the tank. To overcome the dilution effect, the tank volume must pass through the filter approximately seven times to achieve the equivalent of single-pass filtration (where the oil is pumped from one container to another through a filter).
For example, if you have a 30-gallon tank and a filter cart that pumps at 5 gallons per minute (gpm), you need to run the cart for 42 minutes to equal single-pass filtration (30 gallons multiplied by 7, divided by 5 gpm). If you want to achieve two-pass filtration, you must engage the offline filter for 82 minutes or about an hour and a half.
Even with heavily varnished surfaces, the right type of filtration equipment can resolve the problem.
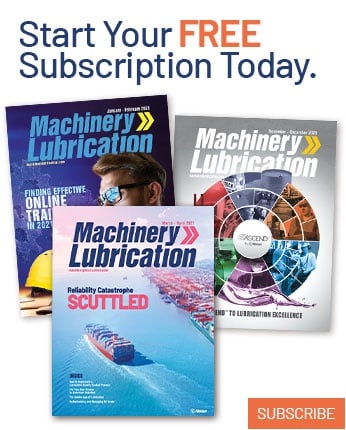