"We recently ran a particle count run on our turbine lube oil. I don't have any reference point for our results, but of our two units, one was much higher than the other. I need to know what reasonable numbers are for particles."
Several areas need to be considered when answering this question. First and foremost is the sampling procedure. If the sample is being pulled from a sump drain or via simple drop-tube sampling, one can expect erratic particle count results because these methods do not result in quality representative conditions of the level of contamination or the level of wear. Best practices include installing a primary sample port in the return line prior to dumping into the sump.
Secondary sample points can be installed inline after each lubricated component (bearings). This will allow for pinpointing a source of a problem noted in the sample drawn from the primary sample point.
Secondly, regarding reference point, the alarm sets assigned to cleanliness levels do not utilize a reference point. The alarms given to cleanliness are target values assigned by the end user based on criteria such as safety, production criticality, cost of downtime, etc. While it is important to test your new lubricant for cleanliness, this value is not used as a baseline reading like those results from viscosity would be.
Original equipment manufacturer (OEM) recommendations for some turbines are as high as 16/13, while others recommend a cleanliness much cleaner, such as 14/11. Significant improvements in reliability and equipment life can be achieved by setting target values lower than those recommended by the OEM. For example, reducing the target cleanliness from 16/13 to 14/11 will allow an extension of 1.5 times the life as a 16/13 target (all conditions remaining optimum).
In order to achieve these target levels, proper contamination control measures should be in place. These include quality desiccant breathers or hybrid breathers, serviceable seals, full exclusion from the environment to include lube top-up and change procedures, and quality Beta-rated filters.
It has been said that, "The cost of excluding a gram of dirt is approximately 10 percent of what it will cost you once it gets into your oil." Paying a premium cost up front to exclude contamination will definitely save you from losing a small fortune due to this contamination.
If you have two like units fitted the same in regards to contamination control and one is showing a higher level of contamination, an inspection as to the source of contamination is warranted. In addition, target values should be in place, and any increase in contamination is cause for corrective action.
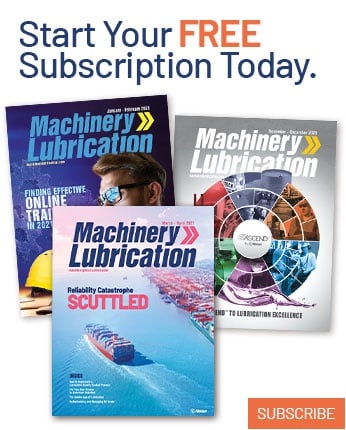