In 1948, Visy Paper was started by the Pratt family in Melbourne, Australia, as a manufacturer of corrugated cardboard boxes. Today, Visy has become one of the world’s leading packaging, paper and recycling companies. It employs more than 5,500 personnel and operates in over 120 sites across Australia, New Zealand, Thailand, Vietnam and Malaysia, with additional trading offices in Singapore and China. Visy also has a sister company, Pratt Industries USA, which employs an additional staff of 3,500 in North America.
Beyond the actual manufacturing of products, Visy operates collection and recycling services across Australia and New Zealand. In the last fiscal year, the company produced more than 680,000 tons of fiber packaging, 623 million steel food cans, 1.4 billion beverage cans, 836 million beverage cartons, 2 billion polyethylene-terephthalate (PET) containers and 646 million units of food plastics. In the same year, Visy recovered more than 1.4 million tons of paper and cardboard, 489,000 tons of glass, 67,000 tons of plastics and 30,000 tons of metals to be recycled.
In 2009, the Visy Paper Gibson Island plant embarked on a journey to improve reliability and reduce engineering downtime. The plant decided to concentrate on lubrication as a major area of improvement. Utilizing a “back to basics” approach, Visy Paper Gibson Island has achieved incredible results in a very short amount of time. For its demonstration of excellence in machinery lubrication, the company has been chosen to receive this year’s John R. Battle Award by the International Council for Machinery Lubrication (ICML).
The prestigious award was presented to Iain Harris of Visy during the recent Mainstream Conference. Harris received the award on behalf of the team at Visy Paper Gibson Island. Lee Taylor, a national reliability manager and former Gibson Island site reliability manager, nominated Visy Paper for the award.
The Visy plant’s “keep it simple” reliability strategy focused mainly on balancing, aligning, lubricating and tightening equipment assets. The plant’s emphasis was to tighten, lubricate and clean (TLC). This TLC given to their equipment has gone a long way, reducing engineering downtime by 64 percent in the first 2 1/2 years, with at least two-thirds of that attributable to lubrication practices.
How to Win the John R. Battle Award
The John R. Battle Award recognizes organizations that have exhibited excellence in the application of machinery lubrication. The award was designed to motivate companies to improve machine reliability and maintenance quality through development, implementation and management of a best-in-class machinery lubrication program.
To become a John R. Battle Award recipient, an organization must demonstrate a solid lubrication program, supported by multi-disciplinary efforts and approaches, with sustainable results and continued improvements. Among other factors, the John R. Battle Award criteria will include the following:
- Commitment to education and skills competencies
- Maintenance culture and management support
- Lubricant selection, lubricant performance standards and lubricant consolidation
- Preventive, predictive and proactive program design and effectiveness
- Lubrication program metrics and overall performance tracking
- Lubricant storage, handling, safety and conservation
- Lubrication PM optimization, work plan management, scheduling and documentation
- Oil analysis program design, test slates, lab selection and setting of alarms
- Oil analysis sampling frequency, sampling hardware and procedures
- Contamination exclusion and removal
- Oil and grease application methods and hardware deployed
- Continuous improvement
ICML awards are open to companies worldwide at no cost to the applicants and are independent of any involvement by the applicant companies in any area of ICML activity. To remain unbiased, it is ICML’s policy that nominations come directly from industry confirmed via plant personnel.
For more information on the John R. Battle Award or to nominate your company, visit www.lubecouncil.org or e-mail info@lubecouncil.org.
Visy’s journey began with its engineering and lubrication technicians attending Noria’s lubrication training, followed by ICML certification. Three other site trades staff also underwent training. These new in-house experts led an effort that included Visy-developed in-house training on lubrication, oil sampling and testing, and fastening techniques. The in-house training modules are now given every 12 months.
Visy currently has a standard for its lubrication personnel with outlined job descriptions, including professional development expectations, to include training and certification minimum requirements. The ICML Machine Lubrication Technician (MLT) Level I certification has become an efficient hiring tool for management at Visy and is a minimum requirement for lubrication personnel.
Visy also undertook a site lubrication audit, with resulting modification of several lubricant-related specifications, rationalization of suppliers and the introduction of monitoring programs, including vibration and oil analysis. Its lubrication program now encompasses a combination of preventive, predictive and proactive activities for different equipment types and criticalities. Time-based oil changes on non-critical equipment and preventive maintenance (PM) lube tasks on scheduled routes are combined with inspection tasks based on vibration and oil analysis results. Precision tasks include a proactive approach of full-time oil decontamination along with oil analysis for health monitoring. Results are trended carefully and utilized in decision making, not just filed away.
In addition, the Visy machines are set up for effective and non-intrusive inspections of relevant lubrication conditions. A thorough criticality study was conducted, analyzing more than 1,500 pieces of lubricated equipment and taking into consideration several factors, such as speed, contamination, position, moisture, temperature, vibration, bearing name, bearing type, bearing bore/outside diameters and bearing width for all grease-lubricated equipment.
By focusing on balancing, aligning,
lubricating and tightening equipment
assets, Visy’s reliability strategy reduced
engineering downtime by 64 percent
in the first 2 1/2 years.
An area of focus in lubrication has been the PM routes and schedules, as well as integration of the computerized maintenance-management system (CMMS). The program puts great emphasis on metrics, with both direct and indirect lubrication program metrics being tracked, including compliance on lube PMs and oil health. Target alarms and discrepancies are tracked, along with completed PM tasks. Examples of indirect metrics for tracking of results include oil usage and downtime, with every minute the machines are down booked to a specific code within the system.
Visy also made a capital investment in the construction of a world-class lube room, employing current best practices. The new room has been designed to house state-of-the-art storage and transfer equipment, and is fitted to provide all necessary filtration of lubricants. The attention to detail includes color-coding of equipment, which even accounts for color blindness as a factor.
Cleanliness levels for the purpose of equipment life extension are a major area of concentration and have generated very positive results. The large lubrication tanks were emptied through a filter, tanks were cleaned, access hatches resealed, holes were sealed, tanks were filter-filled through a 2-micron filtration system and desiccant headspace breathers were fitted.
Visy’s Gear Oil Before Filtration
(100x magnification)
Visy’s Gear Oil After Filtration
(100x magnification)
When the program began three years ago, the Visy team challenged themselves to achieve 100 ppm water and an ISO 13/10 level in the main bearing lubrication tank. This tank supplies oil to more than 350 paper machine bearings. Visy invested in a vacuum dehydrator and a 2-micron offline polishing kidney. Within one month, the company had decreased the water level from an average of 950 ppm to less than 100 ppm. It also reduced the contamination levels over a few months. Visy found that it took about one month to drop one ISO level. This work was a major contributor to reducing engineering downtime.
Closing the existing lubrication practices gaps and tracking the quantifying benefits of doing so have armed Visy’s reliability team with the persuasive tools needed to gain support from management for a greater mission of reliability for the company as a whole. Visy has even added reliability to its mission statement. The company also intends to implement the lubrication excellence program at its eight other sites.
Visy’s example proves how starting with the basics, keeping it simple and investing in world-class maintenance and reliability, particularly lubrication practices and personnel, can translate into immense improvements. These improvements in turn positively affect the reliability, maintainability, availability and profitability of a plant.
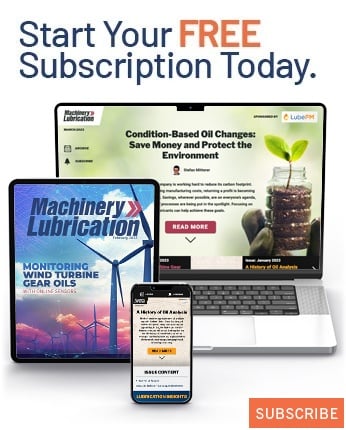