
Approximately 95 percent of the current lubricant market share is comprised of conventional (mineral-based) oils. Most people know these mineral oils are derived from a crude stock, but how much do you really know about the refining process?
The petroleum that flows from a well in the form of crude oil comes in many varieties and types, ranging from light-colored oils containing mostly small hydrocarbon molecular chains to black, nearly solid asphalt-like large hydrocarbon chains.
These crude oils are very complex mixtures containing a plethora of different compounds made of hydrogen and carbon. These compounds (known as hydrocarbons) can range in size from methane (containing one carbon and four hydrogen atoms) to massive structures with 60 or more carbon atoms. This molecular size distribution can be used to our advantage.
The Importance of Refineries
Most lubricating oils come from petroleum or crude oil. In order to get a lubricating oil from a crude oil, the crude oil must be sent through a refinery. The refinery takes from the crude oil a lot of molecules of various sizes and structures that can be used for different things. For example, gasoline, diesel and kerosene are all derived from crude oil.
Lubricating oil relates to hydrocarbon molecules of a particular size (in the range from 26 to 40 carbons). Fairly large and heavy molecules are needed to work as lubricating oils. The molecules that are used with gasoline and kerosene are smaller and have fewer carbons in the structure of the molecule. The refinery puts these molecules in little silos based on size and weight, and removes impurities, enabling each of the products from the crude oil to be utilized.
After the crude oil is desalted and sent through a furnace where it is heated and partially vaporized, it is sent to a fractionating column. This column operates slightly above atmospheric pressure and separates the hydrocarbons based on their boiling points, which are directly affected by their molecular size. In the fractionating column, heat is applied and concentrated at the bottom.
The hydrocarbons entering the column will be vaporized. As they travel upward in the column, they will cool until they condense back into a liquid form. The point at which this condensation occurs varies again based in part on the molecular size.
93% | of lubrication professionals would purchase a lubricant with a high-quality base oil at a higher initial price instead of a lubricant with a low-quality base oil at a lower initial price, according to a recent survey at machinerylubrication.com |
By pulling the condensing liquid from the column at different heights, you can essentially separate the crude oil based on molecular size. The smallest of the hydrocarbons (5 to 10 carbon atoms) will rise to the very top of the column. They will be processed into products like gasoline.
Condensing just before reaching the top, the compounds containing 11 to 13 carbon atoms will be processed into kerosene and jet fuel. Larger still at 14 to 25 carbon atoms in the molecular chain, diesel and gas oils are pulled out.
Those compounds with 26 to 40 carbon atoms are a tribologist’s main concern. This is the material used for the creation of lubricating oil. At the bottom of the column, the heaviest and largest of the hydrocarbons (40-plus carbon atoms) are taken and used in asphaltic-based products.
After the distillation process, the compounds need to be refined for their intended purpose. This step in the process is done to reduce the tendency of the base oil to age (oxidize) in service and also to improve the viscosity/temperature characteristics. There are two ways this can be done.
The first involves a separation process where there are two products being made: a desired lube product and undesirable byproducts. The second way, which is quickly becoming the favored of the two, is a conversion process. This process involves converting undesirable molecular structures into desirable structures with the use of hydrogen, heat and pressure.
Extraction Process
The following is a simplified description of the extraction process:
Deasphalting
Propane deasphalting takes the residuum from the very bottom of the column (the heaviest, largest molecules) and separates them into two products: tar and compounds that are similar to the lube distillates but have a higher boiling point. This material is called deasphalted oil, and it will be refined in the same manner as the lube distillates.
Solvent Extraction
Solvent extraction is the term used for the removal of most of the aromatics and undesirable constituents of oil distillates by liquid extraction. Commonly used solvents contain phenol, furfural and sulphur dioxide. The resulting base stocks are raffinates (referred to as neutral oils) and an extract that is rich in aromatic content, which is highly sought after as a process oil or fuel oil.
Dewaxing
After solvent extraction, the raffinates are dewaxed to improve low-temperature fluidity. This process again produces two products: a byproduct wax that is almost completely paraffinic and a dewaxed oil that contains paraffins, naphthenes and some aromatics. This dewaxed oil becomes the base stock for many lubricants, but there is one more process that can be done to make a premium product.
Hydrofinishing
Hydrofinishing changes the polar compounds in the oil by a chemical reaction involving hydrogen. After this process, an observer would notice a lighter-colored product and an improved chemical stability. The final quality of the base oil is determined by the severity of the application of temperature and pressure in the hydrofining process.
Conversion Process
The following is a simplified description of the conversion process:
Hydrocracking
In this refining process, the distillates are subjected to a chemical reaction with hydrogen in the presence of a catalyst at high temperatures and pressures (420 degrees C and 3,000 psi). The aromatic and naphthene rings are broken, opened and joined using hydrogen to form an isoparaffin structure. The reaction with hydrogen will also aid in the removal of water, ammonia and hydrogen sulfide.
Hydrodewaxing
During hydrodewaxing, much like hydrocracking, a hydrogenation unit is used to deploy a catalyst that is specific to conveying waxy normal paraffins to more desirable isoparaffin structures.
Common Mineral Oil Molecules
Hydrotreating
Because the previous two processes involve breaking chemical bonds between two carbon atoms, it is necessary to introduce the saturation of any unsaturated molecules. This is easily done by introducing more hydrogen. These saturated molecules are more stable and will be able to resist the oxidation process better than the unsaturated variety.
There are slight differences in the characteristics of the finished base oil produced by these two processes. The main difference lies in the aromatic content. The conversion process can reduce the aromatic content to around 0.5 percent, while the extraction process lingers around 15 to 20 percent. This aromatic content has the following effects:
It would appear that the conversion process produces a better quality product, but there is always a trade-off. The cost of refining oil using the conversion process is somewhat higher than the extraction process. This extra cost incurred by the refiner is eventually passed on to the customer. However, in this case, the customer typically gets what he pays for - a higher quality base oil at a higher initial price.
Mineral Base Oils
The base oil is the foundation of a finished lubricant. A finished lubricant is one that is ready for use and is a blend of both base oil(s) and additives. Remember, the additives formulated into the mineral base oil will alter the properties of the base oil.
The basic function of a refinery is to separate the crude oil into its useful components and remove the components of unwanted materials. Base oils or base stocks, as they are sometimes called, are created from separating and cleaning up crude oil. They are one of several liquid components that are created from crude oil.
Gasoline is the lightest or smallest hydrocarbon component, followed by kerosene or jet fuel, diesel fuel, base oils, waxes and asphalt or bitumen, which is the heaviest, thickest material. Base oils are prepared from crude oils through the use of the following series of processes which, to some degree, must be applied to all crude oils for refining and also re-refining processes.
Refining Process
Base oils are typically created in four different viscosity grades within the refinery distillation process. This allows for the creation of the various ISO and API viscosity grades.
These processes are:
1. Atmospheric Distillation is used initially to separate fuel, such as gasoline and diesel, from the remainder of the crude petroleum. Distillation is a separation process. The products of a distillation are referred to as distillates.
2. Vacuum Distillation is performed to distill and therefore separate some heavier fractions that would not distill at atmospheric pressure without damaging them. It is used to obtain the initial base oil viscosity and flash point characteristics. This process provides the four various viscosity fractions (or distillates) from which the finished oil products are made.
3. Refining is performed to remove unwanted chemical structures (rings, etc.) from the base oil to reduce the tendency of the base oil to age in service and also to improve the viscosity/temperature characteristics.
Three basic refining processes are used by oil companies:
(a) Sulphuric acid/clay refining (old, outdated technology)
(b) Solvent extraction (common in refineries built in the middle of the 20th century)
(c) Catalytic hydrogenation or hydrotreating (introduced in the 1980s)
4. De-asphalting is a step in the process that removes the heavy asphalt residue from the useful distillate fractions.
5. De-waxing is a step that is performed to reduce the wax content of the base oil in order to improve the low-temperature properties of the oil.
6. Blending is the final process in producing a finished lubricating oil. It involves the blending of different base oils to obtain the necessary viscosity, as well as the addition of specified additives to ensure that the finished oil has the right properties to provide the intended lubricating ability.
In order to more fully understand why base oils exhibit different qualities, it is necessary to briefly describe the various refining processes listed in No. 3 (above).
1. Acid/Clay Refining is the treatment of crude oil distillates (fractions) with sulphuric acid or their chemicals. The process initially improves the color and aging tendencies, and also increases the density and viscosity index of the oil. The use of acid/clay refining processes is limited to the manufacture of some white oils and sulphonates as well as to some regeneration of waste oils.
This process has, to a large degree, been replaced by more modern refining methods because it produces large quantities of acid sludge, which is very difficult to dispose of without a negative impact on the environment.
2. Solvent Extraction is the term for the removal of most of the ring structures and aromatics (weak, undesirable components) of oil distillates by liquid extraction. Common and suitable solvents are phenol, furfural and sulphur dioxide. Furfural is used extensively as the extractant for the refining of paraffinic oils. This results in base stocks that are neutral oils and an extract fluid that is rich in aromatic content, which is used for process oils and fuel oils.
After solvent extraction, the resulting materials are de-waxed to improve low-temperature fluidity and then sometimes hydrofinished with hydrogen gas to further improve the color and stability.
The final quality of the base oil is determined by the severity of the application of temperatures and pressures in the hydrofinishing process. The base oils are now ready to be selectively blended with the appropriate additives to achieve the desired physical, chemical and performance properties of the finished oil.
3. Catalytic Hydrogenation (hydrotreating) is the refining process that subjects the crude distillates to a chemical reaction with hydrogen in the presence of a catalyst at temperatures as high as 420 degrees C (800 degrees F) and pressures up to 3,000 psi. Hydrotreating processes are the favored methods used by many base oil refiners and lubricant manufacturers because of the superior quality of the base oils and the small amount of waste hydrocarbons created.
Hydrocarbon structures that previously were downgraded to waste streams in the refinery are now converted to valuable base oils. When hydrotreating is performed, more than 90 percent of the aromatic content is converted to more valuable hydrocarbons.
Three types of hydrotreating can be distinguished:
“Hydrofinishing” is a mild process that removes the remaining traces of undesirable compounds.
“Hydrotreating” is a refining hydrogenation carried out to improve color, odor, oxidation stability and demulsifying properties of distillates.
“High-pressure hydrogenation” or “hydrocracking” offers complete removal of unwanted compounds and nearly complete conversion of the aromatics and naphthenic rings into desirable branched paraffins.
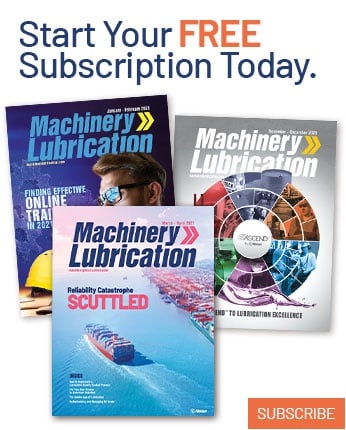