Use caution with grease lines that run out of the machine frame and are intended to offer easy lubrication access points. Since these line extensions often carry more than a few shots of grease, the grease entering the bearing will not be robust and fresh. Vibration, time and temperature changes can lead to leaching of critical oil components from the grease thickener, leaving a dry soap in the tube.
Also, without visual access to the bearing area, there can be numerous undetected problems. The best approach is to provide access to the lube point as close to the bearing as possible. This enables the bearing to be inspected and ensures that fresh grease enters the lube cavity.
Check Gear Reducers for Condensation
If you have a reducer that is water-cooled and the water temperature is too cold, it could condense and put water in the oil. If you notice the gear reducer sweating, water on the floor or water on the cooling water lines going into the gear reducer, you probably have water in the gear reducer. When you find this problem, first increase the temperature until the water lines quit sweating. Second, perform oil analysis on the reducer and check for water. If this issue isn’t corrected, it could be catastrophic.
Infrared Scans Can Detect Reservoir Problems
Consider performing infrared scans on your rotating equipment to monitor the operating temperature of your reservoirs. A routine scan of a large gearbox revealed that it was overheating (operating above 190 degrees F) due to failure of the oil cooler pump. The oil was foaming significantly out of the oil sight glass.
Sediment in Sight Gauges
A fan pump recently lost an oil-filled bearing due to lack of oil in the sump. The oil level sight gauge used on this pump indicated that the pump was full, but actually it was not. The pipe coming out of the side of the pump to the level gauge was plugged with sediment and would not let oil out of the sight gauge to give a true oil level reading. To prevent this, lube technicians need to drain sight gauges periodically to confirm proper functioning.
How Long Should Oil Be Filtered?
When filtering oil, it is a good rule of thumb to run your filtration unit until the total flow through the filters equals the volume of seven times the reservoir capacity. Because of differences in oil viscosities and the bypass valve used to keep the filter pressure in the acceptable range, you may not be able to use rated pump-flow rates to determine how long it will take to reach this goal. However, you can add flow meters on your filtration skid so you will know how much oil has actually gone through the filters. This way you can be sure that you are getting your minimum level of acceptable filtration.
Advice for Labeling Oil Sample Bottles
When labeling oil sample bottles, consider labeling the bottle cap also. If you mistakenly place a cap from a bad sample onto a bottle containing a good sample, the sample is cross-contaminated. Testing of this cross-contaminated sample will yield false data. Labeling both the bottle and its cap will prevent this problem from occurring.
The “Lube Tips” section of Machinery Lubrication magazine features innovative ideas submitted by our readers. Additional tips can be found in our Lube-Tips e-mail newsletter. If you have a tip to share, e-mail it to us at editor@noria.com. To sign up for the Lube-Tips newsletter, visit www.machinerylubrication.com and click on the “Newsletters” link at the top.
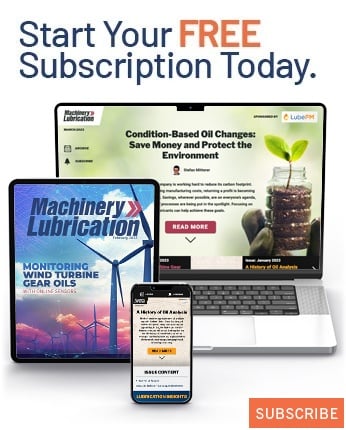