How much of an effect do contaminants have on the life of a bearing?
When bearings operate in a clean environment, the primary cause of damage is the eventual fatigue of the surfaces where rolling contact occurs. However, when particle contamination enters the bearing system, it is likely to cause damage such as bruising, which can shorten bearing life dramatically.
Furthermore, when dirt from the environment or metallic wear debris from some component in the application is allowed to contaminate the lubricant, wear can become the predominant cause of bearing damage. If bearing wear becomes significant due to particle contamination of the lubricant, changes will occur to critical bearing dimensions that could adversely affect machine operation.
In general, the important parameters influencing bearing wear are contaminant particle size, concentration, hardness and lubricant film thickness. Increases in all of these parameters except film thickness will increase bearing wear.
Keep in mind that increasing the lubricant’s viscosity will reduce bearing wear for a given contamination level.
Bearings operating in a contaminated lubricant exhibit a higher initial rate of wear than those not running in a contaminated lubricant. However, with no further contaminant ingress, this wear rate quickly diminishes as the contamination particles are reduced in size as they pass through the bearing contact area during normal operation.
Either dissolved or suspended water in lubricating oils can exert a detrimental influence on bearing fatigue life. Water can cause bearing etching, which can also reduce bearing fatigue life. The exact mechanism by which wear lowers fatigue life is not fully understood, but it has been suggested that water enters micro cracks in the bearing races which are caused by repeated elastic deformation stress cycles. This then leads to corrosion and hydrogen embrittlement in the micro cracks, which reduce the time required for these cracks to propagate to an unacceptable size spall.
Water base fluids such as water glycol and invert emulsions have also shown a reduction in bearing fatigue life. Although water from these sources is not the same as contamination, the results support the previous discussion concerning water-contaminated lubricants.
Another theory suggests that while mineral oils exhibit an exponential rise in viscosity with increasing pressure, water exhibits very little viscosity increase with a rise in pressure. Accordingly, water-based fluids will not generate an elastohydrodynamic film thickness equivalent to a petroleum oil of the same viscosity.
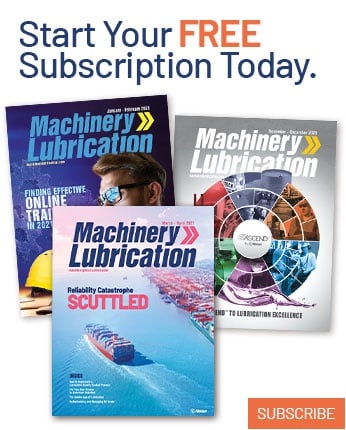