Are we there yet? With summer break now upon us, this question likely will be asked countless times on family vacation trips across the nation. Planning for these trips typically includes asking questions such as where do we want to go, what is our budget, what are the things we need to get there and what can be eliminated. Obviously, the goals must be realistic. Tough decisions and sacrifices will be required from all involved, but the end result will be well worth the effort.
During my travels to various industries, I’ve found that some workers lack a clear plan as to where they are going. They may know that they are there to perform “work,” but beyond that there is little communication/direction between the departments as to where and when they will get there. Imagine putting your family in the car and just saying, “OK, let’s go.” While some might suggest to “just do it,” this motto doesn’t seem to translate well in our professional careers.
Can you answer the “are we there yet” question? If not, perhaps you need to ask yourself if you even know where you are going. It may be time to re-evaluate the direction of your lubrication program.
If you have had the opportunity to attend any of Noria’s Fundamentals of Machinery Lubrication courses, then you should be very familiar with the goal of lubrication excellence. Hopefully, you have gained an understanding of why it is important to keep lubricants clean, cool and dry, as well as the effects of contamination on equipment health. My experience is that most people’s intentions are good when they start. If they would put the same amount of time and effort into striving for lubrication excellence as they do in their family’s summer vacation, they would be successful.
Do you know where you are going with your lubrication program? Are you tracking results and addressing opportunities to improve? Do you have attainable, realistic goals? Do you have the right people with the right attitudes in the right positions to improve the opportunities for success? Once again, tough decisions and sacrifices will be required from all involved, but the end result will be well worth the effort.
67% | of lubrication professionals say their plant has not yet achieved lubrication excellence, based on survey results from machinerylubrication.com |
Lubrication excellence can be achieved. However, many factors can distract you from the goal. You may have started a lubrication program but now have come to the realization that you need to re-evaluate or change the direction of the program. This can become confusing and frustrating, especially when results are not achieved as expected.
There are a few steps you can take to increase your chances for a successful lubrication program or to get back on track. Many times, however, we tend to put the “cart before the horse.” Setting a realistic goal of where you want to be is the best method to increase the chances for success. If you don’t know where you are going, how do you know when you get there? Most kids can only sit in a car for so long before they become agitated. Likewise, most reliability and lube technicians can become frustrated with just going through the motions, especially with so many having become educated and understanding the importance of lubrication.
5 Tips for Setting Target Cleanliness Levels
- Set targets for all lubricating oils and hydraulic fluids.
- Use vendor specifications as ceiling levels only.
- Set life-extension (benefit-driven) targets (e.g., significantly cleaner than before).
- Consider machine design, application and operating influences.
- Make it a personal decision, because you are the one paying the cost of failure, not the machine supplier, oil supplier, filter supplier, bearing supplier or oil analysis lab.
Let’s start by setting a realistic goal for contamination control and establishing cleanliness targets. These levels should reflect reliability goals. This can be achieved by considering the reliability penalty factor and the contaminant severity factor. This will help to set a contaminant goal that is based on your specific facility’s goal.
You also need to take specific actions to reach the goal. This means selecting the proper filter and capture efficiency to achieve the target. Be sure to measure the contaminant levels frequently. Remember, what gets measured gets done. Make appropriate changes as necessary. Setting this goal will help your department answer the “are we there yet” question.
.
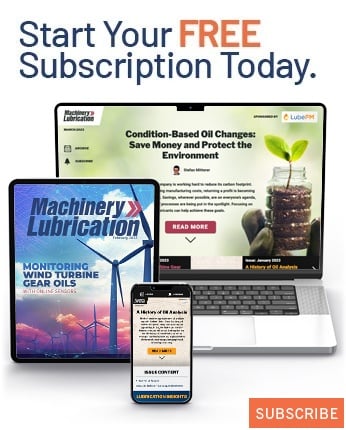