"How can we convince the maintenance manager at our paper mill that oil analysis is beneficial?"
The reason to use oil analysis or for that matter any predictive technology is twofold: to avoid catastrophic failures and to extend equipment life.
A good oil analysis program can save big dollars for a really small investment. You can learn to predict those conditions that are the precursor of failure through spectrographic analysis and trending as well as wear debris analysis. Fluid cleanliness can be tested and compartment targets maintained. Clean fluids make machines last longer.
A solid analysis program results in making condition-based decisions both on the state of the equipment and the lubricant. The oil might be in good condition (minimal contamination, degradation, etc.), but an alignment/load problem may occur that may manifest as higher wear rates as determined by oil analysis. Maintenance supervisors can then look into possible causes (check vibration data) and correct problems before they develop into failure modes.
Even if no premature failures have occurred, it is a risky proposition to operate in such a hostile environment without predictive maintenance tools such as oil analysis. Studies show that 6 to 7 percent of the gross national product (more than $795 billion) is required just to repair the damage caused by mechanical wear.
The single largest cause of mechanical wear is adhesion, most commonly caused by abrasive, tiny particles. Airborne particles are an unfortunate fact of life in a paper mill, and even if measures are taken to reduce the amount of particles in systems, it is difficult (if not impossible) to determine whether particle levels are acceptable without periodic oil analysis including particle counts.
Water is another ubiquitous factor in the manufacture of paper, and some of this water will inevitably find its way into lubricating systems. Water is an oxidation catalyst and can increase sludge and corrosion. In small concentrations, water contamination may not be visually apparent, creating another case for regular oil analysis.
Paper machine oils are also exposed to high bearing temperatures, which is another root cause of oxidation. Total acid numbers should be monitored via oil analysis to ensure that oxidation levels are acceptable. Otherwise, deposits will develop, which can have a detrimental effect on reliability and may eventually lead to premature failure.
Routine oil analysis will shed light on metallic wear trends and assist in scheduling overhauls and downtime, as opposed to employing reactive maintenance practices only when serious problems occur. Oil analysis can also provide confirmation that the correct products are being applied.
In short, routine oil analysis should be a mandatory component of an effective maintenance reliability program, especially at a paper mill.
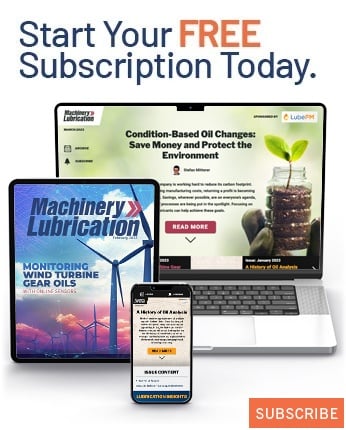