"Our large manufacturing plant has a history of never greasing electric motor bearings because management believes this practice does more harm than good. The plant has a mix of motors, some of which have been in service for 10 years, with others just a few months. Depending on motor manufacturer, speed and horsepower, there is everything from sealed and shielded bearings to open bearings. How should we go about developing a regreasing strategy for these motors?"
First, you will want to establish a way of tracking each motor as an asset. Develop a preventive maintenance (PM) program in your computerized maintenance management system (CMMS) to track these motors.
Next, it is time to play detective and find as much information on each motor as possible, including the date of installation, horsepower (hp), revolutions per minute, bearing type, type of duty, volts, frame size, warranty, etc., as well as the last vendor to repair the motor and the type of grease and bearing used. Start with your most critical motors and new replacements.
Now separate the sealed, shielded bearings into one group and the open bearings into another group. Perform vibration analysis on the sealed and shielded motor bearings. Trend the vibration until replacement. On motors of 15 hp or less, stay with the sealed bearings.
You may wish to replace the motors and not repair them. Use your own formula for replacement vs. rebuild. On larger motors when vibration shows bearing near failure, consider rebuilding the motor with open bearings and bring them into the grease program.
It is best to develop your PM frequency based on runtime (for example, 6,500 hours). Some organizations prefer to relubricate the bearings with the motor running at operating temperature whenever possible.
For open motor bearings:
1. Clean the top grease fitting and remove the bottom grease-relief valve.
2. With a manual grease gun, pump and listen to the bearing using an acoustic grease gun adaptor, following the manufacturer’s directions.
3. Watch for grease coming out of the bottom port. If you pump excessive grease into the motor and none comes out of the bottom port, stop and check for hardened grease in the bottom passage.
4. Allow the motor to run for 1 hour to expel any excess grease before installing the bottom grease-relief valves.
5. Clean any excess grease from the exterior of the motor.
6. You must determine if the original grease is compatible with the new grease. On new motors, you will need to contact the manufacturer.
When sending out a motor for repair, evaluate the bearings and assess how well your program is working. Start with your more critical motors or your most frequent failures. Also, perform vibration analysis on critical motors. This all depends on whether you can run to failure and how much downtime your plant can endure.
For bearings 2 years or older that have supply tubes where the grease fitting attaches to a pipe or tube, that tube needs to be removed and swabbed out. Grease could have become caked in these supply tubes over time. Be sure to fill the supply tube with grease after cleaning.
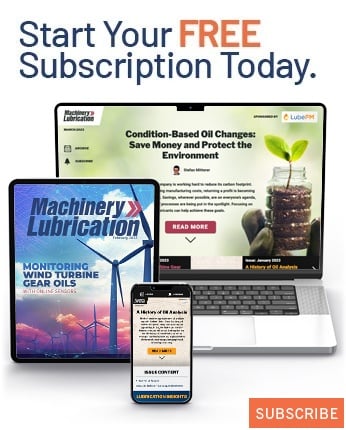