Corrosion costs companies billions of dollars each year. Much of this loss is due to the corrosion of iron and steel. When exposed to moisture and oxygen, iron and steel will react, forming an oxide. This oxide does not firmly adhere to the surface of the metal and will flake off, causing pitting. Extensive pitting eventually results in weakness and disintegration of the metal, leading to failure. This article covers the importance of rust and corrosion prevention methods for machine health and reliability.
How Rust Forms
Obviously, because of the involvement with water, rust occurs much more rapidly in moist conditions. However, there are a few other factors that determine the rate of corrosion. One example is the presence of salt. Dissolved salt increases the conductivity of the aqueous solution formed at the surface of the metal and enhances the rate of electrochemical erosion. Another example is heat. The higher the temperature is, the higher the corrosion rate will be.
Rust Formation
The formation of rust is a very complex process that begins with the oxidation of iron to ferrous (iron “+2”) ions.
Fe → Fe+2 + 2 e-
For the next sequence of reactions, both water and oxygen are required. The iron (+2) ions are further oxidized to form ferric (iron “+3”) ions.
Fe+2 → Fe+3 + 1 e-
The electrons provided from both oxidation steps are used to reduce oxygen.
O2 (g) + 2 H2O + 4e- → 4 OH-
The ferric ions then combine with oxygen to form ferric oxide, which is then hydrated with varying amounts of water.
In layman’s terms: Iron + Oxygen + Water = Hydrated Iron Oxide (Rust)
Other types of corrosion can occur in machine components, namely corrosion from organic acids. These organic acids can form in multiple ways and can even be a byproduct of the oil aging (oxidation). They are weak compared to common inorganic acids but still hydrolyze well enough to damage most metals.
One example is acetic acid. It is mildly corrosive to metals, including iron, magnesium and zinc, forming hydrogen gas and salts called acetates:
Fe + 2 CH3COOH → (CH3COO)2 Fe + H2
In layman’s terms: Iron + Organic Acid = Iron Acetate + Hydrogen
Rust and Corrosion Inhibitor Products
Rust and corrosion inhibitors are essential for protecting metal surfaces in industrial environments, where exposure to moisture, salt, and other corrosive elements can lead to significant damage. One popular option is TKX All-Purpose Lubricant from ITW Pro Brands, which provides excellent rust protection while also acting as a penetrating oil and lubricant. It's versatile, making it suitable for a wide range of applications, including bearings, gears, chains, and pumps.
LPS 3 Premier Rust Inhibitor
Other options include products like LPS 3 Premier Rust Inhibitor which offers long-lasting protection. Its thick, durable coating shields metal surfaces from extreme conditions and is a great fit for cables, chains, and pulleys.
Each of these solutions provides reliable protection, ensuring that equipment remains in good working order and reducing the need for costly repairs or replacements.
Rust and Corrosion Inhibitor Additives
The best way to stop rust and corrosion is not to allow the metal to come in contact with water, oxygen or acid. In essence, this is exactly what rust and corrosion inhibitors in oil do. These additives are typically compounds that have a high polar attraction toward metal surfaces.
They chemically bond to the metal surface, forming a protective film over the underlying metal. This film acts as a barrier that does not physically allow the metal to come in contact with anything that could promote corrosion. Some popular compounds being used are amine succinates and alkaline earth sulfanates.
If rust formation cannot be prevented, the rust particles can flake off and contribute to abrasive wear. The iron oxide is much harder than the steel surfaces it comes in contact with, so massive amounts of three-body abrasion occur.
Three-body Abrasion
The rust-protective properties of an oil can be hard to evaluate and are somewhat subjective. For best results, the lab must polish or sandblast a test specimen and then immediately coat it with the oil to be tested. After coating, the lab can then begin subjecting the specimen to conditions that accompany rust formation. ASTM D665, although denoted as “Rust Preventative Characteristics of Steam Turbine Oil,” can be used for any formulation of oil. In this test, a steel specimen is immersed in a mixture of distilled or synthetic sea water. Over a 24-hour period, the mixture is agitated and checked for the formation of the onset of rust.
Bottom Line
Effectively inhibiting rust and corrosion is critical to maintaining the longevity and reliability of machinery. By understanding the mechanisms behind rust formation and employing a strategic approach that includes the use of high-quality inhibitors, regular maintenance practices, and environmental controls, you can significantly extend the life of your equipment. Selecting the right inhibitor for your specific application—whether it’s for short-term storage, long-term protection, or high-humidity environments—is essential. By doing so, you not only prevent costly repairs and downtime but also ensure optimal performance and safety in your operations.
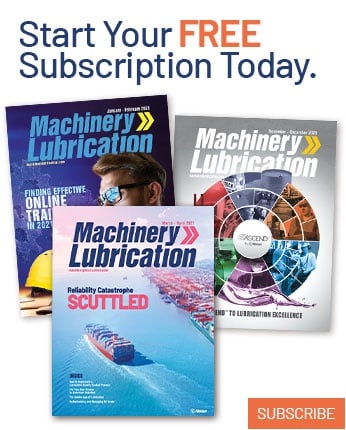