"Our plant has more than 4,000 pieces of rotating equipment. How can we determine which components require routine oil analysis, and how do we select the proper series of tests for these systems?"
First, find out what is currently happening onsite regarding condition monitoring, failure modes and rates, preventive maintenance procedures, machine criticality information, computerized maintenance management system (CMMS) usage, plant/machine availability and reliability information, annual plant output, and costs and revenues.
To gather this information, check the CMMS reports, speak to operations and maintenance personnel, examine control charts, and analyze purchasing, sales and customer information. Also, determine what the business drivers are regarding plant operations. Is it cost reduction, increased quality output, transforming to a lean environment, etc.?
Next, perform a quick criticality assessment. This can always be repeated later in more detail. Learn which machines are causing problems, which machines are critical to operations and which machines could cause a serious health and safety problem if they were to fail.
After establishing the high-priority machines, check duty cycles, operating/environmental conditions, lube specifications and maintenance procedures, as well as actual and possible failure modes. This will help you to decide on the sample tests and frequency.
Work with the laboratory at this point so the diagnosticians can help interpret the data results and set up tests and frequencies. This may also reveal the opportunity to do in-house tests along with lab tests. Most labs have standard test suites by machine type, but check to ensure these tests cover the failure modes.
For instance, hydraulic systems should have particle counts, high-temperature operations may require a rotating pressure vessel oxidation test (RPVOT), and high-moisture environments might need a crackle test. The lube oil supplier should also be able to help determine test suites and frequencies. If oil analysis is not currently performed, a review of labs and a lab contracting phase may be necessary. Make sure the lab is competent to do what is required and that the diagnosticians have experience.
You will also need to train maintenance and operations personnel on why oil analysis is important to machine operations and how this will affect maintenance activities. Educate them on how to take a sample, what the reports will tell them and what diagnostics will be generated.
If oil analysis is new to the site, appoint specialists to get the program running. This adds competency and status as well as process implementation. These specialists will also be good contacts for the diagnosticians.
Finally, ensure oil analysis procedures are added to the CMMS system and that maintenance planners know what these new tasks are. It might be possible to establish oil analysis routes for your specialists. Alternatively, operators could take samples.
The planner should receive copies of the reports and know what to do if a diagnosis suggests a maintenance action. Make certain that all feedback goes into the CMMS. Once a maintenance action is finished, the diagnostician should be informed.
When the high-priority machines have been completed, determine oil analysis activities for the lower priority machines. This may also be the time to do a more rigorous criticality assessment now that high-priority machines are covered under oil analysis procedures.
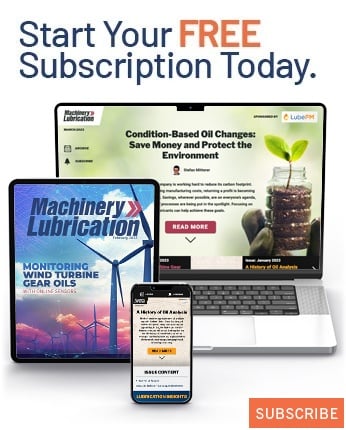