
"After a number of return-line bearing samples were taken from our steam turbine, we were puzzled and concerned by some of the oil analysis results.
Our main concern was the large number of samples that showed elevated particle counts. It’s been recommended that maintenance personnel check the seals, breathers, etc. However, this leads us straight to the silicon count, which is, for the most part, zero. Therefore, the increase cannot be attributed to the ingress of normal dust or dirt. Neither does there seem to be any increase in any telltale wear metals or contaminants in the elemental analysis.
While we are aware that particles large enough to contribute to the particle count may not directly affect the elemental analysis, it seems that an increase in particulate contamination with no supporting evidence from the elemental analysis may be spurious. What else could the particles be? Water levels in the samples are low, ranging from 30 to 40 parts per million (no interference on laser counts). What steps can be taken to determine the root cause of the elevated particle counts?"
Start with the most obvious (or easiest) possible solutions. Direct attention to the sample containers and confirm that they are ultra-clean jars with the seal covers still in place. Next, verify that the samples are being drawn in a proper manner. For example, if a plug is being removed, ensure the area is wiped before removal.
Lines returning to the reservoir will gather contamination to varying degrees, and particle counts cannot be reliably “trended.” However, the question in this case is relative to composition of the particulate, not its varying presence.
You need to find out if the particulate is being generated during each given lube cycle. This could be determined by taking a sample at the current sample point and another following the filter. If the filters are adequately reducing the particle levels, you would know the elevated levels are being generated with each pass through the system.
Using these same samples, direct the laboratory to visually identify any non-metallic contaminants present in both samples. There are two options: ferrography and millipore filtration with microscopic examination. Since no elevated ferrous wear metals were present, ferrography may be limited in what will be captured on the slide. Therefore, a membrane extraction for particulate removal and microscopic identification may be the best choice.
The examination should focus on identifying the size and composition of contaminants, which could include filter media materials, carbon (seals), hose or gasket materials, varnish formations, lint or cloth fibers (shop towel), etc. There could also be gels formed from an incompatible fluid mixture such as a glycol-based fluid. These gel formations would be detected as solid particles in a laser detector.
Should this not provide the necessary evidence, submit a filter element for removal and perform a visual examination of what is present within the media. These steps should reveal the answers for corrective and preventative actions.
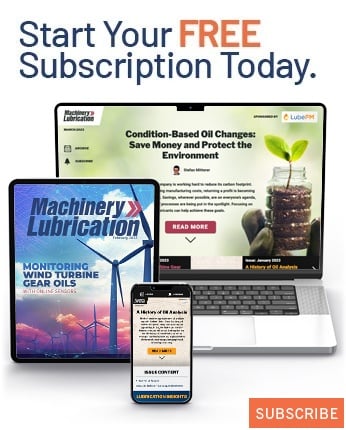