"We've noticed that aeration is occurring in one of our hydraulic systems. What causes this to happen?"
Aeration can be a serious problem if not dealt with quickly and properly. It can lead to cavitation of the pump, spongy or slow hydraulic response, as well as the loss of control of the hydraulic system. There are four states of air in oil: dissolved, entrained, free and foam.
Aeration can be caused by a variety of reasons. The sump design could be creating your problems. Look at how the hydraulic fluid is returning to the reservoir. If the return line is dumping straight in from the top, add a diffuser to reduce the amount of turbulence.
Imagine a glass of beer. When pouring the beer, you tilt the glass to the side to reduce the foam from forming. The same is true in your hydraulic system. If the oil falls straight in and splashes around, this allows air bubbles to form (entrained air). If the bubbles don't have enough time to settle, it can result in foam. By controlling entrained air (suspended air bubbles), you can reduce foam and oxidation.
Air leaks in a hydraulic system can also lead to aeration problems. Check the suction side of the system for leaks. Pump seals, pipe fittings and unions are all possible areas for air leaks that allow the system to pull in air and pressurize it. You can find these leaks using an ultrasonic gun or by simply placing a small drop of oil or grease around the suspected leak site. If there is a leak, a hole will be drilled through the grease, showing you the area of air ingression.
Poor detrainment, which is the amount of time it takes for the air bubbles to rise to the surface and pop, can be caused by oxidation and contamination or anything that results in low surface tension within the fluid. A lower surface tension allows the bubbles to break apart below the surface. The larger the bubble, the quicker it rises to the surface. When bubbles begin to break apart below the surface, the amount of time it takes them to rise increases. This keeps them in suspension longer, increasing the risk of cavitation and also leading to problems with foam.
By controlling the amount of air your oil is in contact with and how turbulent the environment in the sump is, you can increase the life of your machine and your oil.
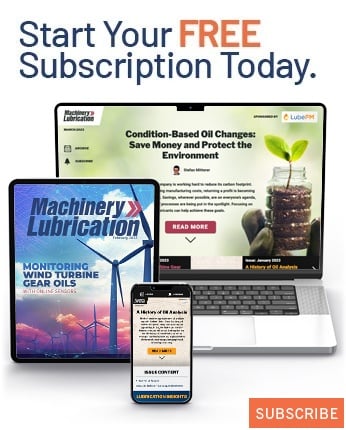