"Should critical equipment be checked more often than non-critical equipment?"
Critical equipment most definitely should be checked more frequently than non-critical equipment. Based on the definition of "critical," you are referring to the machines with the highest importance to you, your company and your process. These assets deserve the focus of your limited time, money and energy.
Of course, it is important to know how you define an asset as critical. There are many approaches to determine the criticality of an asset. Some plants choose to use a simple 1 to 5 grading scale and subjectively assign numbers, while others utilize large, drawn-out processes and even employ a coaching consultant to help make the determination. However, the decision can be narrowed down to a few key attributes:
- Impact on production
- Impact on safety
- Impact on the environment
- Replacement cost
- Spares or redundancy availability
- Probability of failure
- Historical data on reliability and preventive maintenance
Most plants are very limited with regards to manpower and money. If there are only so much of these resources in your "bank," you want to be sure to spend them wisely. In order to make an informed decision on how to spend, you must have a good grasp on the assets’ criticality relative to one another.
These criticalities can also be used to help set work prioritization. With limited resources, you always want to be working on the highest priority jobs first. This ranking of jobs is all but impossible if you don't have an understanding of machine criticality.
A good example of using criticality to drive scheduling decisions is oil sampling. Any asset that has a high impact on production, safety and the environment, costs more to replace, has little to no spare parts or redundancy, coupled with a high failure probability, and poor reliability and preventive maintenance would be an excellent candidate for real-time, continuous online monitoring.
As the asset's attributes become less and less severe, the sampling frequency relaxes, changing from continuous monitoring to maybe hourly, daily, monthly, quarterly or annually. You may even reach a point where you decide that oil analysis just doesn’t offer any benefit because the machine has little to no impact on production, safety or the environment. It might be cheap to replace, or you may have easy access to spares.
Criticality is very much a part of making informed decisions on scheduling, whether it be a simple sight-glass inspection or as complex as a turbine rebuild.
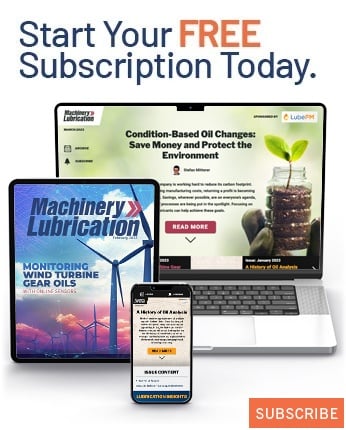