It has been estimated that more than 100 million gallons of lubricants could be saved every year if external leakage from pumping systems, hydraulic machines, gear cases and sumps was eliminated. Approximately 70 to 80 percent of hydraulic oil leaves the system due to leakage, spills, line and hose breakage and fitting failures. Studies have indicated that every year the average plant uses four times more oil than its machines actually hold, and this is not accounted for by frequent oil changes.
Leakage occurs from seals and packings; pipe joints and gaskets; and damaged, ruptured and corroded lines and vessels. The biggest causes of external leakage are the wrong selection, improper application, poor installation and inadequate maintenance practices that are applied to sealing systems. Other causes include overfilling, pressurization from plugged vents, worn seals and over-torqued gaskets. The major reasons for initial seal failure and fluid leakage are cost-cutting by machine design engineers, incomplete commissioning and plant start-up procedures, and inadequate equipment condition monitoring and maintenance practices.
Once a seal has failed and fluid leakage results, the problem is perpetuated by purchasing low-quality or incorrect seals, or by careless installation practices used during replacement procedures. The subsequent leaks, while possibly not considered excessive, can go on and on. Soon plant operating and maintenance personnel accept the leakage as normal.
Leak detection can be by visual inspection, possibly aided by the use of dyes or through make-up oil records. Containment can be achieved with absorbent pillows, pads and rolls; flexible tube socks; dikes; needle-punched polypropylene fibers; loose granular corn or peat moss materials; drip pans and drain covers.
This lack of attention to a few basic details costs millions of dollars annually in make-up oil, cleanup, disposal of external fluid waste, unnecessary maintenance downtime, safety and environmental damage.
Is it possible to stop external fluid leakage? It is estimated to be 75-percent correctible. What is required by machine design engineers and maintenance personnel is much more strict attention to the correct selection and application of seals and seal materials.
When designing machinery and selecting the appropriate seal materials, design engineers may occasionally choose inappropriate seal materials, primarily because they underestimate the temperature range under which the machine may eventually operate. This is probably the main reason for seal failure from a design point of view.
From a maintenance point of view, many maintenance managers and purchasing agents select replacement seals for the wrong reasons. In other words, they put seal replacement cost ahead of sealing effectiveness or fluid compatibility.
In order to make better decisions regarding seal selection, maintenance personnel, design engineers and purchasers should become more familiar with the types of materials used for seal manufacture and where these materials can be used most effectively.
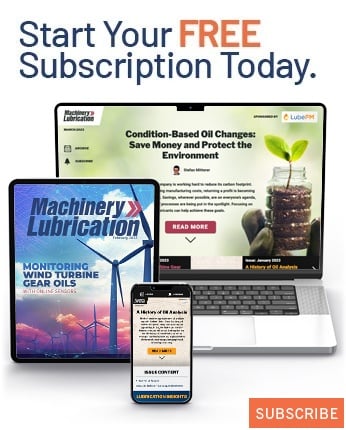