"We are having trouble supplying grease through grease extension lines because the grease appears to be separating and losing its properties before it reaches the bearings. What is the proper method for using grease extension lines to effectively provide good grease to the bearings?"
In industry, it is very common to see extension hoses used to supply grease to fittings that are difficult to reach or in hazardous environments. Greased bearings are commonly located high and out of reach, below floor grading or in dangerously high-temperature environments such as near dryers on a paper machine.
The application of a hose extension becomes a necessity to allow routine greasing without causing machine downtime, subjecting personnel to unsafe temperatures or moving equipment.
While an extension hose may seem like an obvious solution, it can pose one serious problem: grease can separate within the hose. The two primary properties of grease — base oil and thickener — are at risk of separating when certain parameters are met.
Time alone can cause grease to separate. This can be seen when a drum of grease has been sitting untouched for some time. When the drum is finally opened, a layer of shimmering oil — the base oil — is sitting on top of the grease. Other factors such as temperature can also increase base oil separation from the thickener.
A likely scenario would be to use an extension hose that is several feet long to grease a particular bearing. The bearing is supplied a "fresh" shot of grease every few months, which equates to approximately a foot or two of grease in the hose.
If the hose is hung downward from the bearing and in a high-temperature environment, the grease inside the hose may separate, causing only base oil to be waiting at the top of the hose for the next injection into the bearing. In just a few weeks, the bearing may begin to show signs of wear from insufficient lubrication.
Within a month or two, the bearing may fail and need to be replaced. Without knowing the root cause of the problem, the next bearing could fail under the same circumstances.
The solution to this problem is to find a way to supply fresh grease at a distance from the bearing while preventing the grease from becoming stagnant in the degrading environment of the extension hose.
This can be accomplished simply by having a wye in the bearing’s grease fitting with two hoses extending from the wye to a safe regreasing location. With one hose supplying new grease and the other uncapped, new grease can purge the hose completely until fresh grease emerges from the uncapped hose end.
At this point, the uncapped hose end can be capped, and any additional grease pumped into the hose will be directed to the bearing. While this may result in some unused grease, it will ensure the goal of supplying fresh grease to the bearing is achieved.
Read more on bearing lubrication best practices:
How to Protect Bearings from the Elements
Grease Guns - Learning the Basics
10 Tips for Maintaining Grease Guns and Fittings
The Grease Gun: Applications, Uses and Benefits
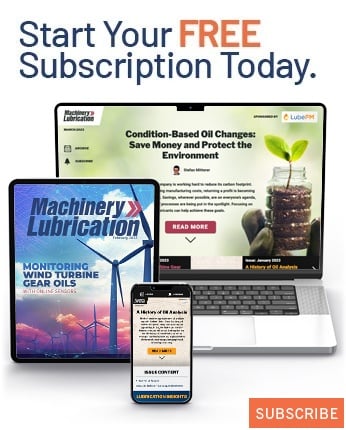