While traveling and teaching lubrication fundamentals courses at various facilities across the country, I am constantly reminded of the misconceptions that are rampant in our industry. Recently, I was asked the question, “How do you determine the proper circulating oil flow to a journal bearing if you know the shaft speed, clearance, oil type and temperature?”
Like many things in lubrication, the answer is not nearly as simple as it may seem. Several concepts must be explained, including some of the design processes that are involved in determining the correct journal and bearing dimensions, materials and lubrication requirements.
Several names are used for these types of bearings, such as journal bearings, sleeve bearings and plane bearings, just to name a few. The basic function of a journal bearing is generally to support a shaft. This type of bearing usually is chosen for applications that are not subject to changes in shaft speed or load.
There are three major components of this type of system: the stationary part or the bearing, the moving part or the journal, and the lubricant. The system’s metal components may consist of any number of materials. The bearing normally is made of a softer metal than that of the journal to prevent wearing of the moving element.
Typically, the lubricant enters the bearing from the center and passes through to the ends where it leaves the bearing. The lubricant performs several functions including providing controls for friction, wear, corrosion, temperature and contamination, as well as a power transmission component.
In journal bearing lubrication, three basic lubrication regimes apply: hydrodynamic or full film, mixed film, and boundary. It is important to note that regardless of how well a metal surface is machined, imperfections still exist. These little peaks and valleys are known as asperities. The three lubrication regimes essentially refer to the amount of contact between these asperities.
The vast majority of journal bearings are designed to operate in the hydrodynamic (full-film) regime. However, these bearings spend a portion of their operating life in the other two regimes as well, so they also deserve an explanation.
In his article “Boundary Lubrication, an Appraisal of World Literature,” W.E. Campbell defines boundary lubrication as: “... lubrication by a liquid under conditions where the solid surfaces are so close together that appreciable contact between opposing asperities is possible.”
In short, boundary lubrication is the regime where metal-to-metal contact occurs and the largest portion of wear is generated. The vast majority of the load is being carried by these asperities with very little, if any, being carried by the lubricant. This typically takes place upon equipment startup.
In mixed-film lubrication, a little contact between the asperities still exists, but the lubricant is also supporting some of the load. This transpires shortly after startup but prior to reaching normal operating speed. Harry C. Rippel’s book, The Cast Bronze Bearing Design Manual, describes mixed-film lubrication as: “... part of the total load carried by the bearing is being supported by individual load-carrying pools of self-pressurized lubricant and the remaining part by the very thin contaminating film associated with boundary lubrication.”
Once the normal operating speed is reached, full-film or hydrodynamic lubrication is achieved. In this regime, the two metal surfaces are separated by a lubricant film to such a degree that the asperities no longer come in contact. It makes perfect sense that if you maintain full separation of the metal surfaces with a lubricant in between, no mechanical wear will occur. In fact, it has been stated that as long as this condition exists, these bearings can operate indefinitely without wear.
Typical journal bearing
This process can be compared to water skiing. While the boat is idle, the skier is in the water, which is equivalent to a boundary condition with the lubricant providing no support to the shaft. As the speed increases, the skier rises out of the water. This is similar to the mixed-film regime, as the water is providing some support to the skier. Once the boat is up to speed, the skier is fully out of the water and riding across the surface (full-film or hydrodynamic lubrication).
Fluid pressure is generated in the lubricant film, which is able to support load due to its viscosity. Lubricating oils have a significant pressure-viscosity coefficient. This means that the greater the pressure on the lubricant, the higher the viscosity at the pressure point. In the case of rolling-element bearings, this pressure is high enough to raise the lubricant’s viscosity to the point where it will deform the bearing’s rolling elements. This pressure-viscosity coefficient is what provides the load-carrying capacity of a journal bearing.
With a better understanding of lubricant films, let’s now look at the two equations for determining the lubricant oil feed to ensure a sufficient quantity of lubricant to support the load in a journal bearing. The equation you use to calculate the proper circulating flow will depend on whether you are working in gallons per minute or in drops per minute. The equations can be seen in the box above.
While most of the variables in these formulas are straightforward, the clearance factor (m) may be confusing for some. It can be determined by calculating the diametral clearance (2C), which is equal to the bearing bore diameter minus the journal diameter. Obviously, the clearance will be much smaller than the journal diameter (D), so this value is multiplied by 1,000 to make calculations easier. Therefore, the clearance factor is: m=1,000(2C/D).
Returning to the original question about establishing the proper oil flow to a journal bearing, in this instance, the clearance was known. The diameter and length should be easy to obtain either by taking a measurement or by checking the documentation. The speed was also known, so the only value left to find is the load (W). This is simply a matter of determining the weight of the rotating element divided by the number of bearings.
Once all the values have been identified and the appropriate equation selected for gallons or drops per minute, you just need to enter the numbers into a calculator.
References
Campbell, W.E. (1969). “Boundary Lubrication: An Appraisal of World Literature.” ASME.
Rippel, Harry C. (1960). Cast Bronze Bearing Design Manual. Cast Bronze Bearing Institute Inc.
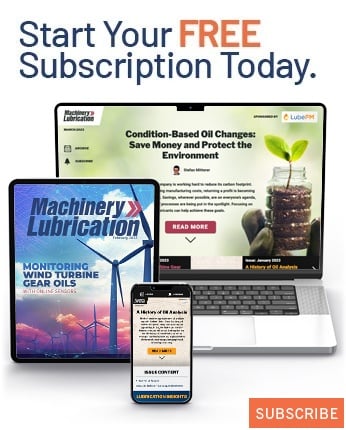