Going “green” by becoming ecologically and environmentally responsible is an excellent practice that does not always have to cost your organization money. In many cases, it can actually save money. A number of industries have begun reclaiming, recycling or even regenerating oil because it makes good business sense. These include automotive manufacturers, steel mills, paper mills, sugar mills, process plants and power generation plants.
Unfortunately, some companies do not reclaim, recycle or regenerate used oil because they think they don’t have the time or budget to devote to these programs. The engineering/reliability managers of these plants are often so busy managing the day-to-day processes that little or no attention is paid to the total lubricant life cycle, which in most instances would make their process more reliable and less expensive to maintain. In the case of oil regeneration, they may even be able to extend the service life of oil indifinitely, which also improves machine service life by maintaining oil at high levels of cleanliness.
Reclaiming or regenerating oil offers many benefits, such as increased machine reliability, considerable cost savings on oils, less time spent on oil change-outs, reduced environmental contamination and decreased waste disposal costs.
Oil Reclamation
Regeneration, reclamation and recycling are related processes but with significant differences. Reclamation is the act of salvaging, recovering or reclaiming. In this context, the oil is temporarily rescued from normal degradation. It generally involves cleaning, drying and adsorption to remove water, acids, sludge and other contaminants. The reclaiming of oil is mostly a nonchemical process that restores an in-service lubricant to good health for a time by removing impurities. Processes like centrifuging may also be used to remove suspended particles and some water. Many oil reclamation units dry the oil by heating it and applying a vacuum. Vacuum dehydrator units can be utilized onsite and are great assets if the costs can be justified. If not, you will need to have your oils reclaimed offsite.For the most part, reclamation can and should be done onsite to mitigate the chances of cross-contamination. Reclamation may also take place offsite where the vendor of the reclamation service drains the existing oil and replaces it with previously reclaimed oil.
Keep in mind that if the oil is removed from the plant and reclaimed at an offsite location, the potential for cross-contamination increases tremendously. In addition, if an oil spill or accident occurs during transport to the facility, the owner of the oil is liable.
Some oils like motor oils cannot be reclaimed, while others should not be reclaimed due to the costs involved. Additive formulations may be proprietary, or the additives are not easily sourced. There is also the question of whether the reclaimer would be able to finance the liability of equipment damage, downtime and/or bodily harm if there was a mixup with the viscosity or additive formulation.
The best option is to have your newly reclaimed oil tested by a reputable lab to ensure it complies with the machine’s original equipment manufacturer (OEM) specifications before it goes back into service.
Regenerating Oil
One of the more advanced ways to treat your in-service oil is to regenerate it. While oil regeneration is a newer technology, there are already robust solution offerings available from companies like SKF RecondOil that are helping plants around the world to go beyond oil recycling or reclamation. Oil regeneration represents a shift in how we relate to industrial oils. Moving from treating them as a consumable product to vieweing them as a long-term asset in our maintenance and reliability programs.
Unlike recycling, which focuses on using contaminated oil for other applications where degraded oil will not have a significant negative impact (such as lubricating a chain or making asphalt), oil regeneration maintains the oil in a like-new state. While reclamation is similar to regeneration because it is focused on returning oil to a usable state, eventually oxidation products in the oil will degrade it to a point where it can no longer be used in the application.
Through processes like SKF RecondOil's Double-Separation Technology (DST), combined with additive top-ups and other treatment methods, oil regeneration allows us to maintain oil in a highly clean state that allows it to be continually re-used, even indefinitely. In some applications, the same oil can be used for years and years with performance characterstics that are equal or better than "new" oil.
This shift toward oil as an asset represents an exciting and potentially disruptive change in the lubricants industry because it allows plants to simplify many processes. If less oil changes (or even no oil changes) are required, the associated labor, potential for contamination during transport, issues of storage, available supply, price changes and many other problems that have long been seen as "necessary evils" of lubrication may be avoided entirely. Lubrication is always evolving, and it is exciting to see how new technologies will change the face of the industry today and in years to come.
Recycling Oil
Recycling is one of the simplest methods to get more use out of degraded oil. Recycling means returning something or a part of something back to useful service, which may be different from the original application. Whether it is in an engine, gearbox, hydraulic system or turbine, unless it is being maintained through regeneration technologies, all lubricant oil eventually reaches the end of its useful life and must be drained from the machine, sump or reservoir.
Some forms of oil recycling can be done onsite. If your plant produces large amounts of used oil that can’t be reclaimed, this used oil can be turned into lubricant oils or fuel for burning in boilers, industrial furnaces, etc. On the other hand, if your used oils must be sent offsite because they are too badly contaminated with different viscosity/base oils and chemicals, or your plant does not have the volume to justify onsite recycling, make certain that the used lubricants are handled and processed in an environmentally acceptable manner by a waste-removal/recycling company.
A number of recycling organizations are available, but you must ensure that you are dealing with a reputable company that processes the oil correctly in compliance with your local laws and U.S. Environmental Protection Agency (EPA) regulations.
What is Used Oil?
The U.S. Environmental Protection Agency (EPA) defines used oil as “any oil that has been refined from crude oil or any synthetic oil that has been used and as a result of such use is contaminated by physical or chemical impurities.”
Oils used as lubricants, hydraulic fluids, heat transfer fluids, buoyants and for other similar purposes are considered used oil. Some examples include engine oil, transmission fluid, lubricating oil, hydraulic oil, gear oil, transformer fluid, cutting oil, tempering or quenching oils, greases and brake fluid.
Used oil does not include oils made from vegetable- or animal-based oils, oil wastes that have never been used (e.g., virgin oil spills), antifreeze, kerosene, or petroleum distillates used as solvents.
What is the Best Option?
Keeping your oils in service as long as possible is beneficial to your business in many ways. The cleaner and drier the oil, the longer your machines will last. Therefore, cleaning your oils while they are still in service and not allowing them to be used to the point of no return (viscosity degradation/oxidization) makes perfect sense. To achieve this, you first must know which oils can be reclaimed or regenerated.
Typically, hydraulic oils, turbine oils, circulating oils for bearing lubrication, paper machine oils, gear oils, quench oils, some metalworking fluids, transformer oils, some synthetics and several specialty fluids can be reclaimed or regenerated through various processes.
Next, you need to determine your oil’s remaining useful life through oil analysis. Do not just rely on interval-based oil changes for your reclamation or regeneration program. You may be leaving the oil in the machine too long. Employ a quality laboratory or bring in a service provider to help conduct the testing and make sure you have a baseline sample from the new oil as a reference for the viscosity, cleanliness and additive levels. This will help you discover what’s happening to the oils in your machinery and how their life is being impacted.
The oil should be tested for the following:
- Viscosity at 40 degrees C (ASTM D445)
- Acid number (ASTM D664)
- Rotating pressure vessel oxidation test (ASTM D2272)
- Water separation at 130 degrees F (ASTM D1401)
- Trace metals analysis (ASTM D5185)
- Cleanliness level standards (ISO 4406:99)
- Pressure differential scanning calorimetry (ASTM D6186)
Plant personnel should be trained to read sample reports and to take samples correctly with the right equipment. You may need to outfit your machinery with better breathers, quick connects and filters to keep as much contamination out of the machines/systems as possible.
Reclamation involves the oil being filtered and cleaned of debris, sludge and contamination particles. Regeneration takes this a step further by continuously giving oil "new" life by removing the smallest and most destructive particles while maintaining the other properties of the oil. Your choice of recycling, reclamation or regeneration will depend on your application and related business goals. If you are looking to extend the life of oil in the same application, reclamation could be a good option. If you are looking to reduce the total cost of ownership of machines and related assets, oil regeneration may be a more holistic choice with the greatest impact on the bottom line. In either case, it is imporant to ensure the solution you choose is compatible with your lubricants and your ultimate goals. Be sure that you work with solution providers to understand the challenges and opportunities associated with any of these options.
Selecting a Reclamation or Regeneration Company
To help determine a prospective solution partner's credibility and expertise, it is important to ask a few simple questions, such as whether the oil is tested before and after it is processed, if particle count data is provided at the site during reclamation or regeneration, what the cost savings associated with these processes are, if the oil can be refortified legally and accurately onsite, whether the original formulators are involved, and how the reclamation or regeneration will impact the machine’s warranty.
In conclusion, all plants should have a coordinated plan for managing used lubricating oil, including how much oil is reclaimed or regenerated and how much is recycled. Cleaner production methods and a focus on minimizing waste are the first steps to reduce used oil.
However, once the oil reaches the end of its useful life, it should be either regenerated, reclaimed or recycled. If reclaimed, the oil may continue to serve its designed function for many more operating hours. If regenerated, the oil could serve in the same application for many years. Rigorous testing and record-keeping will be necessary for either approach.
If the used oil is a mixture of contaminants and waste oils or has been severely degraded and cannot be regenerated or reclaimed, then it should be reprocessed by a recycler or repurposed into fuel. Of course, all of this is dependent on the type of contamination in the used oil.
Finally, be sure to follow all local laws and regulations for used oils. If you do not, harsh fines may be imposed.
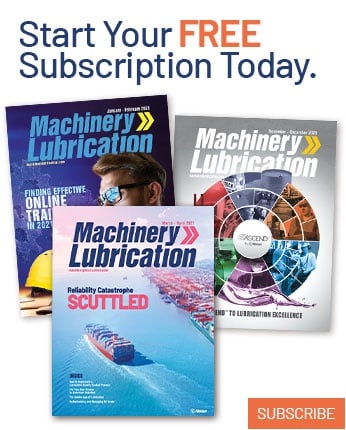