.
What is reactive maintenance, and how do you know if your company is practicing it? Many people like to hide reactive maintenance and call it something it’s not, but if you honestly answer “yes” to any of the following questions, then you likely are stuck in the reactive rut:
Are you measuring how fast a piece of equipment gets fixed once it breaks down? Are you patting guys on the back for fixing broken equipment rather than keeping it from breaking? Do you think cutting maintenance costs starts with manpower and/or material? Are your maintenance costs increasing even though you’ve implemented sound strategies? Are you rewarding failure?
Some of these questions may sound ridiculous, so let me explain. For example, you may ask what company in its right mind would reward a failure. But do you award overtime to your millwrights or mechanics for coming in at night or on weekends to fix broken machinery? If so, you are rewarding the failure of that machine.
A better strategy would be to reward the team when there are no failures. Don’t you think maintenance personnel would focus on keeping a machine in optimum condition if their reward was tied to the machine’s continual operation and availability as opposed to its failure? This is a significant cultural issue at a number of the plants I visit, and it is not an easy hurdle to overcome.
Changing from reactive to proactive maintenance requires a different way of thinking, executing and managing. When designed, implemented and managed effectively, proactive maintenance results in optimal asset reliability at optimal cost. Everyone wins. The company gets more value from its machines, the maintenance budget and upfront costs are reduced, profit margins increase, the actual work being done by the team is easier, etc. The list of benefits could span pages.
So why isn’t everyone striving to make this change? Change is difficult, and people tend not to like it. Although change is not simple or easy, it is achievable. Not only is change achievable, but lots of people are making it happen.
There are many strategies for change management, including a few I will discuss later. However, the first thing you must do is to believe that making the change will have a lasting effect on the organization and the people within it.
Anyone who works in maintenance and reliability is probably aware of the frustrating consequences of unexpected equipment breakdown (the definition of reactive maintenance). Some organizations have hundreds or even thousands of pieces of equipment to maintain, and a single breakdown could bring operations to a halt. If the organization is running at full capacity, this loss can never be returned. While there’s no doubt that fixing something as soon as it breaks is important, few people realize the high costs associated with working in reactive mode.
45% | of plants utilize a proactive maintenance strategy, based on a recent poll at MachineryLubrication.com |
Maintenance Management Approaches
There are three basic approaches to maintenance management: reactive, predictive/preventive and proactive. Reactive maintenance, which is precipitated by failure, results from a lack of preventive and predictive maintenance. On the other hand, proactive maintenance keeps equipment serviced and in working order through preventive and predictive maintenance as well as a keen focus on eliminating the root causes of failure.
A reactive maintenance approach can be detrimental to your organization because it means that you could get stuck in a vicious cycle of constant emergency work pushing aside the tasks that could lead to a reduction of that very same emergency work at a future date. Furthermore, reactive maintenance is much costlier than proactive work. This is because reactive maintenance tasks tend to be complex, like tearing apart a gearbox to fix a bearing, whereas proactive maintenance tasks are relatively simple, such as sensory inspections and small corrections.
Starting the Journey to Proactive Maintenance
This type of change cannot be made with a simple flip of a switch. It will be a long, drawn-out process that is more of an evolution than a change. Even when all is said and done, you may never rid yourself of reactive maintenance work. However, you can significantly minimize unplanned repairs.
Implementing an enterprise asset management/computerized maintenance management system (EAM/CMMS) that is customized to fit your organization’s specific needs can help in shifting a reactive maintenance program to a proactive one. You will need a way to organize, measure and analyze lots of data. Without the help of software and the supporting structure behind it, your efforts will need to be multiplied many times.
The main goal of this software is to help provide proper planning and scheduling of your preventive and proactive maintenance. Maintenance costs can never be eradicated, but they can be redirected. You want to focus your time, money and energy on making sure that proactive tasks are being completed, because when done correctly, they will result in a massive reduction in reactive tasks. You are in effect trading complex, harder work (reactive maintenance) for easy, cost-effective work (proactive maintenance). Software should be able to help facilitate this trade.
Preventive Maintenance
The first step toward proactive maintenance is using data from past experience to drive your maintenance timelines and decisions. For example, if you know a certain sump pump has a life expectancy of three years for its operational and environmental conditions, and you know this because you have data spanning back a decade, then it would be safe to say that you need to plan and schedule to replace or rebuild the pump at the 2.5-year mark. While this obviously is not the best case scenario, because you might be changing out a perfectly operational pump at the 2.5-year mark, this strategy can reduce overall costs in both the short and long term, as opposed to an unknown catastrophic failure that occurs unexpectedly.
This approach still requires significant manpower to perform tasks that at the time may seem unnecessary. However, this extra effort can pay off in the long run when things like production uptime and being able to plan the work are added to the equation.
According to a case study by the Office of Energy Efficiency and Renewable Energy, practicing periodic component replacement in the form of preventive maintenance saves an estimated 12 to 18 percent over reactive maintenance.
Predictive Maintenance
The next step toward proactive maintenance is being able to assess the machinery’s current condition. Predictive maintenance will enable you to better plan corrective actions before the equipment experiences a catastrophic failure. A variety of technology tools can help with this, and the main goal of each is to measure failure symptoms or faults. These tools and technologies are usually non-invasive and can monitor machine and component conditions through direct monitoring and analysis.
The one inherent flaw with this strategy is that in most cases you are measuring failure symptoms or faults. This means that by the time you have something to measure, the problem already exists. There is certainly great value in knowing that a problem exists and being able to perform corrective actions before it becomes catastrophic, but you can do better. If your program has evolved to this point, a case study from NASA suggests you are saving up to 50 percent on maintenance costs compared to reactive maintenance.
Proactive Maintenance
Up to this point the evolutionary steps have been quite easy and gradual. Making the leap to proactive maintenance requires a change that is difficult for most organizations to master because it requires a shift in thinking, processes, procedures and culture. Proactive maintenance doesn’t focus on repairing machines or being more effective in performing corrective actions on machines that show signs of problems. Instead, it concentrates on eliminating the root causes of the issues. If you can eliminate the root causes, you won’t have the failures these root causes eventually would have turned into emergency work.
One of the simplest ways to move toward proactive maintenance is through education or training your frontline people on what to look for and why. This is essentially what proactive maintenance comes down to - knowing the root causes that lead to the majority of machine failures, knowing what they look like and knowing why it is important to correct the issue at this stage versus waiting until later in the P-F (failure) curve. These types of inspections can save organizations tremendous amounts of money, but they are often overlooked for their simplicity.
For instance, consider checking the oil level in a splash-lubricated component. Although this is extremely easy to do and only requires the briefest of training, if not done, it could lead to catastrophic failure of the component and everything associated with a breakdown.
With proactive work, you want to trade the costly breakdown in the future for the time, money and energy up front to perform a simple inspection. This is almost always a favorable trade and will lead to a massive reduction in maintenance and production costs. Of course, it doesn’t always work out that way.
Not all programs and strategies fit a perfect mold. Each program needs to balance the cost of implementation with the expense of being complacent. For instance, it is perfectly acceptable to utilize a reactive maintenance mode for a cheap component that is easily changeable and readily available. It doesn’t make sense to spend a lot of time, money and energy on a sump pump that costs $500 from a mail-order catalog, has three available spares, takes five minutes to change and is not part of a critical process.
The ideal program will be able to use a variety of maintenance modes to make sure the plant is running as efficiently and effectively as possible. Understanding the different maintenance philosophies and having an excellent grasp of operations, machine criticality, costs, etc. will be essential in adopting a balanced approach at your plant. Only once all the variables are fully understood can you optimize your program and start getting the most from your people and machines.
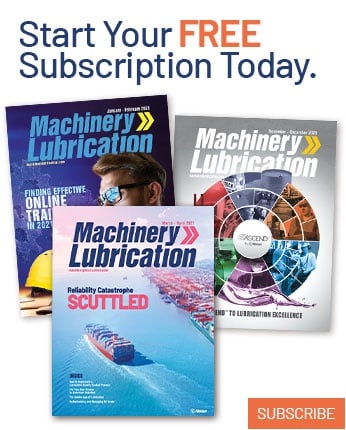