"What is the best way to manage lubrication information for plant assets and their maintenance records?"
Information management is a key factor in the success of a maintenance and reliability program. It is also one of the most challenging aspects due to its complexity.
The first step is to employ a good system (software) that can manage your asset information properly. The system should include a complete database of asset information (models, specifications, capacities, etc.), detailed information for each asset's lubrication requirements (lube points, lubricants to use, lubricant capacity, frequencies, etc.) and comprehensive information related to the work instructions (safety requirements, necessary materials, time to complete the task, relevant activities and lubrication data).
The management system should also be able to generate routes based on different criteria (lubricant type, geographical area, machine type, task and frequency) and work orders according to their priority (critical machines, tasks due, routine or on condition).
Do not overlook the role of the maintenance team, which must be trained and qualified to execute the required lube routes and tasks. Floor personnel should also collect information about the results, including completed tasks, detected abnormal conditions or the need for additional actions. Appropriate written instructions, checklists and records must be available to support these activities.
The collected information should be saved in the management system for maintenance administration and stored for as many years as practical. This historical information can then be analyzed to identify trends and failure frequencies in order to improve the plant's maintenance strategy. Reports can also be created to show the performance of different aspects in the program.
A system of performance indicators will be necessary to monitor the program's progress and results. Remember, processes that are not measured are also typically not controlled. The system should have the capability to not only generate statistics and calculations on the overall maintenance program but also the performance of various parameters, such as lubricant consumption, machine failures, cleanliness targets, etc.
All maintenance and reliability team members should have access to this information based on their level of involvement in the program. This will encourage them to embrace ownership of the work being performed.
While it may take time to implement a system with all of these suggested attributes, it is important to keep in mind that good information management starts with a robust database and detailed work procedures and policies.
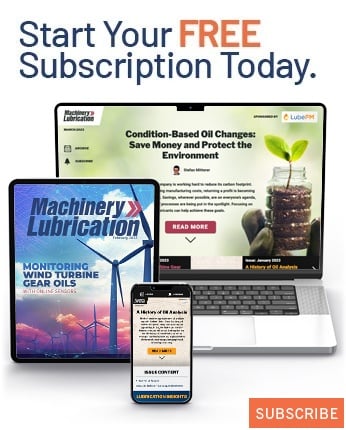