"Our existing oil analysis program has lost its business value. Where should the focus be to get the value back for both the customer and dealer?"
It is essential for oil analysis users to understand the capabilities of the various tools in order to take full advantage of them. In general, oil analysis can be utilized to determine three conditions: machine wear levels, undesirable contaminants in the oil and lubricant properties or performance. If you are simply managing your oil analysis program by checking to see if the reports have red, yellow or green flags and then taking the recommended actions, you are losing a lot of the program’s value.
Be sure to consider all the possibilities in terms of the available tests, their purposes, locations and times at which they can be conducted in the lubricant’s life cycle. A successful program not only will be used for routine analysis of the in-service lubricant but also for several other purposes. These would include monitoring the incoming lubricant’s cleanliness and integrity during storage, identifying root causes after a failure, verifying the lubricant’s condition and ability to continue in service after filtration or "sweetening," optimizing oil change intervals, validating the performance of a new lubricant, or assessing the effectiveness of the contamination control program.
For in-service oil, different test slates can be combined and quick field tests employed to determine the lubricant’s condition so you can take immediate action. Exception tests typically are performed at more extended intervals (e.g., every year) to analyze lubricant performance. This is particularly useful in large-capacity systems where the lubricant life is long or the change-out cost is high.
Oil analysis can also be progressively modified to enhance your reliability program. Targets and limits for test results may be altered based on your plant’s reliability goals or success of the contamination control program. Oil sampling frequencies may be adjusted accordingly. In some cases, different technologies or methods should be used to measure a parameter. These should be selected based on the criticality of the test results.
Understanding the possibilities of oil analysis is also important for clearly defining the program’s goals. Appropriate sampling procedures and frequencies will be fundamental for the program’s success according to the established objectives. In addition, it may be necessary to provide training to the program manager or floor personnel.
By making your oil analysis program multi-dimensional, you will be much more likely to realize its maximum value for plant or fleet reliability.
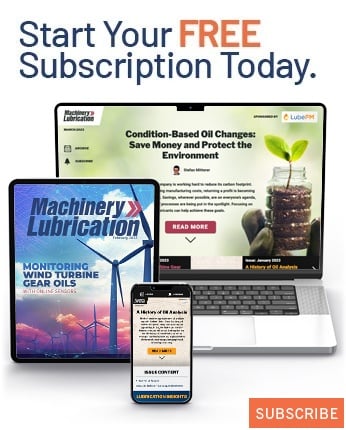