There is nothing more harmful to equipment reliability than the combination of a poor lubrication program and an untrained lube technician.
One night several years ago, I received an emergency call from an oil export terminal jetty to investigate severe leakage/splashing of hydrocarbon product from the loading arm joint.
I rushed to the incident site with various questions in mind. The product transfer had been immediately stopped by the shift operator, and due to poor visibility at the loading arm area at night, I was unable to determine the exact location of the leak.
The next morning while interviewing the operator, I learned that the leak was from the swivel joint on the newest of the loading arms installed at the jetty, which had been commissioned just six months earlier.
He reported that this type of leak had not happened in the past on previously installed loading arms at that jetty. In response to my question about whether any maintenance activity had been performed on this loading arm in the last few days, the operator replied, "Yes, the lube technician yesterday conducted the six-month greasing activity."
I then questioned the lube technician who performed the greasing job at this jetty and asked him if he found anything abnormal while greasing this new loading arm. He said that he had been greasing all the loading arms every six months for the past 20 years with no issues.
Yesterday he had been given a work order to apply grease as per the six-month PM schedule. However, this time the new loading arm was also included along with all the old loading arms. When he began greasing this new loading arm, it was difficult to push grease into the swivel joint through the grease gun, but after a few hard strokes, it became easier.
This discussion provided me with some clues, so I went to the document controller and requested the maintenance manual for the new loading arm. In reviewing the cross-section drawing of the swivel joint, I found there was a grease leakage plug that seemed to be the culprit.
The greasing procedure in the manual clearly mentioned to remove this plug before applying grease to prevent a seal rupture. I got confirmation from the lube technician that he had no idea to remove this plug before applying grease to the new loading arm.
I still had questions about who should be blamed for this incident, which could have led to severe consequences in terms of safety, cost, reputation, etc. Was it an error by the lube technician or his supervisor who did not brief him about the new loading arm greasing procedure?
Was it negligence on the part of the project team which didn't develop detailed procedures and upload them into the company's computerized maintenance management system (CMMS)?
Was it the mistake of the operations team which had this equipment handed over to them without the proper documentation being uploaded into the CMMS? Was it the fault of the operations readiness and assurance (ORA) person who did not complete the pre-startup audit for this new asset?
Regardless of who is blamed for this type of failure, it is a proven fact that companies lose millions of dollars every day in terms of lost production and maintenance costs due to breakdowns that could have been avoided through better lubrication practices.
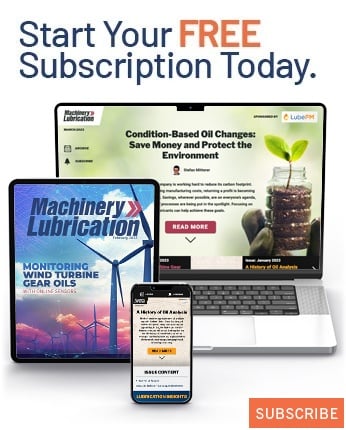