For an effective oil analysis program, it is essential to set goals for tangible and defensible improvements. Here are four key areas to focus on this year: optimizing oil sampling, eliminating uncertainty in lab report interpretation, advancing your equipment list and following a path to improvement. Select one or all four, and seek team buy-in as soon as possible.
Optimize Oil Sampling
Take the time to assess your company’s oil sampling strategy and execution. There are always methods of enhancing your technique, sample location, sampling device or frequency. Typically, the individuals in charge of extracting samples are not offered the opportunity to offer their ideas for improvement. In addition, oil sampling technicians often are not encouraged to analyze lab reports.
This year, make time to do the following: Join your lube tech for a round of pulling routine samples, discuss optimal sampling techniques as a group, learn from the lube tech where sample locations can improve, and urge everyone on your team to review the lab reports and provide suggestions.
If the same contamination alarms are triggered repeatedly, examine the oil analysis reports to identify where the sampling technique or location could be improved. Recurring water contamination or heavy wear particle contamination from the same sampling locations usually indicate a need for modifying the sampling technique or location.
Eliminate Uncertainty in Report Interpretation
Laboratories do not expect their clients to understand everything in an oil analysis report without training. To fit test results on one- or two-page reports, labs frequently use acronyms, abbreviations and abridged language that may not always be as easily understood as they should be. It’s rare when all stakeholders in a reliability group are trained to interpret results and can put the puzzle pieces together from the package of tests run on a sample. Laboratory personnel know this and expect interested parties to inquire for the benefit of making informed decisions that can increase machine reliability. Therefore, call, email and request training from your lab. It’s their job to help you.
Advance Your Equipment List
Assist your lab in improving the analysis by providing more detailed information about your lube systems and critical equipment. The following details will be helpful: system oil capacity, date of last oil change, date of last filter change, correct oil brand and viscosity. Ask your lab for the list of sample locations and lubricated equipment to verify existing database records and supply any additional information required.
Follow a Path to Improvement
Set goals for your oil analysis program and define a path for improvement. The most common goal is to reduce the number of warning alarms triggered by equipment or oil condition issues discovered in lab reports. If a routine batch of monthly samples averages 30 warning alarms, try to cut that number in half this year.
The first step to reduce warning alarms is pinpointing where the lab has set unattainable alarm thresholds. In other words, the alarms aren’t properly set. If you make a reasonable request that doesn’t risk the reliability of your equipment, your lab should adjust these threshold alarms.
Once your team has bought into the goal of reducing alarms and all members understand how they can make a difference, you will naturally chip away at the problems and begin to make a positive impact on your oil analysis results.
Many programs focus intently on the ISO code for oil cleanliness. If your organization has already tackled the low-hanging fruit, it might be time for a joint effort to lower the ISO code by one or two levels this year. Attempt this strategically and set a reasonable goal. For example, if certain screw compressors always have higher ISO code results, then agree to exclude them from the calculation.
Oil analysis labs pay close attention to wear metal contaminants detected in emission spectroscopy. Pinpoint the lubricated equipment that are your repeat offenders for high levels of iron, copper, tin and lead, and determine what will be necessary to make those numbers drop this year. Strive to stop letting those machines trigger warning alarms on your lab reports month after month.
Finally, keep in mind that the most impactful way to quantify improvement, especially for upper management, is to lower maintenance spending without compromising asset reliability over the short and long term.
About the Author
Ben Hartman is the president of MRT Laboratories.
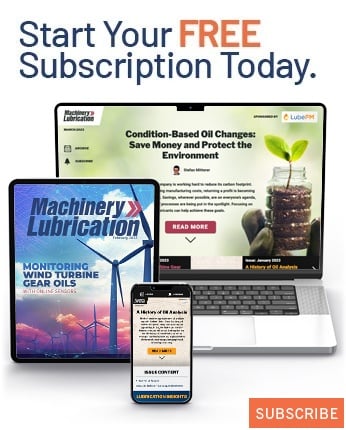