"Due to our limited human resources, we currently are sampling the oil in our turbine bearings on a yearly basis. Is this type of interval adequate for detecting failure modes or should the frequency be increased?"
How often to take a sample is one of the most critical decisions in an oil analysis program. An appropriate routine sample frequency would be somewhere between two weeks and three months. Since the specifics for this turbine are not provided, the following recommendations will be generalized to apply to any machine.
The optimal sample frequency for any application should be based on your reliability objectives. First, ask the following questions: How much would it cost my company (in parts, labor and downtime) if the machine suddenly failed? Is there a safety risk associated with a failure? How much would I be willing to invest to forecast the failure 24 hours, one week and one month in advance?
The price you are willing to invest is the theoretical break-even point with all condition monitoring deployed on that machine. Considering that oil analysis may be only one of several condition monitoring strategies deployed and knowing that it is not an absolute solution for predicting failure, you might not invest up to that break-even point. However, some amount less than that would be acceptable.
For example, if your break-even point is $40,000, it may be reasonable to invest $5,000 in oil analysis to predict a failure on the machine. So, if the total cost of each oil sample taken is approximately $50, you may be willing to sample at least 100 times within the estimated time between failures. If there is a safety risk as a result of component failure, the price you are willing to invest to indicate a failure mode may be much more and could even exceed the initial break-even point.
The next step is to account for the environment, machine failure history, component type, age of the components, etc. How likely is it for the machine’s internal lubrication zones to be exposed to contamination? Has the machine recently been installed or is it approaching its design life? How quickly might a known root cause lead to catastrophic failure?
Predicting a failure with oil analysis is all about having the opportunity to witness the root causes or the symptoms of the failure mode at some point within its failure development period (FDP). The FDP is the time between the failure inception, such as the first time wear debris is produced, to the time functional failure results (complete bearing failure). Throughout this failure in progress, the detectability increases while the potential savings from remediation decrease. Therefore, to lower the remediation costs from an impending failure, you must sample and analyze the oil early within the FDP. Unless you are lucky, you can only expect to accomplish this by sampling at a frequency higher than the FDP.
The FDP can be anywhere from a few months to a few hours. Considering that it would be too costly to sample every hour and of little use to sample outside of a few months, the ideal frequency can be cost-justified somewhere in between and may fluctuate as the risk profile changes.
The questions above should be useful in evaluating the risk profile. They not only can help estimate the machine criticality factor (consequence of failure) but also the failure occurrence factor (the likelihood of failure). When calculating this with a risk matrix, the resulting overall machine criticality can be used to identify the appropriate sampling frequency.
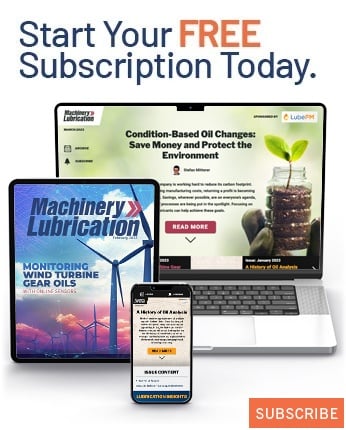