Oil analysis is a valuable tool for predictive and proactive maintenance and provides critical insights into the health and condition of machinery. Before embarking on an oil analysis program, there are a few straightforward points to keep in mind to ensure accurate and meaningful results. Let's explore these key considerations.
1. Providing Accurate Details
This information aids the laboratory in choosing the appropriate test and interpreting the results precisely including creating the baseline, caution limits, and critical limits. The process resembles how doctors diagnose patients — the more accurate the information you give your labs, the more precise the diagnosis you will get back. In the first topic, we'll classify our discussion into two main categories: registering for equipment and registering for lubricant samples.
Registering for Equipment
The registration process begins when maintenance teams decide to set up an oil analysis program for their machinery. Laboratories have to fill in specific asset details in their database. Below are the critical details that need to be provided:
- Machine Identification Name and Number: The designated name or label for the machine on which you intend to conduct the oil analysis should be one that's recognizable and commonly used by your team. While a site might have several machines that appear identical but are located in different places, the unique number associated with each machine is crucial to pinpoint the specific unit you've selected for testing.
- Unit Type: The unit type describes the general classification or category of a machine based on its primary function (such as an Engine, Turbine, Compressor, Gearbox, Motor, etc.). However, a more detailed description, like "high-pressure vane pump hydraulics," allows the laboratory to conduct a more targeted analysis using table of specific standards. If such specifics aren't provided, the lab will compare results with reference standards.
- Manufacturer and Model of Machine: Take "MITSUBISHI POWER M701J" as an example. Here, "Mitsubishi Power" represents the manufacturer of the gas turbine, while "M701J" is its specific model. Typically, these details can be found on serial plates attached to the machine. Having this information aids in identifying the machine's metallurgy and the range of wear metals to expect.
- Fluid Manufacturer, Type, and Grade: Using 'SHELL TURBO T ISO 46' for illustration: 'Shell' is the name of the fluid manufacturer, 'TURBO T' is oil type, and 'ISO 46' defines its viscosity grade. This detail assists laboratory analysts to roughly classify the formulation components and specific properties of the oil based on the Technical Data Sheet (TDS). Each type of oil has its unique pattern of degradation.
- Operating Condition: The operating condition refers to the manner and environment in which a machine is used, encompassing various specific attributes such as the machine's working at high speed, exposure to shock load, continuous operation, or working in shifts. It would impact wear rates going forward and run-time exposures.
- Work Environment and Ambient Exposures: The working environment refers to the conditions which the machine is being surrounded by during its operation, such as in extreme cold environments, radiation-intensive areas, or high sulfur facilities. For instance, machines operating in a mining environment with excessive dust can typically result in elevated silicon levels.
- Lubricant Application Knowledge: This encompasses details such as total oil volume, operating oil temperature, the use of coolers or heaters for the oil, circulating systems, and splash systems, which allow lab analysts to better understand the overall application of the lubricant.
Sample Bottle Registration
Laboratories require you to submit updated details about your oil and machine every time you send an oil sample to the lab. This can be done either on a small paper form, through a label sticker attached to the sample bottles or by scanning a QR code to fill out a form via an app provided by certain labs. Below are the critical details that must be provided:
- Machine Identification: The name and number should exactly match the registration for equipment. Oil analysis labs usually use machine names to link current results with historical data, forming a continuous trend. However, in factories where there are various machines and the staff changes frequently, issues may arise, such as calling a machine by a different name. Confusions such as "machine left vs. right" or "First machine from the bottom vs. First machine from the front" can arise. It’s highly recommended to establish a procedure that clearly guides the team on proper sampling, machine names with pictures, and data entry, to ensure everyone is on the same page.
- Sampling Point: A single machine can have multiple components and various points for taking oil samples. Clearly identifying the sampling point ensures continuity with historical data from the same location, enabling consistent tracking over time.
- Date Sampled: This marks the day the oil sample was taken, revealing consistency interval for testing as planned.
- Machine Runtime: This represents the total operating time of the machine, similar to car mileage. It helps analysts correlate machine usage with lab results.
- Lubricant Runtime: Unlike machine hours, this indicates how long the current oil has been in use. It helps the lab roughly determine whether the oil's degradation is consistent with its age or premature.
- Hot/Cold Running Condition: Specify whether the machine was in operation or shut down when the sample was taken. Taking an oil sample after a prolonged shutdown might not be ideal, as sediments may have settled, resulting in a sample that doesn't truly represent the oil in actual machine operation.
- Maintenance Action: Maintenance actions refer to activities like oil changes, filter replacements, major overhauls, repairs, and oil top-ups. This action more or less directly affects the efficiency of oil. Furthermore, in case of a switch in the oil supplier, it is crucial to provide updated information regarding the fluid brand, type, and grade.
- Report Abnormalities: Reporting any noticeable abnormal symptoms of the machine and oil, such as stable foam in the sight glass, leakage, and bottom sediment, can provide additional beneficial information for interpretation.
- Extra Test Request: Request preferred exception tests (specialty test), such as analytical ferrography, which provides a more in-depth evaluation of wear particle identification.
2. Bottle Integrity
It is common to observe new customers using recycled water bottles to take samples of oil. Because these bottles could contain leftover water residue, the detection of water in these bottles might indicate sampling oil mixed with residual water contamination, rather than solely from oil sampling.
Even in actual working conditions, the presence of water might be in normal range. The best practice is to use the bottles provided by the lab, which adhere to a standard of cleanliness and ensure the most accurate results.
Bottle Storage (Before Delivery to Labs)
Typically, sample bottles are clear to easily spot sediment and the presence of free or emulsified water. After sampling oil, it’s advisable to store the bottles at room temperature and away from sunlight. Ensure you do not store the samples for too long, though. It is best practice to send out the samples as soon as possible for current and accurate data.
Some articles explain how sunlight exposure can affect the MPC value (Membrane Patch Colorimetry) because if oil is left in the sun for a long time, it can darken and result in unusual MPC detection (especially in turbine oil). To prevent this issue, many labs provide non-translucent outer covers that can protect the sampling bottles from ultraviolet light exposure before they are delivered to the labs.
3. Sampling Conditions
While it’s common knowledge that samples should be taken from representative areas and maintain oil sample hygiene, here are a few simple but important conditions to also consider:
- Environmental Conditions: Before taking the sample, make sure the area around the sampling port is clean to prevent oil sample contamination
- Flush or “Purge” Before Sampling: It’s important to flush the dead volume 5 to 10 times prior to sampling to ensure that the oil sampled is representative of the current state of the machine.
- Sample at Operating Temperature: Taking the oil sample while the machine is in operation (if possible) ensures that the oil sample is closest to its working condition. This provides a more accurate representation of the oil's current state and performance.
- Single-Use Sampling Tubes: If employing the drop-tube method, use the tube only once to prevent cross-contamination and ensure the most accurate representation of the current oil condition.
- Consistency in Taking Oil Samples: Ensure that you are collecting the sample from the same location on the system and utilizing the same sampling procedure every single time. It is recommended to never fill a sample bottle more than 3/4 full.
- Inspect Sample Before Sending to Lab: Check that the volume of the oil sample is sufficient for testing requirements. Conduct a visual inspection of the sample to ensure it is in a suitable condition for testing. Additionally, check for sediment, water, ferrous wear (using a magnet), and any changes in color (such as darkening or haziness) that may indicate maintenance concerns. Flag any issues to the maintenance team.
Conclusion
Oil analysis is a long-term investment with significant payback. The more accurately you gather asset data, the more valuable insights you derive. Future caretakers of the machinery benefit from the historical database of oil analysis reports, allowing them to make informed decisions and takenecessary actions based on past trends.
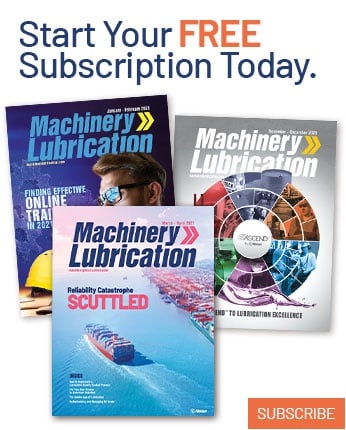