Under pressure to be more competitive, companies make strategic decisions to change their lubricant supplier. Better products, services, and lower costs are the incentives for the change.
However, the idea of changing a lubricant supplier, especially after staying with the current supplier for a long time, can be daunting. Besides the high switching costs, the uncertainty over its impact in the short term can put off many opportunities that can be gained from a new supplier.
Understanding the risks and potential issues with changing lubricants can alleviate these concerns. The risks can be categorized as performance, compatibility, and application. Mitigating these risks will ensure a successful and seamless changeover process.
Performance Risk
One of the key risks of changing lubricants is the quality and performance of the new oil. The new lubricant could be inferior and has weaknesses compared to the current lubricant, which can lead to reliability issues. You want the new oil to have at least the same or better performance than the current oil.
The first step of managing this risk is to review your equipment lubricant requirements and establish a baseline or minimum performance. First reference must always be OEM specifications. You must also consider operating conditions such as load, temperature, speed, materials, and duty cycle of lubricating components in your machines. You can then match those requirements with the new oil supplier product offerings.
Most companies choose the easier way by getting equivalents to the current lubricants rather than reviewing the machine requirements. Although quicker, this is not advisable. This practice assumes that the current product is the right lubricant for the machine. Sometimes this is not the case.
Also, the matching lubricant may not necessarily be a direct equivalent in terms of specification and formulation. Reviewing lubricant machine requirements can avoid any potential mistakes or using less than optimal lubricant.
Besides convenience, companies prefer to go on the product equivalence route because they do not have good records of machine lubricant specifications and operational requirements. All they have is a historical purchase record. Conducting a review of the lubrication requirements is an opportunity to establish a master reference of what your assets need.
Oil suppliers can claim that their oil is approved under certain industry bodies or OEM standards. As the end user, you should verify this directly with the standard issuing organization or the OEM.
There are occasions when the new supplier lubricants cannot be verified against the standards they claimed. This is because some industry bodies and OEMs do not issue approvals to specific brands. Their standards are meant to be adhered to by lubricant manufacturers, and the onus is on them to prove that their products meet the standards.
When standards cannot be verified, you may have to rely on the credibility of the oil supplier. Is there a justification to trust them? What information and track record do you know about them and their products? Is there any reference customer for whom you can get the information? Is there performance data on the successful use of new lubricant in similar machines and conditions?
In the absence of the above, you will need to evaluate the lubricant quality and performance through product testing. Commercial laboratories can perform standard tests such as viscosity, metal elements, AN/BN, and particle count. The readings can give you a basic idea of the typical properties and composition of the new lubricant.
However, to truly know its performance, advanced tests are required. This means you need access to specialized testing labs. Oftentimes, costs and time prohibit most companies from doing this.
Alternatively, you can conduct a product trial in your plant. Choose the least critical machines and run the new lubricant over a pre-determined period. Monitor machine and oil conditions via oil analysis.
It is worthwhile to shorten the sampling intervals for early detection of abnormalities. Should the trial on the least critical machines show promising results, you can increase to more machines and more critical ones.
Compatibility Risk
The new lubricants could be incompatible with the previous ones when mixed in a storage tank, potentially resulting in poor lubricant performance and other associated reliability issues. Mitigating this risk requires a compatibility assessment between new and current oils based on understanding their oil type, base oil, additive, and thickener (for grease) composition.
There are general rules of thumb to determine compatibility between products. Starting with the base oil, synthetics such as PAO and diesters are generally compatible with mineral oils. PAG, however, does not.
For engine oils, mixability between the same API classification and SAE viscosity grade shouldn't be an issue. For other oils, incompatibility is often due to mixing acidic and alkaline additive technologies together.
Mixing these two types will cancel each other. As a result, solid substances will form, changing the oil's physical and chemical properties. This is likely to occur if mixing different oil types, for example, engine oil and turbine oil.
Although it is not common to purposely mix different oil types, incompatibility still can happen for similar types, such as mixing zinc-based and non-zinc hydraulic oils. Check with your oil supplier to identify their products fall under acidic and alkaline additive technologies.
As for grease, thickener compatibility is the most crucial. Grease NLGI consistency will be affected when incompatible soap thickeners come into contact.
With many different thickeners out there, a grease compatibility table should be referenced. This is presented in Table 1:
Table 1: Grease Compatibility Chart (Source: Machinery Lubrication)
You can also determine compatibility based on the OEM and industry specifications. Certain specifications stipulated that oils must pass compatibility with different additive types of the same or related specifications. API and Caterpillar TO-4 are examples of specifications that allow mixability between oils within the same specification.
If unsure or sufficient information cannot be provided by your oil supplier, it is best to assume they are incompatible. This warrants compatibility tests to determine that the two oils combined will not undergo properties and performance changes, leading to them becoming inferior to the individual oils.
Mix the new and current virgin oils in three ratios, 90:10, 50:50 and 10:90, to simulate different mixing conditions. Heat the mixtures to 65⁰ C continuously for seven days while observing any change in appearance and sediment fallout. A clear indicator of incompatibility is deposit formation that will plug filters and hinder oil flow.
The absence of changes in the appearance does not mean the oils are 100% compatible. Critical machines such as turbines will require further tests to ensure no performance degradation is taking place during service.
Some of the follow-up tests recommended are Kinematic viscosity at 40degC (ASTM D445), Acid number (ASTM D664 or D974), foaming characteristics (ASTM D892), air release properties (ASTM D3427), water separability (ASTM D1401) and rotating pressure vessel oxidation test (ASTM D2272).
If any of the new lubricants are found to be incompatible, steps need to be taken to minimize contact with the current lubricants during transition. Airtight lubricants change-out procedures must be in place to eliminate any possibility of mixing incompatible fluids whenever practical. For example, storage tanks and machine compartments need to be flushed and cleaned before filling in with the new lubricants.
Application Risk
Application risk involves maintenance staff applying the wrong oil due to unfamiliarity with the new lubricant naming and packaging. This mistake can be catastrophic.
A proper management of change process is key to managing the transition. One person should be assigned as the overall champion or project manager to handle the change process from start to finish. Involve the oil supplier and all stakeholders within your plant to get their input. We do not want to have change-over issues by an oversight.
Communication is paramount. All users, especially personnel who receive, store, transfer, and fill lubricants into machines, should be made aware of the changes. Easy-to-understand procedures and instructions will greatly help make the changeover seamless.
One important tool is a cross-reference chart. It shows the current and new lubricants side by side and the machine compartment they should go into. To avoid confusion, it is preferable that the project manager goes through the chart with the relevant staff to ensure everyone understands.
This allows questions to be asked and addressed earlier rather than later. The cross-reference chart must also be accessible and clearly displayed in areas where lubricants are filled whenever practical.
The lubricant storage area and all dispensing and filling points must be clearly labelled with the new lubricant's name alongside the old lubricants that are being replaced. Once the transition is over, the old lubricant label should be totally removed from the plant. Maintenance documents, such as the service sheet, will need to be updated with new oils as old ones are discarded.
During the transition period, you will have to stock both old and new lubricants at the same time. All old lubricant packaging and containers need to be marked for depletion and stop order once finished. Here, ‘First In, First Out (FIFO)’ must strictly be in place. We do not want to find unopened or unused packaging of old oil in the plant midway through the transition when all the machines are already filled with the new oil.
Even worse, someone unintentionally re-orders the old lubricant when change is underway, thinking it is low in stock. This is a common mistake and can easily happen in your plant without the adequate training on proper lubricant replacement.
If you have an oil-analysis program in place, the laboratory needs to be informed of the change. Oil properties, additive composition, and concentration may be slightly different. This could cause a false alarm when the readings turn out differently from the old oil's reference.
For example, some engine oils use contains more magnesium concentration as a detergent than others. This can be mitigated by supplying the new oil sample to the lab for testing and recording the readings as a new reference.
When these three risks are managed properly, companies will find minimal disruption to their operations during a lubricant change. Although there may be teething problems, the long-term benefits of having better and improved lubricant quality, performance, and service far outweigh all the potential hurdles.
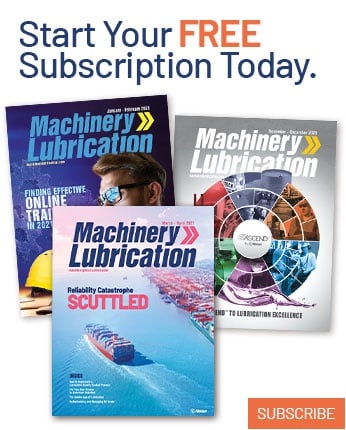