This edition of Oil Analysis 101 focuses on particle counting and related standards. Considered by many to be the single most important test for used oil analysis, whether you are conducting onsite particle counting, or relying on a commercial lab, there can be no doubt that a host of problems can be quickly and easily determined by monitoring the number and size-distribution of particles in an oil sample.
The importance of clean oil cannot be over emphasized. Particle count data is an invaluable part of any proactive condition-monitoring program, from ensuring that abrasive bearing wear is minimized, to determining if a hydraulic fluid is clean enough for reliable operation.
Particle counting was introduced during the 1970s as a result of the pioneering work on hydraulics and fluid power, conducted at Oklahoma State University by Dr. E. C. Fitch, father of Noria’s founder and president Jim Fitch, and coworkers. However, it has only been the last 10 to 15 years that industry, determined to work smarter, has started to fully realize the importance of fluid cleanliness.
The most common unit of reporting fluid cleanliness is the ISO Code System. This convention is covered under the ISO standard 4406:99. In this standard, the number of particles in three different size categories, >4 mm, >6 mm and >14 mm are determined in one milliliter of sample.* ISO 4406:99 states that the number of particles in each size category should be counted with the absolute count converted to an ISO code, using the ISO range code chart shown in Figure 1. Although the most common standard, ISO 4406:99, is not the only method by which the cleanliness of an oil sample can be reported. Others standards include NAS 1638 and MIL-STD 1246C, as well as outdated standards such as the SAE fluid cleanliness rating system. However, whichever method of reporting is selected, the first step is to count the number of particles in a volume of fluid.
There are three basic methods that can be used to determine the absolute number of particles in any given sample. These are outlined below:
Optical Microscopy (ISO 4407)
The original method for determining fluid cleanliness levels was to take a representative portion of the sample and examine it under an optical microscope. In this procedure, the particles are manually counted, which can then be used to determine the fluid cleanliness of the bulk sample. While this method may seem outdated, slow and cumbersome, it is still in use today and considered by many to be the most reliable and accurate method of particle counting, unaffected by some of the limitations of more modern, automated methods.
Automatic Optical Particle Counting (ISO 11500)
Perhaps the most widely deployed method today for determining fluid cleanliness is to use an automatic optical particle counter. There are a variety of instruments commercially available to optically count particles; from portable units for onsite use that cost as little as $15,000, to large, sophisticated lab-based instruments that may cost in excess of $40,000. There is even a low-cost, online optical particle counter available for under $1,000. However, all instruments, whether they be a hand-held unit or a full lab instrument use one of two methods, either a white light source, or more commonly today, a laser.
In a white light instrument, particles pass through the capillary detection zone and create a shadow on a photocell detector. The drop in voltage produced by the photocell is directly proportional to the size of the shadow and hence the size of the particle passing through.
In a laser-based instrument, due to the near-parallel nature of the laser beam, light scattering from the unimpeded laser beam is minimal because it is focused into a beam stop - until a particle passes through the instrument. As the laser strikes the particle, light scatters and hits the photocell. Just like a white light instrument, the change in voltage across the photocell is directly related to the size of the particle. In the laser-based instrument, one looks at an increased signal against what should be a zero background (in theory). Laser optical particle counters are generally considered to be slightly more accurate and sensitive than white light instruments.
There are several subtleties that must be considered with the automatic optical particle counters. First, for the most part, particles from used oil samples are not perfectly spherical. This can create problems for optical counters because with the one dimensional ISO 4406:99 coding scheme, how are particles counted that are 5 microns across the minor axis, but 40 microns across the major axis? To resolve this issue, developers of automatic optical particle counters have devised a compromise known as the equivalent spherical diameter (Figure 2).
![]() |
![]() |
Figure 2. The Spherical Diameter was Developed to Help Resolve Reporting Errors with Optical Particle Counters |
With the equivalent spherical diameter method, a particle is counted in the size-range under which the shadow, or scattering effect observed would have appeared, if the particle had been a perfect sphere. This allows the average fluid cleanliness to be estimated, permitting the ISO code to be trended over subsequent samples.
Another concern is the effect of false positives. For example, both air bubbles, and free and emulsified water appear as if they are a particle using the optical particle counting method. While the effect of air and water can be negated using an ultrasonic bath and vacuum de-gassing to remove air, and solvent extraction to dissolve free and emulsified water, other false positives are possible with multiple particle coincidences and additive floc. For this reason, care and attention to procedural details must be exercised when performing optical particle counts.
Pore Blockage Particle Counting (BS3406)
The pore blockage method is a widely used method of obtaining an automatic particle count. In this method, a volume of fluid is passed through a mesh screen with a clearly defined pore size, commonly 10 microns. There are two instrument-types that use this method.
One instrument measures the flow decay across the membrane as it becomes plugged while pressure is held constant, first with particles greater than 10 microns, and later by smaller particles as the larger particles plug the screen. The second measures the rise in differential pressure across the screen while the flow rate is held constant as it becomes plugged with particles. Both instruments are tied to a software algorithm, which turns the time-dependent flow decay or pressure rise into an ISO cleanliness rating according to ISO 4406:99.
While pore block particle counters do not suffer the same problems as optical particle counters with respect to false positive caused by air, water, dark fluid, etc., they do not have the same dynamic range as an optical particle counter, and because the particle size distribution is roughly estimated, are dependent on the accuracy of the algorithm to accurately report ISO fluid cleanliness codes according to ISO 4406:99. Nevertheless, they accurately report the aggregate concentration of particulates in the oil, and in certain situations, particularly dark fluids such as diesel engine oils and other heavily contaminated oils, pore block particle counting does offer advantages.
Why Particle Counting?
For many who are considering setting up their own onsite oil analysis program, the first question they ask is “What instrument should I purchase first?” While there are many fine onsite instruments available in the oil analysis marketplace, there can be little doubt that the ability to quantify an oil’s fluid cleanliness using particle counting is the most valuable tool in any proactive maintenance program.
So, whether you are looking for early signs of bearing wear, ensuring that a hydraulic fluid is good for service, or evaluating the performance of a filter in the field, particle counting offers a plethora of information for what is by comparison precious little money.
* The ISO code 4406 changed in 1999 to reflect changes in the calibration fluids used to calibrate particle count instruments. For more details on these changes, refer to “How the New ISO Particle Count Standard Will Affect You,” by Leonard Bench in the July-August 2000 issue of Practicing Oil Analysis magazine.
Particle Counters Offer a Multitude of Uses and Benefits
|
Tips to Ensure Accurate Particle Counting:
|
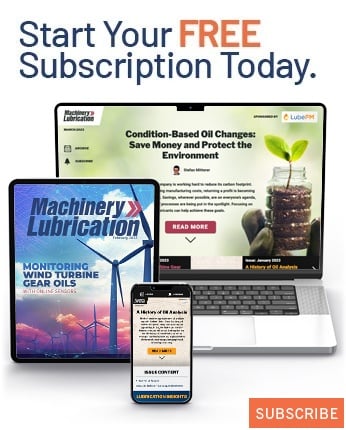