Many analytical techniques exist to characterize the uniqueness of lubricating oils for internal combustion engines and to confirm their compliance with specifications. Among the most frequently used characterizations are the base number (BN), viscosity grade, sulfated ash level and metals content. One of these, the base number, describes the level of reserve alkalinity of an oil. This alkalinity reserve is needed for the neutralization of acidic contaminants of the engine oil. Acidic contamination can come from various sources, and over time, the importance of these sources has shifted.
Historically, the level of contamination with inorganic acids derived from the combustion of high sulfur fuel and leaded gasoline has been important. More recently however, many governments have mandated the use of low sulfur fuel for diesel engines and unleaded fuel for gasoline engines. Modern engines operate at higher temperatures and with longer oil change intervals, leading to higher levels of oxidation, and consequently higher levels of organic acids.
A third important factor, which will play a major role for diesel engines, is the introduction of Exhaust Gas Recirculation (EGR), which enables the engine builders to lower the NOx emissions of their engines. The recirculated exhaust gas is cooled and fed back into the intake system of the engine. While cooling this exhaust gas, inorganic acids such as sulfuric and nitric acid can condense and contaminate the crankcase lubricant.
Various lubricating oil additives contribute to the alkalinity reserve. The most important source is the detergent, followed by dispersants and some antioxidants. The capability of these additives to neutralize acids differs depending on the acid strength. The most commonly used method to evaluate an oil’s capability to neutralize acids is to measure its BN. There are two commonly accepted measurement methods: ASTM D2896, often used for fresh oils, and ASTM D4739, which is often applied to measure the reserve alkalinity of used oils.
The two methods are similar in that they involve adding a measured amount of acid to the oil until all of the reserve alkalinity has been neutralized. The BN is calculated from the amount of acid required to completely neutralize the lubricant. The difference between the two methods comes in the choice of acid used, and solvent in which the oil is dissolved to run the test. D2896 uses a stronger acid than D4739 and a more polar solvent system. The combination of a stronger acid and a more polar solvent results in a more repeatable method that measures the presence of both strong and weaker base. For some lubricant additive types, D4739 does not measure all the base that is present. In general, D4739 gives a lower result because only the stronger basic species are titrated.
With the shifting balance of inorganic to organic acid contamination, it becomes more important to choose the proper tools for the evaluation of lubricants and to correctly interpret the results. In an attempt to demonstrate this issue, three detergent technologies have been compared in a bench test evaluation: A calcium phenate, a calcium sulfonate and a magnesium sulfonate. Three fully-formulated lubricants, identical in every way except for the detergent, were treated with a 5 acid number (AN) of oleic acid, a weak organic acid. In addition, the same amount of acid was added to base oil as a reference case.
As shown in Figure 1, the magnesium sulfonate did not reduce AN at all over the base oil case. The greatest reduction in AN was observed with calcium phenate, but calcium sulfonate also afforded a meaningful reduction in D664 AN. This difference would indicate that the magnesium sulfonate detergent does not completely neutralize a weak acid, thus preserving its BN while allowing the AN to increase and a corrosive environment to be created. Judging the quality of a used engine oil solely on its BN retentional in some cases may not be recommended.
Incomplete neutralization of acids will result in a more acidic environment in the engine. In this kind of environment, corrosion can occur. Corrosion may negatively impact the wear levels of all critical engine components such as journal bearings, piston rings, cylinder liners and valve train components. In general, the most sensitive components are the journal bearings, which are often made-up of a combination of metals including copper and lead. The oil’s capability to prevent journal bearings from corrosion is routinely evaluated in engine tests as part of the industry’s standardized qualification protocols. One of these engine tests, the Mack T-9 test, is part of the API CH-4 Specification for Heavy Duty Diesel Engine Oils. The Mack T-9, more than any other CH-4 engine test, has the character of an extended service interval test. During the 500 hours of testing, most BN is depleted. AN increases, in some cases causing a corresponding increase in lead - most likely from bearing corrosion.
Four test oils, listed in Table 1, were compared in this Mack T-9 test. The BN (D4739) curves of the intermediate oil samples, shown in Figure 2, indicate that the calcium-containing oils have a higher rate of BN depletion than the all-magnesium oil.
The end-of-test BN level of the all-calcium internal reference oil dropped to near zero; the low BN calcium/magnesium oil dropped to 1.2, whereas the all-magnesium oil dropped only to a level of 2.2. Comparing the BN curves with the lead concentration curves of the used oils, shown in Figure 3, two conclusions can be drawn:
Starting off with a sufficiently high base reserve does provide protection from bearing corrosion, and some detergent types provide bearing corrosion protection at lower BN levels than other detergents, evidenced by the reversal in ranking of the low BN all-magnesium and the calcium/magnesium oils.
This reversal in ranking can be explained from the AN and oxidation data, shown respectively in Figures 4 and 5. The all-magnesium oil shows a lead level increase starting around 300 hours while the BN is still at a level well above 4 mg KOH/g, but the AN started increasing early in the test. This again suggests that acidic species in the oil are not being completely neutralized by the magnesium-based detergent. The end-of-test oxidation levels appear to relate very well with the observed used oil lead contents, lending support to the idea that oil oxidation is the root cause of the observed bearing corrosion, creating organic acids that resulted in both BN depletion and AN increase as well as lead corrosion of the bearing material. This also argues in favor of using D2896 in used oil BN testing.
The observations discussed in the previous paragraphs demonstrate that it is important and necessary to use a lubricant with sufficient alkalinity reserve to neutralize acids. The most important source of acidic contaminants will remain the oxidation of the lubricant, because high-temperature operation is critical for the engine’s efficiency, the fuel sulfur levels continue to be lowered and hopefully engine builders will design their engines such that acid contamination as a result of the use of EGR is minimized.
Given the fact that a significant proportion of the acidic contaminants are the weaker organic acids, it can be concluded that a judgment of the used engine oil’s condition and suitability for extended service intervals should not be based on BN retention alone. In addition, the ability to control AN and oxidation must be evaluated because of the potential impact on bearing corrosion. Used oil condemning limits should, for the same reason, not be set based on just one used oil characteristic but on a combination of BN, AN increase, oxidation state and wear metal levels.
Editor’s Note:
There are two schools of thought about the validity of ASTM D2896, which employs perchloric acid as the reagent, versus ASTM D4739, which employs hydrochloric acid, a relatively weaker acid than perchloric acid, when applied to used oil analysis. One school suggests that the D2896 method is better because the strong acid neutralizes strong and weak alkaline components in the oil, providing a more realistic measurement of the true base number, while D4739 only measures the strong alkaline components. The other school suggests that the strong acid used in D2896 reacts with weak alkaline wear metals in the oil, producing a falsely exaggerated base number, which could lead to an overextend oil drain interval. D4739 measures only measures the additive package, which is there to neutralize acids, making it a more accurate test for used oil analysis.
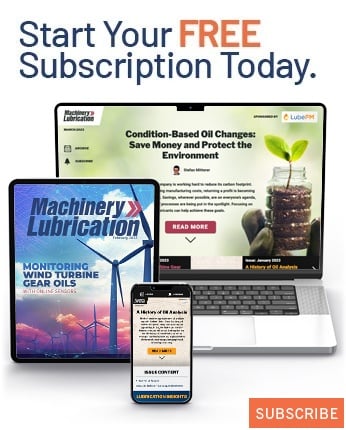