The author has supplied list of materials used to complete the stages outlined below. The bracketed numbers within the text correspond to the box “Cliff Smart’s Toolbox for TAN Titrations.”
Do you need a Total Acid Number (TAN) titration method that is simple, accurate and inexpensive? Years ago, I modified the ASTM D974 procedure in order to use a digital titrator [1] (Figure 1). I found the standard glass column burette to be inaccurate and frustrating to use. Face it - it’s difficult to hunch over the bench, conforming yourself to the apparatus, only to overshoot an endpoint because you let two drops fall instead of only one. The smallest increment the standard burette will release is about 0.05 ml when one carefully splits the drops in half.
On the other hand, the digital titrator will easily dispense 0.00125 ml per unit by simply rotating a stem with your fingertips. The difference in control afforded by the titrator radically improves the volumetric accuracy of the analysis. Attached to the front of the titrator is a 13 ml titrator syringe or cartridge [2], which I fill with a standardized 0.1 N alcoholic Potassium hydroxide (KOH) solution [3].
The refillable cartridge and “J” hook delivery tube [4] are airtight, even when in use, preventing evaporation of the isopropanol-based titrant solution. As far as expense, the titrator, empty cartridges and delivery tubes cost about $125. The titrator is very durable and carries a lifetime warranty.
The analysis begins by weighing a quantity of the lubricant into a 250 ml Erlenmeyer flask [5] on a balance [6], which provides 0.01 g sensitivity (Figure 2). For turbine lube oils weigh-out about 12 to 15 g of fluid. For dark or EP gear oils weigh-out about 0.5 g. Viscous, dark-colored oils, as a general rule, have a higher acid content than light-colored, low viscosity fluids.
Depending on their additives, they will require more titrant (weight for weight) to reach the desired titration endpoint. Attempting to titrate 5 g of an EP gear oil may expend half of a syringe of titrant and a lot of valuable time. Appropriate adjustments of the lubricant weight will minimize analysis wastes and improve efficiency. With these guidelines an analyst will use about 200 to 500 units (or 0.25 to 0.625 mls) of titrant per analysis. Contrast this with the inaccuracy of two to six drops from a glass burette.
Cliff Smart’s Toolbox for TAN Titrations
|
[1] Digital titrator, HACH 1690001
[2] Titrator syringe, HACH 1449501 [3] KOH titrant, Ricca 6257-16 [4] Delivery tube, HACH 1720500 [5] Glass flask, Kimble 26650 [6] Lab balance, Mettler PB3002DR [7] Toluene, VWR 48218-734 [8] Isopropanol, VWR 48218-704 [9] Graduated cylinder, VWR 65000-006 [10] Indicator, Mallinckrodt E12154 [11] Dropping bottle, HACH 23184-06 [12] Graduated dropper, HACH 23185-06
[13] Clamp and holder, VWR 21570-302 [14] Stand base, VWR 60110-222 [15] HCl titrant, Ricca 3800-16 [16] Calculator, Hewlett Packard 20S [17] Pocket balance, AccuLab PP-150 or V-333 [18] Polycarb flask, Nalgene 4108-0250 |
The oil is now diluted with a titration solvent. The solvent is a 50:50 mixture of Toluene [7] and Isopropyl alcohol [8]. I don’t recommend that you use the anhydrous Isopropanol as indicated by ASTM D-974. Instead, I use reagent-grade Isopropanol and omit the specified addition of distilled water. Why pay the higher price for water-less alcohol then add water? Also, to reduce analysis wastes and costs, I use only 50 ml of the titration solvent. Measure the solvent into a 100 ml, plastic, graduated cylinder [9].
Carefully pour the solvent down the inclined walls of the cylinder (and subsequent flask) to reduce acidifying the solution through the introduction of atmospheric carbon dioxide. Transfer the solvent into the inclined titration flask, rinsing-down any adhering oil droplets or streams. An indicator solution is prepared by dissolving 1 g of p-Naphtholbenzein [10] into 100 mls of the titrant solvent. Add one-half ml of indicator solution to the titration flask from a dropping bottle [11] with a graduated dropper [12]. Swirl the solution to mix in the indicator, avoiding agitation. This produces a solution with a bright orange starting color and a dark green/brown endpoint.
The analyst should now load the digital titrator with a KOH-filled syringe and purge any air from the syringe and J-tube. For convenience the titrator is supported with a 3-prong clamp and holder [13] on a stand base [14] (Figure 3). Zero the titrator counter dial, immerse the J-tube in the solvent and begin swirling the solution. Use of a white background behind the flask will aid in seeing the green/brown endpoint.
I have developed a “triple endpoint” technique whereby the titration is completed in three stages. At first, the titrant is added quickly until the endpoint is met - the first absence of orange. I remove the J-tube from the solution and add one drop from the titrator. I then weigh-out the next sample. During this delay, the solution again becomes bright orange. Now, I titrate to a second color change and add one drop.
I dilute the next sample, add indicator and swirl it. Finally, I slowly titrate the original sample to a green/brown (no orange) endpoint, read the counter dial and add slightly more titrant to verify no further color change. The color must persist for at least 15 seconds to be called the endpoint. I then record the value of the third endpoint, zero the counter and proceed with the next titration. Consistency will lead to very accurate, repeatable TAN determinations.
What about Total Base Numbers? Crankcase oils require the “alter ego” analysis of the TAN analysis - the TBN. Essentially, we start with a base solution and neutralize it with an acidic titrant. Motor oils contain alkaline (or base) additives to counteract acids from combustion gases, metal oxides and oxidation by-products.
The normal interaction of these acids with the lubricant expends the protective reserve alkalinity. By trending changes in the TBN, we can determine when the lubricant should be removed from service. The only change in the analysis method is to fill a standby digital titrator syringe with standardized 0.1 N alcoholic Hydrochloric acid (HCl) solution [15]. The green/brown-colored oil solution is neutralized with the acidic titrant to an orange-colored endpoint.
When the titration is complete, I use a programmable calculator [16] to determine either the TAN or TBN value (Figure 4). Both are reported as “milligrams of KOH per gram of oil”, per ASTM, in order to keep the acid number and base number scales in parity. Some labs use a chart that specifies a certain weight of oil, a delivered volume of titrant and a pre-calculated final result.
I prefer to calculate the result for whatever weight and volume was used in the analysis. This reduces analytical errors and analyst intervention. For the longest time I did the six-step calculation manually. Finally, I “discovered” programmable calculators, which are available for about $30 to $50. They are easy to program, efficient to use and prevent computational errors.
The greatest benefit of this titration method is that it is field portable (Figure 5). The sturdy digital titrator is designed to be handheld and effortlessly dispenses 0.00625 ml of titrant with a stroke of the thumb (Figure 6). That’s 1/160 of a milliliter with the titrator compared to 1/20 of a milliliter with a fragile glass burette. Samples can be accurately weighed to within 0.1 g with a portable, battery-powered, pocket balance [17] (Figure 7). This type of balance will cost about $150 to $250 depending on the capacity.
Polycarbonate flasks [18] prevent reaction vessel breakage in the field while allowing visibility for endpoint colors. After the analysis, the screw cap flasks contain the solvent waste for disposal at a later time. Use of a programmable calculator will again greatly reduce errors and fatigue (Figure 8). An analyst or an operator can accurately and quickly evaluate the acid content of a lubricant while in the plant.
There you have it - a simple, very accurate and inexpensive means of obtaining Total Acid Number values in the lab or in the plant. Coupled with a falling ball viscometer and a wear particle patch test, a sharp analyst could accurately evaluate lubricant and equipment conditions anywhere, anytime.
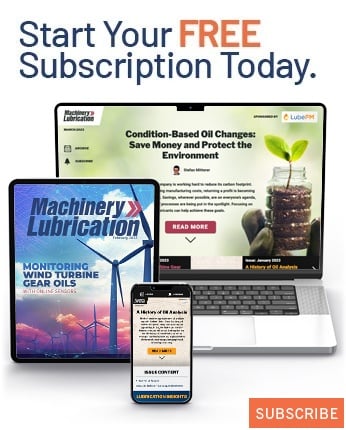