Is the cost of oil analysis really justified? Perhaps you’ve heard another rhetorical question. How long is a piece of string? The answer to both questions is the same - it depends. Oil analysis is justified only when the answers to specific questions about the oil and machine have sufficient value to offset the cost.
Unfortunately, some users are unaware of the many questions that oil analysis can answer and as a result they gain only a fraction of the potential benefit from their oil analysis program.

Therefore before you design your oil analysis program, before you select a laboratory and before you develop test slates, create a list of value-generating questions that you want answered. Basically you want to reverse engineer your oil analysis program.
You start with a list of the ideal oil analysis deliverables (answers to your important questions) and work backward. The list below is designed to help you develop your question set:
Questions Relating to Lubricant Quality and Type:
-
Has the appropriate lubricant been specified for this application and machine?
-
Is the specified lubricant currently being used?
-
What is the condition and quality of new lubricant deliveries?
-
Have two incompatible greases or lubricants been mixed?
Questions Relating to In-service Lubricant Health/Condition:
-
Have any vital additives become depleted and if so how much?
-
Has the basestock been impaired by thermal degradation, oxidation or hydrolysis?
-
Has interfacial tension changed, affecting foaming, air release and demulsibility properties?
-
Has the oil’s viscosity changed due to evaporation, shear, radiation, contamination or various chemical reactions?
-
What is the residual life of the lubricant?
-
Is a lubricant in a storage container fit for service?
Questions Relating to Lubricant Contamination:
-
Has the lubricant been mixed with other fluids or lubricants?
-
Has the lubricant become contaminated with soot, dirt, fuel, water, process chemicals or coolant?
-
Has the lubricant been damaged by radiological contamination? Is it a hot (radioactive) sample?
Questions Relating to Abnormal Machine Wear:
-
Is there incipient evidence of abnormal wear?
-
Which component or machine surface is generating the wear?
-
What is the tribological cause of the wear?
-
Does the oil contain evidence of abnormal operational or mechanical wear conditions such as misalignment or overloading?
-
How severe or threatening is the wear?
Questions Relating to Miscellaneous Failure Root Cause:
-
Is the oil prone to laying down surface deposits, varnish and sludge?
-
Is the oil highly acidic with suspended corrosion agents?
-
Has there been sabotage or criminal activity associated with the machine that could affect its condition and lubricants?
-
Does a new machine have manufacturing defects?
Questions Regarding Maintenance and Operations:
-
Does a filter need to be changed or is there need to service a separator?
-
Is there either internal or external leakage?
-
Has a machine been properly repaired or rebuilt?
-
Has a machine been properly commissioned?
-
Is there a need to perform certain internal inspections during a shutdown period?
-
Has a bearing been over/under greased?
-
Is there evidence of abnormal operating temperatures, pressures, or duty cycle?
-
Is it time to decommission a machine?
In it simplest and most basic form, oil analysis is performed to improve the quality of machine and lubrication maintenance decisions. When well designed and implemented, many of the questions listed above can be answered without excessive expense or complexity.
One approach is to rank each question according to importance as A, B or C, with A questions being the most important. This is similar to a Pareto chart or criticality analysis (e.g., failure modes and effects analysis).
Once your questions are ranked by machine type, you should develop an oil analysis test slate (both routine and exception tests) that emphasizes A and B questions, in other words, those tests that can provide high-confidence answers to these questions.
Next consider where the samples will be pulled to maximize the data strength (signal-to-noise ratio) and minimize data disturbance. Consider both primary and secondary sample points where appropriate.
Also, develop a sample frequency strategy that considers both onsite and off-site laboratory analysis. The only remaining step is to baseline your lubricants and assign alarms and limits to all test parameters.
It is much easier to justify the cost of oil analysis when you have an optimum list of value-generating questions that you want answered.
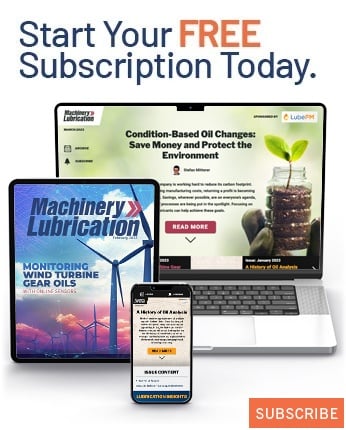