Butler Machinery Company, located in Bismark, N.D., is the Caterpillar Dealer serving North Dakota (excluding 5 northwest territories), South Dakota and Clay County Minnesota. Our client base consists mostly of mining, trucking and agriculture. Caterpillar has approximately 145 labs worldwide testing 6.5 million samples a year; 65,000 of those are tested at Butler. We provide oil analysis (through our S·O·SSM program), help customers optimize oil change intervals, monitor repairs and validate maintenance practices.
Our S·O·S program (which originally stood for Scheduled Oil Sampling) is structured around a series of tests: elemental or wear analysis, oil condition analysis, oil cleanliness and liquid contamination. The first three are instrumental analyses and are performed on the ICP spectrometer, FTIR spectrometer, Viscometer, Particle Counter and PQ Wear Density Meter (Table 1). The liquid contaminant tests (sometimes called physical tests) are performed using wet-chemistry and simple temperature-separation techniques.
Table 1 - Butler’s Tests Performed for Wear Analysis, Oil Condition Analysis and Oil Cleanliness |
The ICP (inductive coupled plasma electron emission spectrometer) is used to measure wear metals, contaminants and in some cases additive elements. The sample is heated in hot plasma where the electrons of the different elements are boosted to higher energy levels. When the electrons lose energy or return to their ground state, they give off light. This light, which is emitted at specific wavelengths, is then captured and measured by special detectors. By knowing the frequency and intensity of the light we can tell which elements are present and in what amount. In our lab we currently run 11 elements but plan to expand to 21 or more in the near future. We run 11 elements because we focus on the elements that provide the most information about wear, contamination and mechanical problems. Some labs run many additive elements but this can, on occasion, be misleading. As an example, many additives, such as the zinc-containing antiwear additive ZDDP, degrade to form inactive organo-metallic species and salts. The ICP measures the metal (zinc for instance), but does not differentiate between the active and inactive forms.
The particle count instrument measures all particles in the oil from 5 to over 100 microns. It does not tell what kind of particles are present, only the size and number. This test, sometimes referred to as oil cleanliness testing, is performed on all non-engine samples and is one of our standard tests. The PQ ferrous debris monitor is an instrument that measures the amount of magnetic metal (iron and nickel) present in the oil. Although this test is most commonly used for gear compartments we find that it is extremely valuable for engines because it detects the large iron particles missed by the ICP. We perform this test without additional charge on all samples and are one of the few labs in North America that provides this test. Kinematic viscosity is a test of the oil’s thickness or resistance to flow. This test provides information about the condition of the oil and whether fuel or other contaminants are present. It also tells if oil of the correct viscosity is being used. Because viscosity is temperature dependent we maintain the temperature of our viscometer bath to within 1/100 of a degree. FTIR (Fourier Transformed Infrared Spectroscopy) is a test that provides information about the oils’ condition and presence of contaminants (water, fuel and antifreeze). We measure soot, oxidation, nitration and sulfur levels with this test. We also screen for water, fuel and antifreeze. The main limitation is that a sample of new oil from each customer must be on file and it must closely match the used oil. If the reference oil is different, the accuracy is affected. This happens frequently when different brands of oil are added or mixed, or when the oil company changes formulations. This test is performed on all engine samples and selected transmission samples.
The microscope exam is performed when the other tests (particle count or PQ) indicate a problem is likely. We are able to identify many of the particles and can get information about the wear processes that are occurring. This test provides some of the information available with ferrography, but it is much less The antifreeze contamination test is a chemical test. A small amount of oil is combined with an acid and an oxidizer. After a few minutes a color indicator or dye is then added. If antifreeze is present the solution turns purple. This test is not specific to ethylene glycol and therefore a color change may result from non-harmful glycols used in the oil formulation, and from other chemicals. The test for water is a simple temperature separation. A drop of oil is placed on a hot plate and heated to 350°F. Since water boils at a much lower temperature than oil it forms bubbles if it is present. We can estimate the amount of water in a sample by comparing the bubbling action to known water-containing standards. Diesel fuel dilution is detected by a combination of viscosity testing and flash testing. We look for a decrease in viscosity and then perform a Seta-flash test. This test is frequently inconclusive because of the differences in the boiling point of different oils and fuels. The viscometer provides much more usable information. |
The primary goal of a Caterpillar Dealer Lab is to provide product support. By providing oil analysis we help our customers get the lowest operating cost. This results in a win-win situation for both the customer and the dealer because happy customers buy more of our products, and one of our major goals is to sell machines.
At Butler, we process samples for all brands of engines/machines, but since we are a Caterpillar Dealer, our area of expertise is with Caterpillar products. Some may argue that it is not in our best interest to help owners of competitive machines. However, in many cases these customers also own Cat machines. We want them to be successful in their business so they can continue to do business with us. For those that do not own Cat machines, Butler has the opportunity to demonstrate our superior product support capabilities. Hopefully we’ll gain these users as future engine or equipment customers.
Caterpillar maintains a large database that contains data on an extensive line of equipment. This was established to help Caterpillar service customers better. The database allows dealers and labs to provide repair options based on files from engineers. Cat also has a 150 member Internet e-Group to share information instantly with other Caterpillar Dealer Labs around the world. The e-Group is like having on-line consultants available at the click of a button. We can immediately share and compare results, and trends with the other Cat labs.
When shopping for oil analysis the qualifications of the interpreter should be considered. At Butler, our analyst is a degreed chemist. It is also important that he or she have training or experience with engines and equipment, and that they have access to engineering and technical data.
Another factor to consider is turnaround time. Turnaround time is very important because problems such as internal coolant leaks and fuel dilution must be caught early to save money.
From the time the sample arrives at the lab, the results should be available within 24 hours. In our case, the results are available 6-8 hours after they arrive at the lab. The reports are sent electronically via e-mail to the customer as an acrobat file. Anything delivered by shuttle truck is available within 24 hours. We have even performed emergency testing on samples over the weekend.
Price is sometimes used to compare oil analysis services; however, you cannot always judge the quality of an oil analysis service by the price. Our price is comparatively low because we focus on product support (not on oil or oil sample sales), yet we provide tests that others do not. We have one price that includes all the essential tests. This is a cost effective combination that provides maximum information at minimum cost.
The importance of providing complete and accurate information when submitting samples can’t be overstated. It is key to the results produced by the testing. The only information labs have about your sample is the information you put on the bottle label. Below are examples of information that should be on the bottle label:
How many hours the oil was used (because a low-hour sample with high readings is more serious than a high-hour sample with high readings).
Brand and viscosity of the oil (so the correct reference oil for the FTIR test is used and to discover if the oil is thicker or thinner than it should be).
The serial number of the machine being sampled. (The serial number is used to identify the machine and to maintain a machine’s history so changes in wear can be easily trended. Be sure to inform the lab of specific problems to look for.)
For example, we received an engine sample with high lead and tin readings. We did a quick literature search on the Caterpillar system and found there was a possible problem with the bonding of the lead/tin overlay on a group of rod bearings manufactured on a certain date. Knowing the affected serial number range and manufacturing date we where able to determine that the engine being sampled was one that could be affected by this problem.
Our service people removed the oil pan and inspected the rod bearings. Sure enough, there was one bearing that had started flaking. With access to the Caterpillar system information we were able to pinpoint the problem and take corrective action early. Our service people knew exactly where to look for the problem and it was caught before any damage was done.
Finally, the important thing to remember about oil analysis is that you’re purchasing information. Oil analysis is very similar to medicine. At the end of the day, you want the best information available, not just the test results. In the case of disease, the doctor interprets the medical test results and provides information on treatment options. Our S·O·S lab does the same thing. We provide information about the problem and then help you decide the best course of action.
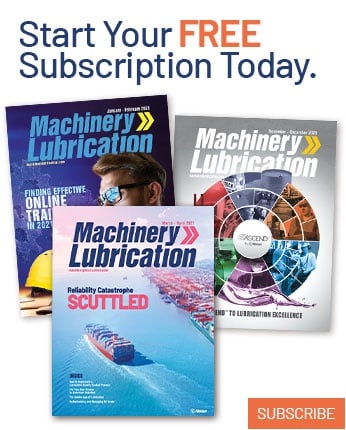