By now, most of us are aware of the need to manage contamination in our lubricated machinery.
Unfortunately, many who have identified the need for cleaner oil and developed appropriate cleanliness specifications for the equipment still have trouble meeting the targets, making costly contaminant removal tactics necessary.
There are many sources of solid particle contamination including new oil additions, built-in contamination, machineborne particles and the ambient air that enters when the machine breathes.
When it comes to ingested dirt, it stands to reason that much of it comes from the immediate surroundings including the surface of the machines. By the same token, a significant portion of this ingression can be controlled by simply keeping the machines clean on the outside.
In addition to controlling particle contamination in the oil, surface cleanliness also plays a large role in controlling heat contamination.
A large percentage of rotating equipment is air-cooled, and therefore, is sensitive to fouling of the surface area. Unfortunately, a thin layer of dirt on top of an air-cooled component can cause a dramatic drop in heat transfer.
The way I see it, cleanliness starts with a clean operating environment. Of course, this can be a tall order in many industries due to process materials and ambient conditions.
However, most of us could and should do a better job. When I look at machinery, I am often startled by the lack of cleanliness on the outside. General housekeeping and machine cleanliness are commonly overlooked components of a contamination control program.
After all, the dirt that gets in the machines has to come from somewhere. It stands to reason that the dirt on the exterior of the machines or on the oil transfer containers will eventually end up in the oil.
While it may be impractical to remove contaminants from the ambient air, we can certainly address the pounds of dirt and grime that are on and around the machines.
The development and implementation of a meticulous housekeeping policy, from storage facilities to production areas, can go a long way toward improving oil cleanliness and machinery reliability. It’s time we started cleaning up our messes and demand excellence in this important, yet often overlooked issue.
Housekeeping is a Minimum Requirement
When developing a housekeeping strategy, the obvious first step is to remediate the immediate problem. If the machines and the work or process areas are dirty, clean them.
While this can certainly be a daunting or seemingly impossible task, it’s really not. I’ve witnessed multiple examples of similar equipment in similar service that are virtually at opposite ends of the cleanliness spectrum.
This process, like many endeavors, may be best handled by tackling one area at a time. Justifications such as “it has always been this way” or “it was like this when I got here” are often true; however, they don’t change the necessity for action.
Once the areas have been cleaned up, they must be maintained. Without some degree of diligence, it would be quite easy for things to quickly return to their previous level of cleanliness.
For some, this task is as simple as everyone cleaning up after themselves, wiping down machines after an oil change or cleaning up spills, for example. For others, it may require design changes to the equipment or process areas. The use of items such as passive shields or guards can protect machinery from process material which may continuously fall from above.
I was once asked to examine and determine the cause of failure for a set of bearings in a cement mill. When I examined the bearings in service, a shovel was required to gain access. The components were literally covered with extremely abrasive dust which continually rained down from overhead equipment.
A well-placed shield would deflect the falling material and routine cleanup of the area would likely curtail the prevalent particle-induced failures.
There are other measures that should be taken to maintain machine cleanliness. Painting machines and resurfacing floors on a routine basis is another good way to support maintainability.
Keeping machine surfaces and piping in good order will also allow for prompt and accurate leak detection. It can be difficult to locate a leak if everything is coated with oil and grime. Leak remediation is another component of machine cleanliness. We all know that oily surfaces collect dirt more quickly and are more difficult to clean than dry ones.
Oil leaks also pose a serious safety hazard. Even a minor injury like a twisted ankle due to a slip on an oily floor can be quite costly. According to OSHA, the No. 1 category of industrial accidents is slips, trips and falls. Additionally, the No. 1 overlooked factor in these accidents is general housekeeping.
Preventing or repairing oil leaks and keeping a tidy workplace can go a long way toward preventing these kinds of accidents. A clean and well-ordered plant environment also creates a more psychologically healthy workplace, which itself can boost morale and productivity.
When it comes to achieving and maintaining machine and overall plant cleanliness, the most difficult part is getting started. Once a workable plan and schedule are developed, the dirty, grimy, depressing plant of yesterday will become a more safe, reliable and productive facility.
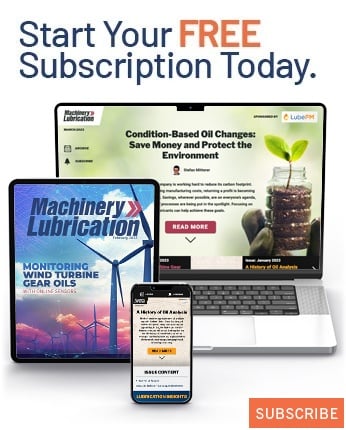