Rule No. 1: Don’t mix incompatible lubricants.
Rule No. 2: When in doubt, assume that two lubricants, when mixed, will be incompatible and will exhibit adverse side effects.
Many think the question of lubricant compatibility is a trivial matter, and therefore have not given it serious thought. Sadly, I could fill every page in this issue of this website with recent case histories that underscore the importance of the two rules mentioned above.
And to make matters worse, many modern lubricant formulations, using premium base oils and additives, have new risk factors related to lubricant cross-contamination.
As a practical matter, lubricants of questionable compatibility will be mixed in various binary concentrations from time to time. This occurs for a variety of reasons, such as the following:
-
Lubricant consolidation practices have been implemented to reduce the number of lubricants in use.
-
Past lubricant supply agreements are not renewed, resulting in a change in vendors.
-
A change in machine application or reliability requirements triggers the need to switch to a lubricant with enhanced performance or modified properties.
-
New or rebuilt machines are shipped with internal surfaces wet with an unknown type of lubricant or corrosion preservative.
-
Accidental mixing of lubricants caused by untrained personnel or packaging/ labeling error.
-
The practical inability to drain out all remnants of a previous incompatible lubricant when switching lubricant types.
-
Bad advice regarding compatibility offered by lubricant suppliers or unwise use of generic cross-reference guidelines.
Even world-class maintenance organizations face lubricant incompatibility issues occasionally. Once the threat has been recognized, damage control and remediation may be the only practical alternative.
This should begin with vigilant monitoring and inspection, looking for symptoms of incompatibility, side effects and/or impaired performance. This is where oil analysis can play a vital role to enunciate a condition that spells trouble.
Before we begin our list of symptoms, let’s briefly list the general classifications of lubricant incompatibility:
-
Mixtures of some base oils can reject additive solubility.
-
Base oils can chemically react or reject other base oils.
-
Base oils can react with foreign additives, forming transformation products.
-
Additives can clash, forming insoluble reaction products.
-
Additives can neutralize, dominate or alter the performance of other additives.
Note, this column addresses only incompatible lubricating oil mixtures. Not discussed is the potential of a lubricant’s incompatibility with the machine, process chemicals or operating environment.
Grease thickener incompatibility is also not addressed, but has been covered many times in Noria publications. Also left out are the many risks associated with using unapproved additive supplements.
The Signs of Trouble
Let’s begin by recalling the functions of a lubricating oil. These include friction control, wear control, heat control, corrosion control and contamination control. In any given application and type of lubricant, this list can be refined and expanded.
If a lubricant is properly selected for a target application, it should perform these functions properly over the intended service life. However when lubricants become mixed, performance can change and in certain cases, sharply alter machine health.
It is worth mentioning that there are degrees of incompatibility. This ranges from harsh rejections leading to catastrophic machine failure to a change barely noticeable in a single lubricant’s performance parameter.
After all, lubricants routinely face unforgiving machine environments that compromise performance in ways that far exceed a mild shift in lubricant oxidation stability or air-handling ability, for instance.
The following are examples of potential symptoms of lubricant incompatibility:
Impaired Film Strength
Increase in wear metal production, heat generation, vibration or acoustic emission.
Water Demulsibility
Emulsions may begin to form where previously water would shed (settle) rapidly.
Color Change
Some changes in lubricant color and opacity are normal as a lubricant is exposed to operating temperature and the service environment. In other cases, a pronounced and unusual change in color or turbidity may be a telltale sign of incompatibility from cross-contamination.
Air-handling Ability
Impaired air release and foam suppression is a potential symptom of incompatibility.
Soft Insolubles
Additive floc, additive drop-out, varnish, sludge, deposits, bathtub rings, premature filter plugging and bottom sediment are possible side effects of clashing additives and/or base oils.
Premature Base Oil Oxidation
There are many symptoms of oxidation, including a sudden increase in acid number and viscosity excursions combined with sludge and a rancid odor.
Sudden High Particle Count
An unexplainable increase in particle count may be additive precipitation or other insolubles resulting from additive and/or base oil interactions.
Phase Separations
Sight glasses and oil samples may exhibit separation of fluid phases, color, consistency and/or refractive indices (for example, streamers).
Gelation
Some lubrication mixtures can cause thick gels to form on filters, reservoirs and sight glasses. This can lead to lubricant starvation and even a drop in oil pressure.
Leakage
Leakage from several points in the system may be associated with viscosity change and/or interfacial tension change, both possibilities caused by lubricant mixing.
No Home Brews
Consider this: It can take years of testing and experimentation for lubrication for
mulators to select the perfect blend of antioxidants to optimize oxidation stability in the target application without risking additive drop-out or altering other properties. Some turbine oils may have as many as five antioxidants in balanced concentrations.
The mixing of lubricants is the equivalent of creating an entirely new recipe from scratch. Professional lubricant brew masters who do this for a living know the complexity of the task and the inherent risks of casual home blends.
Before mixing lubricants, get professional advice. Remember Rule No. 2. While some types of lubricants are already tested and qualified for mixing between brands (motor oils for instance), most are not. Perhaps in the future all lubricants will have a Compatibility Class assignment which will be noticeably visible on spec sheets and packaging labels.
Those lubricants with the same class assignment (A2A for instance) will be prequalified for low-risk mixability. Mixing between class assignments would be prohibited without advance testing.
As a final note of caution, the quality of many lubricants is backed by a supplier warranty, often covering the repair of damaged equipment in the event of a formulation defect. In the case of unapproved mixing of two different lubricants, neither warranty would apply. As one lubricant supplier told me, “When this happens, all bets are off!”
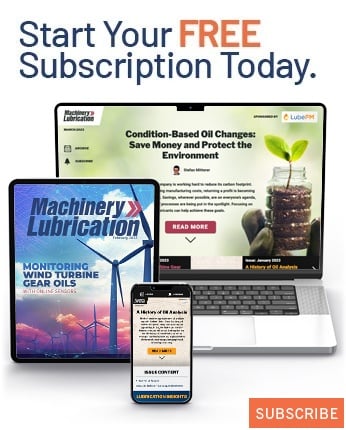