As consumers and manufacturers of all kinds of products, we are often asked to sort out the claims and counterclaims of advertisers and marketers. That’s understandable and will continue in any competitive society. Being informed and focused, and always aiming to “compare apples with apples” is both beneficial and appropriate.
A good example of the “apples to apples” axiom is the European technical publication wherein an engineer from the United Kingdom reported on the adverse effects of moisture intrusion on bearing life. He made a reasonable point that users must guard against lube contamination and that bearing protector seals incorporating the rotating labyrinth principle make economic sense.
Here’s a way to quantify bearing life with and without a contaminated lubricant.
How Bad is Contamination?
Major bearing manufacturers have published authoritative texts on the effects of lubricant contamination. Using illustrations such as Figure 1, plotting the ratio of the lubricant’s operating viscosity over its rated lubricant viscosity (v/v1) and displaying it on the abscissa against a life adjustment factor a displayed on the ordinate, it is possible to understand the importance of lubricant contamination.
In Figure 1, Region I is applicable only to situations with utmost cleanliness in the lubrication gap and moderate bearing loading, which are rather unrealistic for process pumps. Region II indicates a high degree of cleanliness has been achieved, which is possible with modern bearing protector seals (Figure 2). Finally, Region III might be typical for bearing environments exposed to an industrial environment, such as bearing housings without effective protector seals.
Figure 1. Contamination Adjustment Factor a vs. Viscosity Ratio
Using Figure 1 and assuming v/v1=1, we might obtain a= 0.3 in Region III and a= 1 in Region II. Therefore, using effective bearing protector seals would have improved bearing life by a factor of 3. This presents powerful analytical evidence in support of industry trends toward better bearing housing protection.
Figure 2. Lip Seal (Top Portion) and
Modern Rotating Labyrinth Seal (Lower Portion)
Lip Seals vs. Rotating Labyrinth Seals
Bearing protector seals are not a novel idea and users of API-compliant pumps have seen stationary and rotating labyrinth bearing protector seals for decades. New styles of bearing protector seals have been described in technical journals dealing with lubrication and sealing issues; thus, the article by the UK engineer was appropriate. What’s of interest is that after printing the engineer’s article, the editor of a European publication commented that lip seals seem to be permanently denigrated when they are not used in an optimum configuration.
The automotive industry uses cartridge arrangements (cassettes) to what appears to be good effect. They are widely used on trucks and buses, which now often have a half million-mile warranty. This must be in excess of 10,000 hours, so it would be potentially adequate for many intermediate duty pumps, according to the (European) editor.
But was a lubricant contamination issue involved? Was the editor correct in concluding that lip seals are potentially adequate for many intermediate pumps?
The rolling element bearings of literally billions of electric motors and hundreds of millions of automobiles, pumps and other industrial machines are protected against lubricant loss and contamination by lip seals. Lip seals have served industry for more than a century in applications where the elastomeric component received ample lubrication with moderate shaft surface velocities. This perhaps, is the summarized answer to the first question. It addresses the issue regarding the adequacy of lip seals for centrifugal pumps and the fact that lip seals are not deemed satisfactory for API-compliant pumps.
There are, however, relevant differences between automotive applications and process pumps in modern industry. Although a 70 mm (2.75 inch) automobile drive shaft operating at a maximum speed of 2,000 rpm (7,327 mm/s or 288.5 inches per second (ips)) represents a rather strenuous application for a motor vehicle, it is far from the 12,250 mm/s, or 482 ips rubbing velocity of a 65 mm (~2.56 inch), 3,600 rpm shaft in a centrifugal pump.
It is universally accepted that rubbing wear increases as the cube of the velocity ratio. Therefore, if a well-designed lip seal in an automobile has a life of 1,000,000 miles at 50 mph, this would equate to 20,000 operating hours on a set of lip seals.
On the industrial equipment example and at a surface velocity 1.67 times greater, the wear life would be diminished by the exponent 3, resulting in a factor of about 5. In this case, lip seals would last 4,000 hours – less than half a year of continuous operation and not good enough. Interestingly, the 80 percent failure rate given for lip seals after 2,800 hours of operation at testing conditions mandated by applicable United States military specifications seems agreeable with this calculation.1
Sealing Choices
Based on industrial experience, it is reasonable to assume two different scenarios for the bearing housing seals illustrated in Figure 2. A lip seal is shown on the upper portion of the shaft; Let’s assume it costs $5. The lower portion shows a modern rotating labyrinth seal and is priced at $100.
Scenario 1
To avoid shaft fretting, moisture intrusion and premature bearing failure (assuming labor and materials to remedy a bearing failure cost $6,000), we replace a $5 lip seal twice a year (Table 1).
Table 1. Lip Seals
Alternatively, a $100 modern dynamic O-ring rotating labyrinth seal can be replaced after two years of operation (Table 2).
Table 2. Labyrinth Seals
Labor: $250/year; material: $50/year; total per year: $300. In this comparison, modern rotating labyrinth seals are clearly favored.
Scenario 2
Run to failure. The labyrinth seal degrades and the bearing fails after two years. Although no production outage time is assumed, the repair costs the plant $6,000, ($3,000 per year) which is unacceptable.
Energy Issues
As long as a lip seal is operationally effective and has not degraded to the point of shaft wear or elastomer lip wear, it is reasonable to assume that 160 watts of frictional energy are consumed by an average seal. At $0.10/kWh, that equates to $140 per year.
Some sources assume the cost of proper waste oil disposal per gallon is equal to that of the new oil. Therefore, if in that instance and in Scenario 1, precautionary lube oil replacements (oil changes) were performed and a lube oil and disposal charge were factored in, the picture would further shift in favor of modern dynamic O-ring rotating labyrinth seals.
Reliability-focused Pump Users
While most people will agree that lip seals have their place in disposable appliances and machines which, for unspecified reasons, must frequently be dismantled, engineers should always look at the full picture. While in no way claiming that all lip seal applications are past their prime, new alternatives are available for the reliability-focused and energy-conscious user community.
Unfortunately, lip seals rarely measure up to the expectation of the majority of intermediate duty pump users. The fact that lip seals are available in cassette configurations makes no difference. Your pumps deserve better.
References:
-
Heinz P. Bloch and A. Budris. Pump User’s Handbook: Life Extension. 2nd edition. Fairmont Publishing Company, Lilburn, Georgia, page 121, 2006.
-
FAG Bearings. Ball and Roller Bearings. Schweinfurt, Germany.
-
AESSEAL plc. Rotherham, United Kingdom and Knoxville, Tennessee.
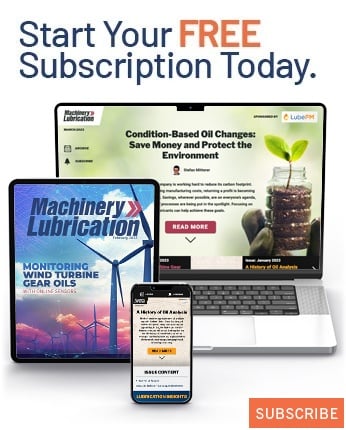