If you've ever gone whitewater rafting on a Class III or IV rapid, you know what turbulence is. A few years ago while rafting with some friends on the Ottawa River, our raft tipped over coming off of a class IV chute and the entire crew went under. Class IV runs have high, irregular waves, breakers, powerful back eddies, whirlpools and sharp bends. Obviously helmets, personal floatation vests and some skill are required when negotiating rapids such as these. Let's face it - whitewater rafting is thrilling, exciting, exhilarating and fun. But nothing matches the heart-stopping jolt of adrenalin you get when you're flung from a raft shooting over a waterfall and then manage to climb back into the raft to run the rest of the river without even a bump or bruise.
Jason (second from left) and His Crew
Unfortunately, most of us don't always get the same thrill from oil analysis, but there are a few similarities between whitewater rafting and oil sampling.
The subject of fluids in motion is refered to as hydrodynamics and has intrigued scientists for years. Hydrodynamics continues to be explored and can be applied to oil analysis and specifically, oil sampling. To understand hydrodynamics and how it applies to oil sampling, the specific components of related hydrodynamics need to be identified.
Hydrodynamics 101
-
Reynolds number - This is a dimensionless ratio of fluid flow used to determine the transition point from laminar to turbulent flow.
-
Laminar flow - The word laminar means "in layers" and describes a smooth fluid flow. Fluids are made up of particle layers that slide by each other and follow a smooth, somewhat consistent path.
-
Turbulent flow - Described as erratic fluid flow, it often changes directions, characterized by small, whirlpool-like currents called eddy currents.
So why, when discussing oil sampling, do discussions about fluid flow and hydrodynamics need to be included?
Practitioners in the oil analysis industry have determined that collecting a sample that maximizes data density and minimizes data disturbance is at the top of the to-do list when selecting an appropriate oil sampling location. The appropriate area is typically located in a turbulent zone. Usually, the turbulent fluid flow can be found in an area where the fluid changes direction at high velocity. This creates a high Reynolds number.
Laminar vs. Turbulent
Turbulent flow is ideal for oil sampling because the fluid in this area is turning over itself, which provides a homogenous mix for particles of all shapes and sizes to be evenly distributed in the sample. Laminar flow, on the other hand, is quite different. Laminar means "in layers." The importance of these layers is the reason sampling in laminar areas is not recommended.
A 1964 study titled "Design and Testing of an Isokinetic Sampling Probe for Sampling Fluid Contaminant in Laminar Flow" by Dean A. Horinek at Oklahoma State University concluded that: "For laminar flow, larger particles tend to flow in the boundary layer of the system, and the small particles tend to flow toward the center of the velocity profile."
Therefore, the distribution of particles in laminar flow is influenced by the size and weight of the particle itself. Sampling in laminar locations will not provide an accurate distribution of contaminants for analysis. We should be aware that even though we sample in turbulent areas, we also need to address isokinetics in our sampling method.
Isokinetic oil sampling refers to sampling in such a way that the linear velocity through the opening of a sample probe is equal to the linear velocity in the pipeline at the sampling location and is in the same direction as the bulk of the liquid approaching the sampling probe. What this means is that if we insert a fixed sample tube perpendicular to the fluid flow in a pipeline, the end of the sample tube must be bent at 90 degrees into the fluid flow which eliminates flaws in accuracy as a result of reduced fluid velocity at the sample tube opening.
So why is the distribution of particles so important? Why is there such concern with the accuracy of particle counting when it is knowingly traded off when testing for other properties in lube oil such as spectrometric measurements of iron or copper where measurements can be as low as seven to 21 percent of actual values for large, free metal particles? Can the health of our systems not be understood when observing rate-of-change trends?
In a past editorial column Jim Fitch addressed this as one of the "Fallacies in Sampling."1 He described an e-mail he received from a colleague asking about sampling location and why it was important. Because the data is trended, "once a baseline is established and samples are taken consistently, problems will be revealed in trend-line movement (change in direction, rate of change, etc.)."
As Jim explains, this issue goes deeper than simply executing consistent procedures when sampling.
"The fallacy with this doctrine is that it ensures only repeatability, not data quality or accuracy. This is illustrated in Figure 1. The target on the left shows how reliable sampling and analyses can be well off the mark ... and consistently so."
Figure 1. Repeatability vs. Accuracy
To understand the health of a system when sampling oil for analysis, it is important to obtain data that is not only consistent and repeatable, but accurate as well. The real focus should be selecting a sampling location that can provide turbulent fluid flow for accurate, repeatable and data-rich samples.
So the next time you are tasked with selecting appropriate locations for oil sampling, just picture yourself whitewater rafting!
References
1. Jim Fitch. "Fallacies in Sampling." Practicing Oil Analysis magazine, January 2002.
2. Personal communication
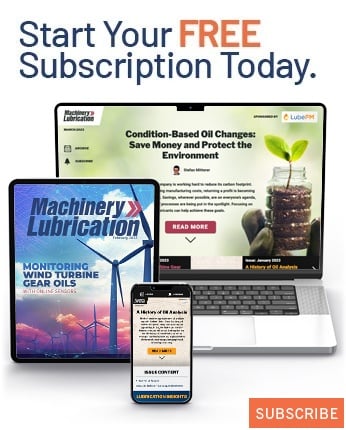