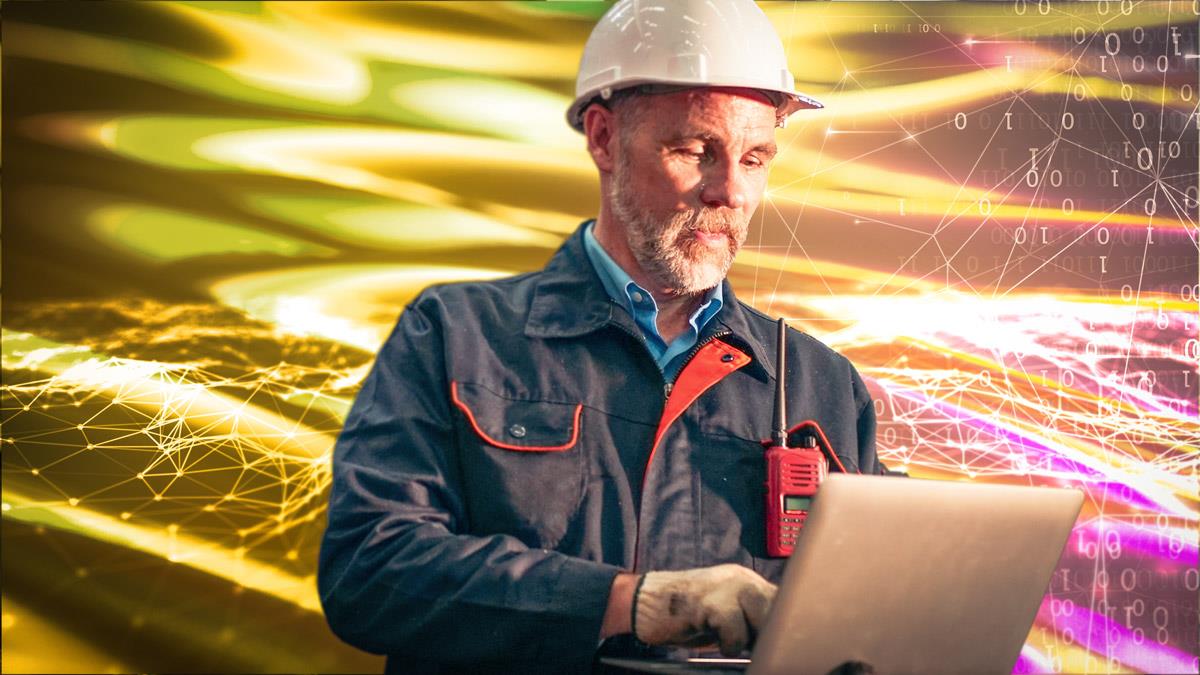
What is your preventative maintenance program designed to do? What are the objectives of your daily maintenance activities? Is it to maintain the machines toward higher reliability, or is it to maintain the status quo? If you’re trying to achieve something higher, keep in mind: if you do what you’ve always done, you’ll get what you’ve always gotten.
For better or worse, machine reliability is joined at the hip with lubrication, whether from a design or maintenance perspective. Proper lubrication ensures that machines run smoothly to minimize the negative impacts of friction and wear. But this isn’t one of those things you can just set and forget.
While lubrication is important, it can be fickle over time if it's not properly maintained. What begins as the healthy lifeblood of the machine can turn into the murderous poison within and lead to premature machine failure and unexpected downtime.
Today, maintenance and reliability have become revolutionized by
lubrication management systems (LMS) that help take the guesswork out of best-practice lubrication. And this doesn't just apply to the tangible lubricant, but rather lubrication, as a whole, and includes all facets of the process that influence the lubricant to perform at its optimum level. Understanding this concept is a core function in proper maintenance.
Holistically, there are
40 factors that should be considered for achieving machinery lubrication excellence. Some of these factors include choosing the optimal lubricants to use across a facility and how to properly receive and store them before use. And as this knowledge applies to day-to-day maintenance and the details associated with lubrication routes in a facility, you must ensure you perform three key processes properly:
lubricant application, contamination control, and
condition monitoring.
Before the Use of a Proper Lubrication Management System (The Status Quo)
Let’s take a typical process — pump asset train, for example — which includes two or three lubricated components: the electric motor, the pump, and the coupling. The status quo activities may include a periodic reminder to "add grease" or "inspect oil level" listed in a physical checklist.
This leaves the quality of the work dependent upon the technician’s level of training and availability, along with any exisiting practices already in place, to communicate any relevant information. Similarly, the pump and electric motor status quo often lack necessary modifications to allow for proper inspections or to protect from the surrounding contaminants.
By default, there is little standing in the way of:
-
Contaminant Ingression – Airborne contaminants entering the machine accumulate, cause friction, and degrade the lubricant.
-
Lubricant Misapplication (amount) – Both under-greasing and over-greasing lead to energy losses and heat generation due to lubricant starvation or viscous drag.
-
Lubricant Misapplication (type) – One of the most common mistakes made in lubrication is applying the wrong lubricant, often due to the lack of proper lubricant identification and labeling.
-
Inadequate Inspections (Inspection 2.0) – Without proper training and on-the-job guidance, more than 90% of inspectable conditions go unnoticed.
Correcting these practices and breaking the status quo requires change. Managing this change requires diligence and time but can be made easier with the right tools and processes. Machine reliability relies on best practices of lubrication performed daily through proper management systems. For many professionals who have been successful in managing these changes, the benefits are abundant and include cost reductions, reduced carbon footprint, and predictable machine operation, along with better job satisfaction for the workforce.
Lubricant Application
Effective lubrication is not just about using the right type of lubricant — it's also about applying it in the right quantity and frequency. An LMS manages each lubricated asset in a cloud-based database and establishes precise lubrication schedules based on equipment usage and manufacturer recommendations.
For example, installing an automated lubrication system, a subset control of the LMS, can deliver the exact amount of lubricant needed and eliminates the risk of over-lubrication, which can lead to energy wastage and component damage. But even standard tasks with a grease gun or a top up container must be carefully guided by best-practice procedures and documented in an LMS. Otherwise, with the status quo, mistakes made with these basic tasks are common and can lead to significant failure modes.

Contamination Control
Contaminants like dirt, moisture, and particles are notorious for compromising machinery performance. The LMS should prioritize contamination control through means of modification considerations, procedures, and condition monitoring. They often incorporate optimized selection of filtration, sealing, and breathers to prevent contaminant ingression and support contaminant removal from lubricated components. Using proper LMS tools, such as LubePM, can help guide which hardware to select for optimizing these needs.
Additionally, daily lubrication PM’s performed by technicians must be well-defined and managed to ensure these critical hardware items are performing as expected. The LMS tools, often accessible through a mobile device app, further help the technician know what to monitor and accurately report the status. This proactive approach allows for timely corrective actions to prevent equipment damage and unplanned downtime.
Inspections
The LMS emphasizes routine detailed inspections as a cornerstone of condition monitoring and overall effective maintenance. These systems facilitate the setup of regular inspection schedules, during which technicians can assess equipment condition through a series of specific questions and answering prompts. This helps support on-the-job training with example images, videos, etc., and also aides in the collection of data to complement other condition-monitoring technologies.
Lubricant Analysis
Regular lubricant analysis involves assessing factors like viscosity, contaminants, and the presence of wear particles. By monitoring these parameters, maintenance teams can identify early signs of lubricant degradation or component wear. The first step for lubricant analysis, oil sampling, must be done carefully, or it will compromise the value of the condition-monitoring technique, just like with inspections.
The LMS helps manage these activities by employing step-by-step procedures that reference best practices. Collecting a representative oil sample also requires a properly identified sampling point and sampling valves, which is recommended and defined within an LMS like LubePM. When done correctly, lubricant analysis empowers users to take preventive maintenance measures, such as scheduled lubricant replacement, before more severe issues arise.
Creating a New Status Quo
Industrial machines can no longer be expected to withstand rough operating conditions with a reactive mindset. There is no more room for that in today’s competitive industry. Since the beginning of machine design, lubrication has always been foundational to reliability. But it cannot be taken for granted.
A Lubrication Management System (LMS) is a dedicated tool that enables lubrication excellence in conjunction with the more holistic maintenance management of a CMMS or EAM. But it takes firm initiative to transcend traditional maintenance practices that have been locked into the status quo of maintenance culture for the last several decades. By deploying modernized tools such as LubePM to manage the entire lubrication program, much more efficient and streamlined workflows, combined with on-the-job job skills development, can be achieved. Take charge of your lubrication program with a systematic approach of an LMS.