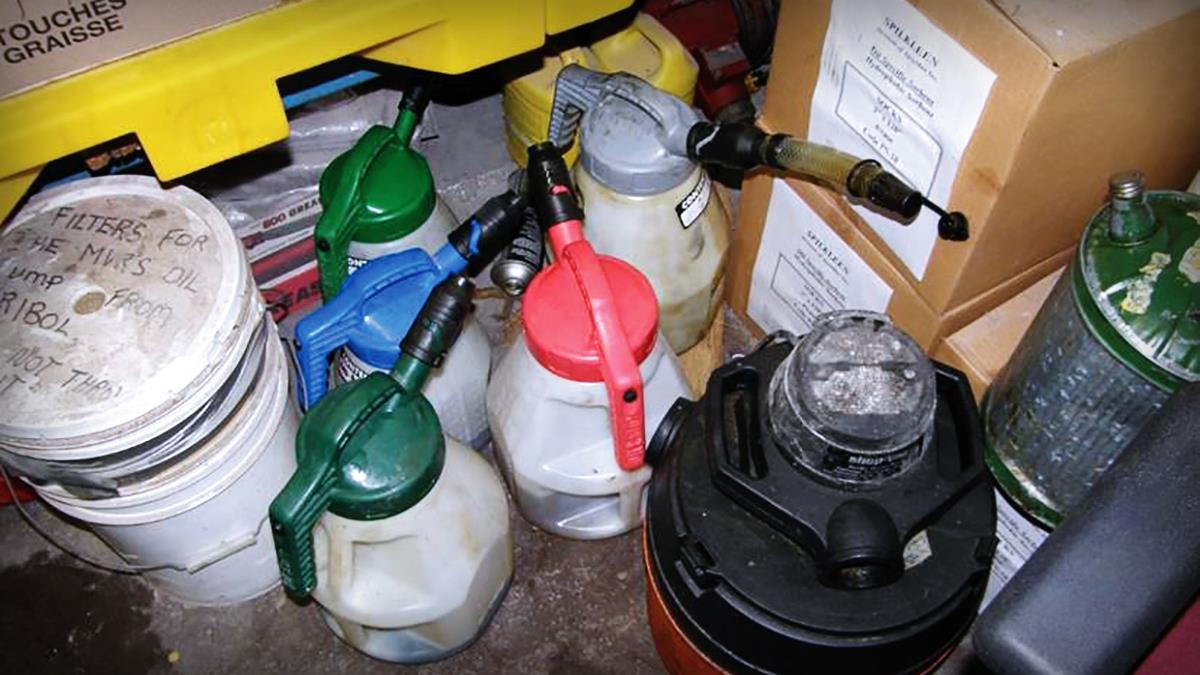
Manufacturing facilities are like my second home. Each year I visit sites all over the world conducting assessments that analyze the overall performance of their lubrication programs. During these assessments as I am documenting, photographing, and completing my list of 540 yes or no questions, I find opportunities for teachable moments.
It’s like living in your own house. You tend to walk past things multiple times a day. It takes an outsider to point something out that’s alarming. Improving your lubrication program today or this month is possible. Look at this list of common problem areas and answer the same questions I ask our clients during assessments. Your responses will be great conversation starters with your team.
The Main Offenders
-
Lube room
-
Lack of documented lubrication tasks and procedures
-
Contamination control
-
Oil analysis
-
Lack of training
-
Using appropriate tools
Lube Room
When
lube rooms are in a state of disarray, the health of the lubricants in the room comes into question. Questions we ask related to the state of a lube room include:
-
Do you have procedures for receiving lubricants?
-
Are you protecting lubricants in the lube room?
-
Are you filtering oils?
Lubricants should be taken care of before going into machines just like the food we protect in our pantries in refrigerators.
Lack of Documented Lubrication Tasks and Procedures
Transferring experiential knowledge from person to person is a traditional and somewhat effective way to learn to the job but it is not an effective way to keep tabs on a lubrication program. One should even be careful when relying on a
CMMS to run a lubrication program because it’s not built to hold those granular pieces of data like specific maintenance points. Proper documentation ensures all lubrication points are addressed, preventing missed points that could lead to equipment failure.
-
Are all lubricated points mentioned in the lubrication database?
-
Do all lubrication tasks have proper procedures?
-
Do these tasks mention the specific lubricant to use?
Contamination Control
Activities related to
contamination control have a large effect on the rest of the program. Storage practices like leaving open barrels and jugs or not protecting the lubricant during the transfer process from the lube room to the plant floor exposes your lubricants to contaminants. These particles will eventually end up in your machine. Protecting your machines from contaminants is paramount to the health and longevity of your equipment.
-
Are you receiving clean lubricants?
-
Are the proper steps being taken to protect the lubricant before it goes into the machine?
-
Are machines outfitted in a way to protect the lubricant once inside?
Photo of a hose obstruction
Training
Trained personnel understand the nuances of lubrication, such as why you shouldn’t mix lubricants and the importance of contamination control. They know the importance of applying lubricants correctly and completing tasks according to documented procedures. A trained team can completely change the trajectory of a lubrication program.
-
Do all personnel that have an active role in the lubrication program have a baseline knowledge of lubrication fundamentals?
-
Do those applying lubricants have specific training in lubrication training such as MLT I?
-
Do those managing the program have a more in-depth knowledge of advanced lubrication topics such as selection and degradation?
Oil Analysis
Have you heard the term “junk in, junk out?” The use of incorrect sample ports and lack of sampling procedures will produce inaccurate results. Confidence in the data you are receiving back from a lab is crucial to taking the right corrective action. So, it’s important to distinguish between a functioning
oil analysis program and an effective one.
-
Are there proper sampling ports on a machine?
-
Are the alarms and limits set up correctly by machine type?
-
Do those reading the reports have a thorough understanding of report interpretation?
Using Appropriate Tools
How many times have we been told, “use the right tool for the right job?” Improper tools like open-top transfer containers and funnels can put the lubrication program in jeopardy. Smaller tools and containers may seem insignificant but the impact these can have on contamination can’t be underscored enough.
Photo of a rusty oilcan
As I mentioned, I travel the world
conducting assessments that show facilities where their lubrication program stands on a score of 1 to 100. The
Ascend™ chart covers six weighted sections which contain 40 critical lubrication elements. Each weighted section deeply interconnects with the next. One underperforming area can have a domino effect on the rest.
One of the joys of my job is the education I get to share with eager workforces as I move with them from asset to asset. The lightbulb moments and ensuing success in equipment failures and downtime reduction is a testament to the importance of proper lubrication practices. Ready for your lightbulb moment? Take your free
self-assessment.