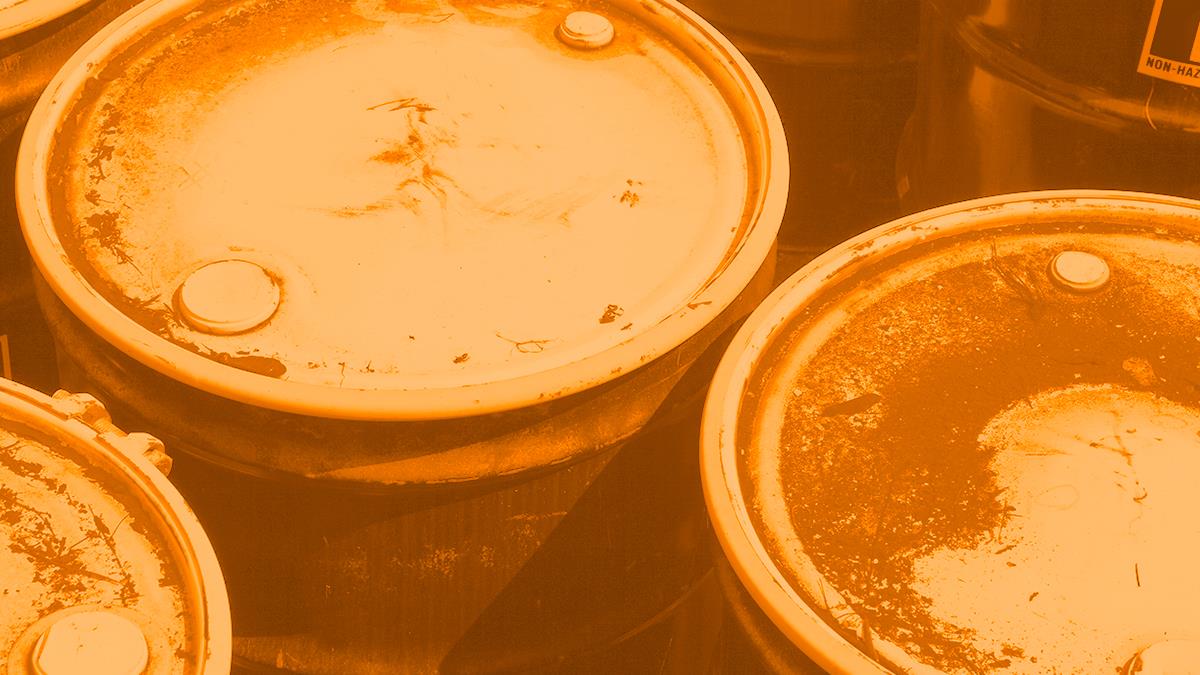
It is a fact that some 80% of machinery failures are related to lubrication. Of these, more than one-third result from the
contaminated lubricant. These facts highlight the need to ensure all lubrication systems remain pure and contaminant-free.
This article clarifies misconceptions surrounding the subject, names the prime causes, and recommends suitable prevention methods. It further highlights modern laboratory analysis methodologies, which point directly to the contaminants found, and highlights the need for accurate sampling techniques. Finally, case studies of mechanical failures due to contaminated lubrication systems are presented, along with the paths taken to prevent these.
Misconceptions Regarding Lubricants
It is overlooked that most liquid lubricants arriving at an enterprise receiving bay are already contaminated. This is not due to the lubricant manufacturer but primarily because the drum or canister does not meet ISO codes of internal cleanliness. In some cases, the cleanliness level and particulate matter's presence exceed this standard five to ten times. A straightforward method of ensuring this lubricant does not cause problems is to provide a
filter cart with appropriately selected beta-rated filters depending on the most stringent and critical application.
The second misconception is that lubricating grease is also pure, but once again, this is a fallacy. There are some methods of purification, the simplest being
filtration.
The Causes of Lubrication Contamination
Industrial lubrication systems can encounter various contaminants that degrade their performance and reliability. Some common contaminants include:
Ingressed Contaminants:
-
Dust, dirt, and airborne particulate from external sources
-
Moisture and subsequent rust, corrosion, soot, microorganisms, and other contaminations result from water contamination
-
Process contaminants
Generated Contaminants:
These contaminants can lead to various issues such as increased friction, wear and tear of machinery components, reduced efficiency of lubricants, accelerated corrosion, and overall decreased equipment reliability and lifespan. Therefore, effective filtration, regular monitoring, and maintenance practices are essential to mitigate these risks in industrial lubrication systems.
How Does Lubrication Oil & Grease Become Contaminated?
Lubricating oil and grease can become contaminated through various mechanisms and sources.
Contamination can occur during manufacturing, storage, transportation, or use within machinery and equipment. Here are some common ways lubricants become contaminated:
-
External ingress: Dust, dirt, sand, and other particulates can enter lubrication systems through vents, seals, or openings in equipment during operation or maintenance activities.
-
Water ingress: Water can enter lubrication systems through condensation, leaks, or washing processes. Water contamination can accelerate oxidation, reduce lubricant effectiveness, and lead to corrosion. (Always ensure that the item has a properly selected "breather" that prevents moist air from entering when the system cools down and inhalation occurs.)
-
Chemical contaminants: Chemical contaminants such as fuel, coolant, solvents, and cleaning agents can mix with lubricants during maintenance procedures or due to equipment malfunction.
-
Wear debris: Particles generated from the wear of components like gears, bearings, and seals can contaminate lubricants. Depending on the materials and conditions of operation, these particles can vary in size and composition.
-
Additive depletion: Over time, lubricant additives can deplete due to oxidation, thermal degradation, or chemical reactions, altering the lubricant's properties and potentially causing increased wear.
-
Microbial growth: In environments with water contamination and suitable conditions, microorganisms can grow in lubricants, leading to microbiological contamination that affects lubricant performance and stability.
-
Improper handling: Poor handling practices during lubricant storage, transfer, or replenishment can introduce contaminants from unclean containers, improper filtration, or inadequate sealing.
-
Cross-contamination: Lubricants can inadvertently mix with incompatible oils or greases during topping-up or maintenance activities, compromising their performance and potentially damaging equipment.
-
Environmental factors: Environmental factors such as temperature extremes, humidity, and exposure to airborne pollutants can contribute to lubricant degradation and contamination over time.
-
Operational conditions: Harsh operating conditions such as high temperatures, heavy loads, or extended service intervals can accelerate lubricant degradation and increase susceptibility to contamination.
What are the Indicators When Lubricators are Contaminated?
Contamination of lubricating oil (and sometimes grease) can lead to various indicators that can be observed through visual inspection, performance monitoring, and analytical testing. These indicators can be a direct indicator of contaminants (e.g., visible inspection or test for particulate) or observed through a consequence of contaminants present in the oil over time (e.g., with resulting oxidation or mechanical wear). Typical of these are:
-
Change in color and clarity: Clean lubricating oil is typically translucent and clear. Contamination can cause the oil to become cloudy, murky, or change color (e.g., darkening). For example, coolant contamination can cause a milky appearance, while oxidation may darken the oil.
-
Unusual odors: Contaminated lubricants may emit abnormal odors that indicate the presence of chemicals, fuel, coolant, or degradation products. These odors can range from sweet (coolant contamination) to acrid or burnt (oxidation).
-
Change in viscosity: Contaminants such as soot, sludge, or varnish can alter the viscosity of the lubricating oil. Increased viscosity can indicate contamination by solids, while thinning can occur due to fuel dilution or thermal breakdown.
-
Foaming: Contaminants like water or air can cause lubricating oil to foam excessively. Foam reduces the oil's ability to lubricate effectively and can lead to air entrainment in the system.
-
Abrasive particles: The presence of visible particles or sediment in the oil can indicate contamination by wear debris, dirt, or other solid contaminants. This can be best observed on a magnetic plus, such as in a bottom sediment and water (BS&W) bowl. These particles can cause abrasive wear and damage to components.
-
Increased wear metal levels: Analytical tests such as elemental analysis (Inductively Coupled Plasma Optical Emission Spectroscopy (ICP-OES) or Inductively Coupled Plasma Mass Spectrometry (ICP-MS) can detect elevated levels of wear metals (iron, copper, aluminum, etc.) in the lubricating oil. These metals indicate wear of components and potential contamination by abrasive particles.
-
Acid Number (AN) increase: An increase in the acid number of the lubricating oil indicates an increase in acid concentrations, often resulting from depleted antioxidants, oxidized base oil and contamination by acidic substances. This can accelerate the degradation and corrosion of metal surfaces.
-
Decreased additive effectiveness: Contaminants can react with or deplete the additives present in lubricating oil. This can reduce the effectiveness of additives such as anti-wear agents, detergents, dispersants, and antioxidants.
-
Increased oxidation: Contamination can accelerate oxidation of the lubricating oil, leading to increased viscosity, formation of sludge or varnish deposits, and degradation of oil properties.
-
Equipment performance issues: Contaminated lubricants can reduce equipment efficiency, increase friction and wear, overheat, abnormal noise, and overall performance deterioration.
-
Particle counting involves measuring particles' number and size distribution in the lubricant. It's often done using laser-based particle counters that can detect particles down to a few micrometers in size. Particle counting can also be done using pore-blockage techniques.
-
Ferrous density and ferrography: This technique uses a magnetic field to separate and analyze wear debris from the lubricant. Examining the particles' shape, size, and composition helps identify the source of wear (such as gears and bearings).
-
Spectrometric analysis: This includes techniques like infrared (IR) spectroscopy, elemental analysis), and chromatography (e.g., gas chromatography-mass spectrometry (GC-MS) which can help identify and quantify contaminants, such as fuel, coolant, or oxidation by-products, as well as metals from wear debris.
-
Water content analysis: Water is a common contaminant in lubrication systems. Techniques like Karl Fischer titration or infrared moisture analyzers can measure the water content in the lubricant.
-
Base Number (BN) decrease: This measures the alkalinity of the lubricant contributed by over-based detergents in motor oil. A decrease in BN can indicate blow-by contamination.
-
Patch test: Techniques like patch testing or gravimetric analysis can assess the cleanliness level of the lubricant by measuring the amount of solid contaminants present on a filter membrane.
These techniques are often combined to provide a comprehensive analysis of the contaminants present in lubrication systems. This allows maintenance teams to assess the condition of machinery and take appropriate corrective actions to prevent equipment failure.
Contaminant Prevention Case Histories
Case Study #1
During a lecture program presented to a prominent oil refinery on gearboxes, the issue of repeated failures in a series of ultra-large, ultra-heavy-duty units measuring more than 12 feet (3m) in height and critical to the continuity of operations was raised. As installed, these gearboxes had no oil purification method, and the recommendation was to design and install bypass filtration units that not only purified the oil but also cooled it. This potential solution resulted in
Mean Time Between Failures (MTBF) that exceeded the shutdown (turnaround) interval and had a major impact on production targets. A simplified but holistic diagram is shown below. This setup can vary depending on the complexity of the application.
Case Study #2
At a sugar milling factory where all the front-end units were hydraulically driven, exceptionally high costs were being incurred as all the equipment was supplied and serviced by a commercial supplier. The management asked to establish a hydraulics department, which resulted in the factory having a specialized workshop with trained staff to install and maintain all such equipment. Multiple changes were made to realize the zero downtime target. The oil brand was changed to what was recommended for the extremely heavy loading. The gear pumps were replaced with Swedish-made piston pumps installed below stainless steel oil reservoirs (flooded suction). The piston rings in these pumps showed minimal wear after five years of operation. They significantly improved in reducing wear compared to the original gear pumps (almost zero friction).
A hose crimping machine was donated, and the factory switched from screw-on fittings to crimped fittings, significantly reducing leaks. All hoses were made in-house, a hose register was created, and working hours/flexing was tracked as a method of planned replacement. Parallel return oil filtration units with 4-micron media were installed, with auto change-over activated by differential pressure control. The overall results of the oil purity tests were impressive, and substantial cost savings were achieved.