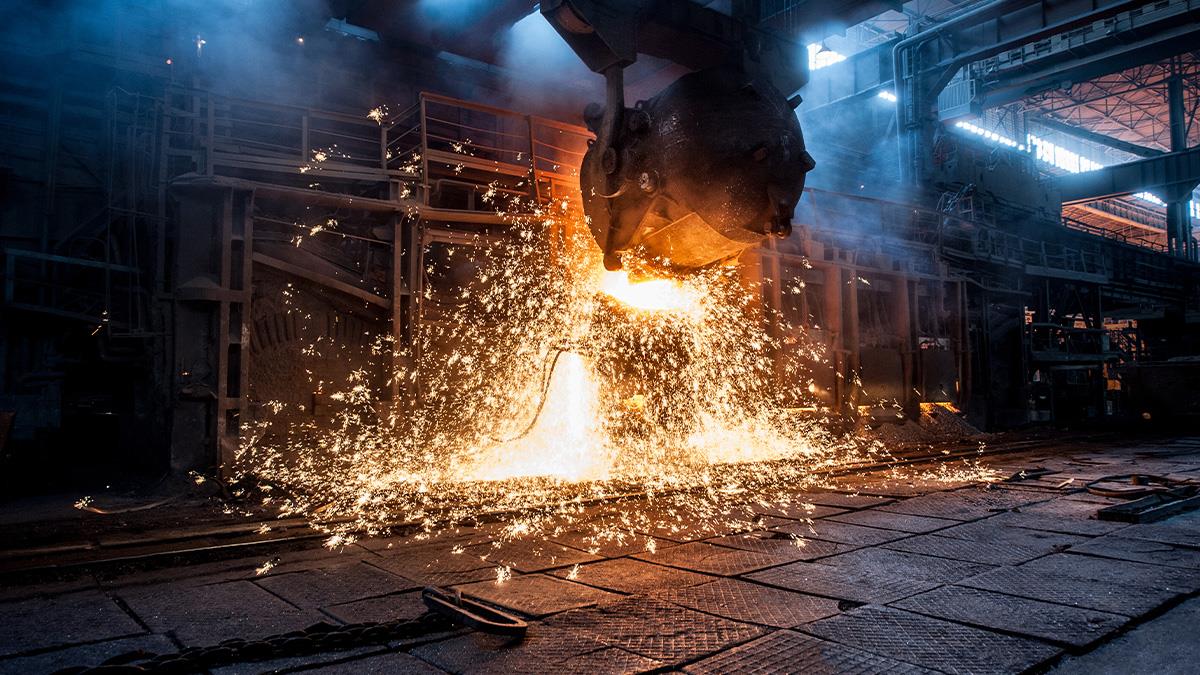
Condition monitoring, contamination control, lubrication excellence, and machine reliability are keywords that are often overused and misunderstood. These words are far more relevant and encompassing in today’s business context, but only a handful of organizations globally are able to implement these concepts simultaneously and successfully while maintaining sustainability.
This process isn’t always easy, but organizations can achieve this through intense, thoughtful effort and collective teamwork, and the resulting successes and benefits are widely documented.
For example, let’s examine a
case study with J.R. Simplot, a private food processing and agricultural company that owns and operates one of the largest high-grade phosphate mines in the Western United States.
A large fleet, including haul trucks, was needed to maintain the demanding mining operation schedule. On average, each engine had to be rebuilt every 15,000 operating hours, costing up to $160,000 per engine rebuild. This consumed nearly 70% of the company's total maintenance budget.
The team recognized that poor lubrication practices and human error were the primary root causes of their engine failures, and they decided to make a change.
By prioritizing
proper lubrication management standards and practices, the team increased the average operating hours between engine rebuilds by 37% to over 18,000 hours, leading to an annualized cost reduction of over $15,000. The team is currently working to increase the mean time between rebuilds to nearly 25,000 hours.
However, despite documented success case studies like this one, it has been observed that a new thought pattern is emerging.
Now, it seems that many organizations and leaders are more invested in talking about and promoting extending component life and practicing asset management and proactive maintenance on different platforms than implementing the needed changes.
This mindset of over-confidence in the principles without the action to support it can lead to a modern-day “counting your chickens before they hatch” scenario, meaning that mistakes are more likely to occur, risking the future of a plant transforming into a world-class facility.
The Steel Mill’s Shocking State
A few years ago, I had the opportunity to visit an older steel and wire rod mill in India to explore potential business opportunities.
My colleague and I visited the site on a typical day and stayed throughout the workday. Because of the mill’s location in India, it’s important to note that we were met with an extremely hot, humid, and dusty environment. We walked around the facility, interacted with managers, supervisors, and technicians, and collected a few oil samples using
proper sampling hardware accessories and sampling bottles.
What we discovered was a vastly different situation than we were expecting. We found:
-
Improper oil barrel storage
-
Thick layers of dirt on the body of barrels
-
Insufficient quantity, undersized, exhausted desiccant breathers
-
No maintenance tags
-
Oil storage, handling, and dispensing was done in an open atmosphere using hand pumps and small cans
-
Dirt was observed everywhere – floors, hydraulic oil tanks, breathers, parts storage area
-
No housekeeping process in place
Moreover, despite our repeated requests, the mill failed to provide any past data. This reluctance to share data may have been due to:
-
A lack of data
-
A lack of generating consent or accurate data
-
A data collection process simply did not exist
This historical data would be crucial for analyzing and understanding the fluid cleanliness level the machines were operating with and how they got to this state. Additionally, they would be needed to help guide future strategies and action plans for remediation.
Collecting, Testing, and Analyzing the Samples
The oil samples we collected were tested and analyzed that following day at our own lab. The tests we performed included:
-
Microscopic patch with 50X magnification
-
Particle count with standard laser particle counter
-
Wear metal analysis using Inductively Coupled Plasma (ICP) Spectroscopy
The patches were prepared using a manual microscope, and the particle count tests were performed using proper procedures inside the lab. Although not considered crucial in this scenario, the wear metal analysis was performed to understand the metal debris in the oil samples. The test revealed that while there were additive metals, such as zinc, calcium, and phosphorus, we did not find excessive metal content.
A Closer Look at the Lubrication Systems
In addition, when observing the mill’s industrial lubrication system, we found that the delivery lines were equipped with 25-micron and 10-micron absolute filters, and there were no return lines. In the hydraulic systems, the delivery line was fitted with a 5-micron absolute filter and the return line with a 10-micron absolute filter.
When looking at the refill tanks and lubrication systems, we discovered the mill still utilized the
NAS system standards, which have largely been phased out of every industry in favor of ISO standards. Despite becoming obsolete, the NAS system should have still been able to maintain some level of cleanliness.
However, when we consulted the particle count data, it confirmed our suspicions – the oils were extremely dirty and contaminated.
Several of the hydraulic systems operated with NAS 6 cleanliness (ISO equivalent of 17/15/12), and others operated with NAS 9 (ISO equivalent of 20/18/15) and even NAS 12 (ISO equivalent of 23/21/18).
The mill’s industrial lube oils also contained a high moisture content—about 2,000 parts per million (ppm), whereas the industry standard maximum is 200 ppm.
This information allowed us to draw the conclusion that most of their contamination issues were occurring because of human error and improper practices during lubrication storage and handling.
Conversations Come to a Close
With our tests and analysis complete, we sat down with the mill’s senior management team to review our data and findings. During this meeting, the management team revealed what their internal cleanliness requirements were:
This was absolutely shocking. When presented with our findings showing the severe discrepancies between facility cleanliness expectations and reality, the mill’s management team declined to offer any explanations and refused to discuss the matter further before abruptly ending the meeting.
Needless to say, all of our enthusiasm and initial activities related to discovering a business opportunity and creating a commercial proposal were quickly discarded.
While we may not be well-versed in every industry’s processes, one thing remains constant – contamination can affect every facility if proper precautions aren’t taken, and an understanding of principles doesn’t correlate to proper application. Confidence in knowing what the principles are without appropriate effort and action leads to an increased risk of human error, jeopardizing the plant’s ability to transform into a world-class facility.
Reflection
After careful reflection of my experience, these were several reasons why it becomes increasingly difficult to pursue a business relationship with this steel mill:
-
Proper cooperation and communication from mill leadership was missing from the beginning.
-
An aggressive approach toward proactive maintenance was not observed.
-
Neither the mill’s team members nor machinery was prepared or equipped to achieve an appropriate cleanliness standard.
-
All lubrication activities were performed in an open and dirty environment.
-
There was no process in place for properly handling, storing, and dispensing oils.
-
A contradictory approach towards standards – they set stringent requirements but implemented extremely poor practices.
-
Mill leadership was aware of the need to remove contaminants from the systems, but remained oblivious to the various procedures and techniques required to prevent contaminants from invading the systems.
-
Oil filters were left unprotected.
-
Fluid-carrying hoses and tubes were left open.
-
No processes existed to adequately clean and cover hoses.
-
The mill’s current filtration system was barely sufficient to bring down the NAS value from NAS 9 to the desired level of NAS 3, even if proper procedures were being followed.
-
Incorrect oil filter size selection at multiple locations.
-
There was no process for regularly monitoring or collecting data on the cleanliness of all oil samples in the facility.
While these reasons may make further business involvement difficult, this steel mill is unknowingly starving for a change catalyst. It could take just one individual with the right change management approach to trigger a series of positive events. This is about culture, and it starts with leadership.
To change the collective mindset of those currently unmotivated to recognize the opportunity, they need to discover “what’s in it for them.” We are creatures of habit, and we only change if there is a compelling reason. Until then, the status quo will persist, and the steel mill and the people within will suffer from unscheduled downtime and lost opportunities.
Looking Forward
I remember in the early 2000s, my lab was processing, testing, and analyzing an average of 100 samples per month. Today, this same lab is working through nearly 5,000 samples every month, with team members working in two shifts to complete the workload. This example creates a silver lining amid deplorable conditions, such as with the steel mill I visited.
In the future,
training must be at the forefront – not only for team members on the facility floor but also for upper management, which is responsible for designing and driving the implementation of new maintenance and lubrication programs. Because of this, the training not only needs to involve proper lubrication practices but also cultural transformation and change management, which is driven from the top down.
When intense, thoughtful effort is partnered with collective teamwork and intentional action, the benefits of a quality program are achieved, and the success stories begin to outweigh the failures.